Weiner’s World
May 2, 2016 | Gene Weiner, Weiner International Inc.Estimated reading time: 11 minutes
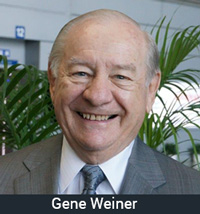
Editor’s note: This blog was originally published in April 2016 at Weiner Intl. and is being reprinted here with special permission from the author.
In Memoriam
We lost another icon this past month, Eugene (Gene) Ronald Selven. Although he had a long history in the semiconductor industry at such firms as TI, Fairchild, and Raytheon, many of us will best remember him as the publisher of Chip Scale Review for which I wrote a column for several years. Gene bought the journal from Tessera in 1999 and built it to prominence in the semiconductor industry. What I remember most about Gene was his insight and gentlemanly way of handling challenges. It was always a pleasure being with him to discuss the industry or to exchange "fish stories." Although he has been retired for a number of years, his passing last month has created a vacuum felt by many. Chip Scale Review continues today under the auspices of Kim Newman, Gene's daughter.
Other News
Presidential candidate Donald Trump singled out 3D printing in his first foreign policy speech as one of the advanced technologies that America should develop and protect.
The electro-deposited copper foil industry is booming in China, but not for PCBs and CCLs. The factories are running at full capacity for the battery industry. The significant portion is for electric cars. About 50,000 electric cars were sold in Shanghai alone in 2015. The margins are much better than for PCBs and CCLs, so it is anticipated that price and delivery issues will arise. The batteries are primarily made in Asia.
The market for assembly (SMT) equipment and robotics has improved substantially in China this month. It appears that some companies could no longer delay purchases of equipment that had been on hold. The same recovery has not yet been noticed for bare board fabrication systems.
In a recent It’s Only Common Sense column, Dan Beaulieu wrote, “And the cold hard fact is that the smaller guys are on their own. They have no one to look out for them, no one at all. Over the years, IPC has made it abundantly clear that they have a vast amount of interest in the big guys, but very little interest in the smaller shops.” Then Dan went on to list 10 advantages that he felt smaller fabricators have over the “big guys.”
I have a different view. The IPC does not work for any individual company. It does work for most companies if they actively participate together as a group in activities that are in their best, collective interests. IPC interacts with our government on behalf of all interconnect companies. It provides a vehicle whereby a class or group of members can get together and work on programs for their mutual benefit.
IPC is reinventing itself. It does more than just develop standards. It offers training for member companies and its employees. It provides focused showcases for its members’ products and services combined with a major conference every year. It recognizes that the electronic supply chain is changing and new solutions must be found as more and more systems bring silicone and components closer together in packages. It recognizes the global world of packaging and works to the benefit of all its members. It fosters cooperation and consortia to the benefit of its fabricators, assembly and packaging members…and industry.
IPC even has a VP in charge of member success. Changes are inevitable. Major consolidations have reshaped the industry. Supply chains are changing. Those that wish to avoid the fate of buggy whips should rethink their company strategies.
To this end, I am working towards presenting a PCB Executive Forum, under the auspices of the IPC, to be held at the next IPC APEX EXPO event in San Diego in February 2017. It will be focused on helping the smaller companies overcome today’s industry challenges. It will be designed to help CEOs, presidents and company owners solve some of the problems they face in today’s environment. All members of the bare board fabricating community, as well as their supply chain, will be invited to attend—even if they are not currently members of the IPC.
Chinese Counterfeiters Caught with the Goods
Daofu Zhang, 40, of Shenzen, China, pleaded guilty this month in New Haven (CT) federal court to conspiring to sell counterfeits of sophisticated integrated circuits to a purchaser in the United States. His co-conspirator Yan proposed to supply the U.S. source with “fake” ICs that “look the same,” to replace the ones to be stolen from the military. Yan and another co-conspirator, Zuo, were also apprehended and pled guilty last month. The case is being prosecuted by Assistant U.S. Attorney Henry Kopel* and U.S. Department of Justice Counterintelligence and Export Control Section Trial Attorney Casey Arrowood.
(*Kopel is the son-in-law of Gene Weiner, publisher of Weiner’s World.)
A Prediction Long Coming
Taiwan-based PCB players are pushing into car-use products as demand for PCs, smartphones and tablets has been weakening. Chin Poon (experiencing record profits) and Tripod Technology, which have been operating in the car-use PCB market for a long time, are looking to expand their presence in the market, while newcomers including Unitech, Unimicron Technology, Global Brands Manufacture (GBM), Apex International, Zhen Ding Tech, and Ichia have been trying to catch up. With demand for smart car applications including Internet of Things (IoT), semi-auto drive, infotainment systems, around-view monitoring systems, parking sensors and portable navigation device growing rapidly, demand for related upstream components such as PCBs is rising, and many PCB makers are aggressively looking to grab a share of the market. Car-use components require certification from car vendors, and the process usually takes more than 2−3 years. (Source: DIGITIMES, April 14)
A senior ADI manager said to us, "Today, automotive is everything!"
We just received a solicitation from a board fabricator offering the following:
-Express PCB Prototyping (2–40 layer)
-HDI PCB with 4 mil laser holes—flexible printed board (1–8 layer)
-Flexi-rigid printed board
-High-frequency board (Rogers, Arlon, PTFE)
-Blind/buried via board
-High Tg thick copper PCB (up to 12 oz. with TG210)
-Mix-material (FR-4+Rogers) multilayer PCB
-Embedding resistance/capacitance board
-Halogen-free/lead-free board
-Thick gold plating/immersion gold/ENEPIG board
Yep! You guessed it! It came from China. How many of America's remaining 200 or so board builders (excluding those "giants" with multi hundred millions in sales) can match all of the listed 11 items as a service? Do you consider the ability to build lots of 20 or 100 complex HDI boards at a time in a secure U.S. location necessary for America's defense? If so, who will support the acquisition of the capital equipment needed to do so? Who will provide (pay for) the expensive secured digital network required by prime contractors (Raytheon, Lockheed, Boeing, etc.)? The latter could cost up to a million dollars—a bit on the rich side for shops with an annual turnover of just $10 or $15 million or so.
Caveat Emptor
The April 15 online edition of PCB Update had a column by Peter Bigelow, president and CEO of IMI, which offers very sound advice worth repeating in the wake of a number of recent industry false starts and overly ambitious claims. A very brief excerpt is below:
“Be judicious when studying ‘game-changing’ technologies! Improvements pitched as being the elusive ‘one size fits all’ breakthrough usually are not. We must be diligent, using rigorous analysis and verification, to avoid processes that are oversold but underperform. If a new material, machine, or process simplification does not improve overall quality, add to overall capability, or have a measurable, favorable impact on cost, it most likely is not worth the effort. Many very interesting and promising technologies may be game-changers for us all. However, some, such as conductive inks, have been around for decades but are still just not ready for prime time. Others may have the potential to transform the industry in ways unimaginable just a few years ago. We need to be aware and inquisitive about all but not allow ourselves to become too mesmerized by any until they demonstrate tangible and proven value.”
Intel said it plans to reduce its global workforce by up to 12,000 jobs, or 11%, as the semiconductor giant reported a worse-than-expected 7% increase in first-quarter revenue. The chip maker said the job cuts are part of the company's restructuring away from a computer-based company to one that powers the cloud and billions of connected computing devices. (Source WSJ)
The joint IPC APEX−HKPCA show in Shenzhen China is now the largest in the printed circuit industry. It will be about 500,000 square feet at the next edition in December 2016. That's four times the recent IPC event in Las Vegas.
BPA’s short term PWB forecast for 2016 is essentially flat with different segments increasing or declining as in the following summary:
- Consumer—falling levels of demand
- Automotive—healthy demand and a bright spot supported by new applications
- High speed equipment—steady demand
- Computers—flat or decline
- Medical and industrial—steady demand growth
- Handsets—flat
- Military—flat
- Aerospace—steady demand
BPA’s 2016 worldwide semiconductor forecast suggests that we will see a flat year to a single figure contraction (in semiconductor value terms) of shipments as compared to 2015. With the macro economic factors as they are at the time of writing, the analysis would conclude that 2016 sales growth will be flat compared to 2015. However, the less optimistic outcome (supported by the semiconductor forecasts), may well be a contraction of 3−5%.
Page 1 of 2
Testimonial
"The I-Connect007 team is outstanding—kind, responsive, and a true marketing partner. Their design team created fresh, eye-catching ads, and their editorial support polished our content to let our brand shine. Thank you all! "
Sweeney Ng - CEE PCBSuggested Items
How Good Design Enables Sustainable PCBs
08/21/2025 | Gerry Partida, Summit InterconnectSustainability has become a key focus for PCB companies seeking to reduce waste, conserve energy, and optimize resources. While many discussions on sustainability center around materials or energy-efficient processes, PCB design is an often overlooked factor that lies at the heart of manufacturing. Good design practices, especially those based on established IPC standards, play a central role in enabling sustainable PCB production. By ensuring designs are manufacturable and reliable, engineers can significantly reduce the environmental impact of their products.
50% Copper Tariffs, 100% Chip Uncertainty, and a Truce
08/19/2025 | Andy Shaughnessy, I-Connect007If you’re like me, tariffs were not on your radar screen until a few months ago, but now political rhetoric has turned to presidential action. Tariffs are front-page news with major developments coming directly from the Oval Office. These are not typical times. President Donald Trump campaigned on tariff reform, and he’s now busy revamping America’s tariff policy.
Global PCB Connections: Understanding the General Fabrication Process—A Designer’s Hidden Advantage
08/14/2025 | Markus Voeltz -- Column: Global PCB ConnectionsDesigners don’t need to become fabricators, but understanding the basics of PCB fabrication can save you time, money, and frustration. The more you understand what’s happening on the shop floor, the better you’ll be able to prevent downstream issues. As you move into more advanced designs like HDI, flex circuits, stacked vias, and embedded components, this foundational knowledge becomes even more critical. Remember: the fabricator is your partner.
MKS’ Atotech to Participate in IPCA Electronics Expo 2025
08/11/2025 | AtotechMKS Inc., a global provider of enabling technologies that transform our world, announced that its strategic brands ESI® (laser systems) and Atotech® (process chemicals, equipment, software, and services) will showcase their latest range of leading manufacturing solutions for printed circuit board (PCB) and package substrate manufacturing at the upcoming 17th IPCA Show to be held at Pragati Maidan, New Delhi from August 21-23, 2025.
MKS Showcases Next-generation PCB Manufacturing Solutions at the Thailand Electronics Circuit Asia 2025
08/06/2025 | MKS Instruments, Inc.MKS Inc, a global provider of enabling technologies that transform our world, today announced its participation in Thailand Electronics Circuit Asia 2025 (THECA 2025), taking place August 20–22 at BITEC in Bangkok.