-
- News
- Books
Featured Books
- pcb007 Magazine
Latest Issues
Current IssueInventing the Future with SEL
Two years after launching its state-of-the-art PCB facility, SEL shares lessons in vision, execution, and innovation, plus insights from industry icons and technology leaders shaping the future of PCB fabrication.
Sales: From Pitch to PO
From the first cold call to finally receiving that first purchase order, the July PCB007 Magazine breaks down some critical parts of the sales stack. To up your sales game, read on!
The Hole Truth: Via Integrity in an HDI World
From the drilled hole to registration across multiple sequential lamination cycles, to the quality of your copper plating, via reliability in an HDI world is becoming an ever-greater challenge. This month we look at “The Hole Truth,” from creating the “perfect” via to how you can assure via quality and reliability, the first time, every time.
- Articles
- Columns
- Links
- Media kit
||| MENU - pcb007 Magazine
Estimated reading time: 5 minutes
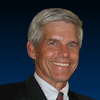
Imaging Methods for Etch Resist, Part 2: Photoimaging
This is the second of three columns describing typical methods for creating an etch resist for fabrication of printed circuits. To read Part 1, which discussed screen printing, click here.
A basic overview of the process for photo exposing etch resist would be:
- The flexible substrate is coated with photosensitive resist
- The resist coated substrate is positioned under a high intensity UV light source
- A phototool is aligned to the coated substrate
- A UV light floods the area, allowing light to expose the resist through selective openings in the photo tool
- The resist is developed and the unwanted resist is washed away
- The copper pattern exposed by removed resist is chemically removed (i.e., etched)
- The resist is stripped off so that only the copper pattern remains
The Photoresist Material
Photoresist can come in the form of a liquid that gets coated on the substrate or as a dry film that is laminated. Liquid and dry film resist can be positive-acting or negative-acting. A resist is positive-acting when exposure to UV radiation results in a photo-chemical change that allows the exposed resist to be developed away while the unexposed resist remains. A resist is negative-acting when exposure to the UV radiation allows the exposed resist to harden to the developing chemicals and remain during etching, while the unexposed resist would get washed away.
Liquid Photoresist
There are a variety of methods used for coating a liquid photoresist, including dipping, spraying, screen printing, reverse roll coating and electrostatic coating. Dipping is probably not suitable for the large, flimsy panel sizes that are common in flexible circuit fabrication.
After coating, the resist needs to be dried to a tack-free state so it can be handled and allow the phototool to contact it. It is also possible to use resists can remain a liquid through the process. This works in a process where coating, exposing, developing, etching and stripping are performed as a continuous “inline” process.
Dry Film Photoresist
Imaging Methods for Etch Resist, Part 2: Photoimaging
This is the second of three columns describing typical methods for creating an etch resist for fabrication of printed circuits. Photoresist can come in the form of a liquid that gets coated on the substrate or as a dry film that is laminated. Liquid and dry film resist can be positive-acting or negative-acting.
Dry film is by far the most commonly used photoresist material for processing printed circuits—both flexible and rigid. The flexible dry film resist is hot roll laminated onto the substrate with controlled temperature and pressure. To prevent the dry film from “blocking” during storage, a 1-mil poly film is bonded to the exposed side. This film is removed immediately before developing.
There are advantages and disadvantages for liquid versus dry film. Liquid resist can be coated much thinner than dry film which typically comes in 1.5 mil or 2.5 mil thicknesses. The dry film has a 1-mil poly layer that slightly diffracts UV radiation and reduces the resolution. Liquid resist tends to give better resolution which is why it is used in integrated circuits (ICs) that require line width and spacing down to 50 nanometers (.001” inch is 25,400 nm). For flexible circuit applications, the resolution that a liquid resist enables is not necessary. The other advantage for liquid resist is material usage and cost. Dry film resist comes in standard widths and can result in waste if the panel size is narrower than the dry film.
Photo Exposing
Once the substrate is coated with resist, it is aligned to a phototool. The photo tool has a patterned emulsion or coating that selectively blocks the UV light. Ideally the phototool is placed in intimate contact with the substrate. The intimate contact is often created by drawing a vacuum between the phototool and surface. For a non-collimated light source, any small gap can cause “light bleeding” and degrade the resolution of the image. Even with intimate contact, a non-collimated light source will expose a slightly wider area than the phototool image.
Many circuit fabricators use equipment with highly collimated light which reduces the need for intimate contact between the phototool and substrate. Collimated light will duplicate the photo image to a higher level than non-collimated light. Figure 1 and 2 demonstrate the difference between a collimated and non-collimated light source.
Once the resist has been exposed, it is sprayed or submerged in a developing solution that (in the case of a negative resist) washes away the unexposed resist and forms the pattern of the desired circuit traces. After etching, the remaining resist is stripped off. Developing, etching and stripping are commonly done with in-line equipment modules as a single process step (DES).
Potential Quality and Productivity Issues
There are a number of variables that need tight control in order to achieve acceptable yields.
Foreign Material
Particles which include dust, hair, skin flakes, and cloth fibers can cause defects at a number of points during this process. When applying the resist, it is critical to avoid “capturing” foreign material within the coated resist to avoid imaging flaws during exposing and developing. Foreign material will block or diffract light causing unwanted conductor width and spacing violations.
Light Bleeding or Diffracting
For a non-collimated light source, any tiny air gap between the phototool and resist can result in light “leaking” and exposing more resist than intended. A smudge, smear or scratch on the photo tool will result in a potential defect. Phototools must be carefully inspected before use. A slight change in surface on the phototool can diffract even the highest collimated light source and result in light bleeding to unwanted areas.
Exposure Level
Exposure levels are closely controlled. Over exposure will result in a larger area of resist cured than desired with some side-to-side cross linking occurring during exposure. Under exposure will result in narrower patterns than desired. Photoimaging equipment often has “built in” radiometers that will adjust dwell time to a set exposure level. The UV radiation level will decline slightly as the bulb ages, so dwell time may need to be increased to maintain a constant exposure level.
Developing
While the process window for developing is quite large, under- or over-developing will result in resolution degradation. Chemical concentration, spray pressure, dwell time, and solution temperature are all variables affecting the developing process.
Condition of the photoresist
The storage of the resist material is also important. Resist stored at higher temperatures and humidity can degrade the material. Dry film resist comes wrapped in a light blocking material. Exposure to ambient light for a long period of time can degrade the resist.
Facility Environment
Temperature and humidity levels of the fabrication facility affect the photoimaging process, so the environment of the room is closely monitored and controlled. Most fabrication sites perform the steps directly related to imaging within a clean room with restricted access. Special non-shedding garments are worn within these controlled environments.
Next time, in Part 3: laser direct imaging (LDI).
Dave Becker is vice president of sales and marketing at All Flex Flexible Circuits LLC.
More Columns from All About Flex
All About Flex: Terms and ConditionsAll About Flex: ISO 9001 Basics
All About Flex: FAQs on UL Listings for Flexible Circuits
All About Flex: Avoiding Trace Fracturing in a Flexible Circuit
Polyimide vs. Silicone for Flexible Heaters
All About Flex: Copper Thickness Requirements for Flex Circuits
All About Flex: Copper Grain Direction
All About Flex: Options for Purchasing Flexible Heaters