-
- News
- Books
Featured Books
- smt007 Magazine
Latest Issues
Current IssueIntelligent Test and Inspection
Are you ready to explore the cutting-edge advancements shaping the electronics manufacturing industry? The May 2025 issue of SMT007 Magazine is packed with insights, innovations, and expert perspectives that you won’t want to miss.
Do You Have X-ray Vision?
Has X-ray’s time finally come in electronics manufacturing? Join us in this issue of SMT007 Magazine, where we answer this question and others to bring more efficiency to your bottom line.
IPC APEX EXPO 2025: A Preview
It’s that time again. If you’re going to Anaheim for IPC APEX EXPO 2025, we’ll see you there. In the meantime, consider this issue of SMT007 Magazine to be your golden ticket to planning the show.
- Articles
- Columns
Search Console
- Links
- Media kit
||| MENU - smt007 Magazine
Selecting a Selective Soldering System, Part 2
May 30, 2016 | Robert Voigt, DDM NovastarEstimated reading time: 1 minute
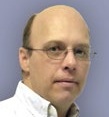
Our last chapter began a discussion of selective soldering, including how it works, some pros and cons, and several fluxing and soldering options to choose from. In this chapter, we’ll dive a little deeper into the mechanics of fluxing systems.
Flux Materials
As covered in prior chapters on wave soldering, there are a variety of flux types and chemistries available, including low pH, high-solids content, and water soluble, alcohol-based, and others. Selection of a particular type of flux is frequently not an option for the contract manufacturer, since it is usually determined by the end-user’s application, so they must be able to accommodate work using many types of flux.
No-clean fluxes are generally preferred because they require little to no post-solder cleaning, except for a visible residue that should be removed. If the user opts not to use a no-clean flux, it is very important to control the amount of flux applied to the board. In most cases, controlling the solder head to cover the area previously sprayed will burn off the flux and eliminate the necessity of cleaning the residue in a subsequent step.
Remember that solder types used for selective must be compatible with solder used on the top of the board, and this will likely have a material effect on the flux type used.
Spray Fluxing
Through-hole penetration is the ultimate goal of any fluxing system, but there are a number of factors that affect the performance of a spray fluxing system.
Editor's Note: This article originally appeared in the May 2016 issue of SMT Magazine.
Suggested Items
How to Specify a Custom Machine
09/16/2016 | Robert Voigt, DDM NovastarLet’s say you have an unusual product configuration, a unique space requirement, an unorthodox handling system, or an application totally unrelated to the PCB or SMT assembly business, and you can’t find a standard machine provider that can handle your requirements. What then? This article highlights key points to consider when going the custom machine way for your project.
DDM Novastar Schedules Fall Technical Workshop
08/22/2016 | DDM Novastar Inc.DDM Novastar will be holding a technical workshop on the fundamentals of paste, place and reflow, to be held from September 14–15, 2016 at the company’s facility in Pennsylvania, U.S.A.
DDM Novastar Delivers Custom Pick-and-Place Machine
08/16/2016 | DDM Novastar Inc.DDM Novastar has shipped a custom pick-and-place machine to a large multinational laser cutting tool manufacturer.
Selecting a Selective Soldering System, Part 5
08/08/2016 | Robert Voigt, DDM NovastarFor the conclusion of his series on selective soldering discussion, Robert Voigt does a quick wrap-up to remind potential buyers about some important considerations that affect the purchase decisions they make.
Improving Test and Inspection
07/05/2016 | Stephen Las Marias, I-Connect007In our recent survey on PCBA test and inspection challenges, respondents consider the following to be among their biggest problems: probing to narrower traces and pads; testing boards with smaller and finer features and sizes; dry solder and other solder-related issues; finding sublayer defects; dealing with flat, no-lead components; and testing cycle time. This month, we look into different PCBA test and inspection strategies that address the key challenges in today’s electronics manufacturing and assembly environment.