-
- News
- Books
Featured Books
- smt007 Magazine
Latest Issues
Current IssueIntelligent Test and Inspection
Are you ready to explore the cutting-edge advancements shaping the electronics manufacturing industry? The May 2025 issue of SMT007 Magazine is packed with insights, innovations, and expert perspectives that you won’t want to miss.
Do You Have X-ray Vision?
Has X-ray’s time finally come in electronics manufacturing? Join us in this issue of SMT007 Magazine, where we answer this question and others to bring more efficiency to your bottom line.
IPC APEX EXPO 2025: A Preview
It’s that time again. If you’re going to Anaheim for IPC APEX EXPO 2025, we’ll see you there. In the meantime, consider this issue of SMT007 Magazine to be your golden ticket to planning the show.
- Articles
- Columns
Search Console
- Links
- Media kit
||| MENU - smt007 Magazine
Making Systems Smarter to Gain Visibility, Traceability, and Reduce Handling Errors
May 20, 2016 | Stephen Las Marias, I-Connect007Estimated reading time: 2 minutes
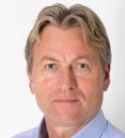
Based in California, KIC is focused on the thermal process—basically making reflow ovens smarter through profiling, automation, data analytics and sharing, and optimization solutions. The company essentially has three product categories. The first is a manual profiler. If you look at a reflow oven and ask yourself, “What is the job that the reflow oven is supposed to do?” It is to process an assembly within the specifications set by the solder paste components and so forth. That’s matched up with a profile—KIC’s system measures that profile manually and can compare that to the required process window.
The company also has software that can optimize the oven setup. Last, but not least, KIC offers automation solutions. The company integrates sensors into the oven to enable on-the-fly measurement of the profile for every assembly going through and checking to see if it’s in spec.
At the recent IPC APEX EXPO event in Las Vegas, I interviewed Bjorn Dahle, president of KIC, to learn more about his views on automation, the technology improvements being made in reflow ovens, and strategies to reduce handling errors in assembly lines.
Stephen Las Marias: How is your technology improving the reflow process?
Bjorn Dahle: The thermal process has kind of been seen as the black box process in a production line. You don’t really know what’s going on inside there. You hope for the best, and traditionally you check that once a day or once a month, and hope that in between your spot checks that everything is doing okay. More and more now, customers want more transparency; they want to know what’s going on, not once a day or once a month, every single board. Is it being processed in spec? They want to have access to that information so there’s process traceability available later on. Transparency and traceability are very big. There is now a number of new needs developing as people are getting into more smart machines and smart factories.
When we install sensors in the oven, it’s almost like installing a video camera. We film, if you will, the thermal process and, in real time, we can then make sure that no boards are being processed out of spec. You get an instant alarm, and we can provide SPC charting and CPK numbers, so you also get an early warning when your process is out of control. Historically this information has been contained at the oven, on the oven PC.
More and more now, you want that transparency to go beyond just the operator or the process engineer on the line, so we can send this information on to, let’s say, an MES system where now the information is shared with up and downstream the production line, and with all the other production lines. Clients now have access to this for their own products if they use an MES, and you get full traceability and transparency.
Editor's Note: This article originally appeared in the May 2016 issue of SMT Magazine.
Suggested Items
Marcy’s Musings: Countdown—The Fabricator’s Guide to IPC APEX EXPO
02/18/2024 | Marcy LaRont -- Column: Marcy's MusingsLike any great tech industry event, IPC APEX EXPO pushes us out of our busy 24/7 manufacturing bubbles. It forces us to pay attention to things that are important but not always present in our day-to-day lives. But there is so much to see and do. This issue of PCB007 Magazine previews many of the important events taking place at the show this year and highlights some changes and opportunities. Let us help you map out your show plan. This issue is focused on the PCB fabricator’s show experience and how you can get the most from your valuable time and investment in attending the show. So, buckle up. We are counting down to IPC APEX EXPO 2024.
Averatek to Present 'Surface Treatment for Soldering Aluminum PCBs to Conventional Copper PCBs' at IPC APEX EXPO
10/29/2021 | AveratekAveratek is pleased to announce that VP of Manufacturing Divyakant Kadiwala will present the paper entitled, “Surface Treatment for Soldering Aluminum PCBs to Conventional Copper PCBs” during the IPC APEX EXPO Technical Conference, scheduled to take place Jan. 22-27, 2022 at the San Diego Convention Center in California.
IPC APEX EXPO 2022 Attendees Can Achieve Digital Transcendence at Show Networking Events
10/13/2021 | IPCIPC APEX EXPO 2022 attendees can meet with electronics industry innovators and connect with peers all in one place at the San Diego Convention Center, January 22–27, 2022.
Foundations of the Future: IPC Education Foundation Lessons Learned
06/29/2021 | IPC Education Foundation -- Column: Foundations of the FutureLooking back on our second year, the IPC Education Foundation (IPCEF) takes pride in how we how we adjusted our engagement initiatives during the pandemic. We couldn’t rely on our original strategy of hosting and attending a range of in-person activities and events.
Dave Bergman on IPC and CFX
07/03/2018 | Barry Matties, I-Connect007The recent SMT Hybrid Packaging show in Nuremberg, Germany, marked the second opportunity for IPC to showcase its new Connected Factory Exchange (CFX) initiative. In this interview, David Bergman, VP for international relations at IPC, tells us more on the overall reception of CFX and the benefits users are seeing thus far. He also provides an update on what’s next for the open source standard.