-
- News
- Books
Featured Books
- smt007 Magazine
Latest Issues
Current IssueIntelligent Test and Inspection
Are you ready to explore the cutting-edge advancements shaping the electronics manufacturing industry? The May 2025 issue of SMT007 Magazine is packed with insights, innovations, and expert perspectives that you won’t want to miss.
Do You Have X-ray Vision?
Has X-ray’s time finally come in electronics manufacturing? Join us in this issue of SMT007 Magazine, where we answer this question and others to bring more efficiency to your bottom line.
IPC APEX EXPO 2025: A Preview
It’s that time again. If you’re going to Anaheim for IPC APEX EXPO 2025, we’ll see you there. In the meantime, consider this issue of SMT007 Magazine to be your golden ticket to planning the show.
- Articles
- Columns
Search Console
- Links
- Media kit
||| MENU - smt007 Magazine
The Henry Ford Division of Labor Production Model
May 31, 2016 | Tom Borkes, The Jefferson ProjectEstimated reading time: 2 minutes
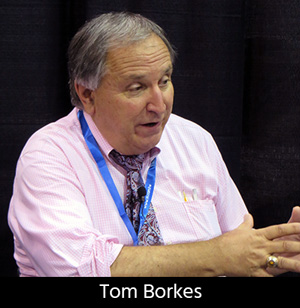
Last month, in my inaugural column entitled, "The Importance of Being Ernest (Educated)", I identified U.S. academia as “the emperor with no clothes” because of their self-congratulatory nature—reveling in buzz acronyms like STEM, and suggesting that decades of a continually widening gap between academic preparation and industry needs in high-tech electronic product assembly has been magically closed just by talking about the “new religion,” when, in actuality, little has changed.
I went on to talk about the need to complement an undergraduate engineering curriculum of primarily "learning for learning" with a commensurate dose of “learning for earning.” Our industry has failed to challenge the “emperor” since our industry's domestic competition has been faced with the same education level of employees that they hire out of school.
However, I indicated that the competitive landscape over the decades has changed in several important ways, as we have continued to tolerate the ill-prepared entry-level employee:
1. Low labor-rate global competition
2. The need for high engineering skill level employees to develop and maintain the leading-edge automation needed to reduce labor content as a way to compete with low labor-rate dollars. In other words, everything else being equal, if your direct labor rate is 10x more than your competition, but you find a way to reduce the labor content (labor hours) of a particular product by a factor of 10, you have removed the low labor rate competitive advantage—assuming that the low labor rate competition isn’t able to automate as well. This rarely happens with minimum wage operators and support technicians (process “engineers”).
Since, everything else being equal, one’s labor cost is simply the number of labor hours needed to build a product multiplied by one’s labor rate (or, more accurately, one’s labor sell rate).
Of course, “everything else” isn’t equal, and "el diablo esta en los detalles!"
I concluded the column by listing a number of "core issues" that, if not addressed, will continue to have us wallow in good intentions without ever seeing a tangible improvement.
For this month, the topic is The Henry Ford division of labor production concept.
We are all aware of what the price of assembling a product is based upon:
• Material cost (assuming the assembler purchases the material);
• Number of labor hours needed for the product assembly and test; and,
• Labor sell rate in dollars per hour.
The material cost, although seemingly uncontrollable, is crucially important and will be the subject of an upcoming column in this space. However, at this time we want to drill down into the labor sell rate to see what pops up out of the ground.
Editor's Note: This article originally appeared in the May 2016 issue of SMT Magazine.
Suggested Items
Turning the Relationship Between the Electronic Product Assembly Employer and Recent Graduates Upside Down
01/27/2017 | Tom Borkes, The Jefferson ProjectThe post-secondary educational system must change from being reactive to our industry’s (high tech electronic product assembly business) needs to being proactive. Students that graduate should act as change agents, challenging a company’s status quo by bringing the latest design, production equipment and process techniques to their new employers from their academic experience.
Moving Beyond Paideia: Learning for Earning
08/11/2016 | Tom Borkes, The Jefferson ProjectThe complexities of our technological world and global marketplace now demand the development of specific, saleable skills as part of the student-customer's educational process--and that the template for teaching these skills must be based in the real world. Tom Borkes explains why in this article.
The STEM Trap
08/03/2016 | Tom Borkes, The Jefferson ProjectPost-secondary schools have not been responsive to the changing landscape of the modern electronic product assembly operation—they really can’t, considering the lack of real-world experience of most of the faculty. In this article, Tom Borkes explains why.
The Importance of Being Earnest (Educated)
05/11/2016 | Tom Borkes, The Jefferson ProjectThis new column in SMT Magazine, titled "Jumping Off the Bandwagon," is dedicated to the continued development and improvement of the high-tech electronic product assembly industry, and the human component of that industry. For his first article, Tom Borkes talks about issues that, unless addressed, will continue to put product assembly at a disadvantage in high labor rate areas of the world.
The Jefferson Project, Part 2: Automation as a Counterweight to Low Labor-Rate Assembly
02/10/2016 | Patty Goldman, I-Connect007In Part 1 of this interview, Tom Borkes, founder of The Jefferson Project and the forthcoming Jefferson Institute of Technology, provided his well-researched plan to introduce students to tech manufacturing, as well as discussed the paper he presented at SMTAI. In Part 2, Tom expands on the example set forth in his SMTAI paper, and describes another important tool in reducing labor cost through the reduction of labor content: designing for automation.