-
- News
- Books
Featured Books
- pcb007 Magazine
Latest Issues
Current IssueInventing the Future with SEL
Two years after launching its state-of-the-art PCB facility, SEL shares lessons in vision, execution, and innovation, plus insights from industry icons and technology leaders shaping the future of PCB fabrication.
Sales: From Pitch to PO
From the first cold call to finally receiving that first purchase order, the July PCB007 Magazine breaks down some critical parts of the sales stack. To up your sales game, read on!
The Hole Truth: Via Integrity in an HDI World
From the drilled hole to registration across multiple sequential lamination cycles, to the quality of your copper plating, via reliability in an HDI world is becoming an ever-greater challenge. This month we look at “The Hole Truth,” from creating the “perfect” via to how you can assure via quality and reliability, the first time, every time.
- Articles
- Columns
- Links
- Media kit
||| MENU - pcb007 Magazine
Estimated reading time: 1 minute
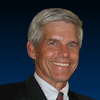
All About Flex: Lean Manufacturing and NPIP for Flexible Circuits
Many companies are familiar with lean manufacturing concepts and have successfully used these techniques to improve manufacturing processes. Lean techniques, while most often used in printed circuit fabrication and assembly operations, can also be applied to nonmanufacturing processes. One such process is new part number introduction (NPIP).
The main thrust of lean manufacturing is to eliminate or reduce waste. There are typically seven wastes (mudas), as defined by Toyota executive Taiicho Ohno, when he developed Toyota’s Production System (TPS)[1]. (“Muda” is a Japanese word meaning uselessness, idleness or other synonyms of waste.) The seven mudas are:
- Transport
- Inventory
- Motion
- Waiting
- Over-processing
- Over-production
- Defects
The typical part number startup for flexible circuits often can suffer from a number of those wastes. Certain waste items are specific to a part number (customer out of office, conflicts in documentation, iterative design conversations, etc.) or be ingrained as accepted gaps in a supplier’s product launch system. As part of a continuous improvement mentality, wastes should be identified for reduction through a documented and monitored part number introduction process. Some of the more common waste elements are:
Transport: In a new part number introduction process (NPIP), transport is the movement of documentation (electronic or paper) from one department to another requiring successive reviews and sign-offs. Excess transport is a symptom of a departmentalized approach to part number start-up rather than a process flow approach. A cross-functional design review team with one leader can remove departmental barriers and help assure that reviews and inputs are done in parallel rather than serially. Transport can also include sending information requests and approvals to customers and suppliers. These requests need to be challenged regarding their usefulness and necessity.
Editor's Note: This article originally appeared in the March 2016 issue of The PCB Magazine.
More Columns from All About Flex
All About Flex: Terms and ConditionsAll About Flex: ISO 9001 Basics
All About Flex: FAQs on UL Listings for Flexible Circuits
All About Flex: Avoiding Trace Fracturing in a Flexible Circuit
Polyimide vs. Silicone for Flexible Heaters
All About Flex: Copper Thickness Requirements for Flex Circuits
All About Flex: Copper Grain Direction
All About Flex: Options for Purchasing Flexible Heaters