-
- News
- Books
Featured Books
- smt007 Magazine
Latest Issues
Current IssueWhat's Your Sweet Spot?
Are you in a niche that’s growing or shrinking? Is it time to reassess and refocus? We spotlight companies thriving by redefining or reinforcing their niche. What are their insights?
Moving Forward With Confidence
In this issue, we focus on sales and quoting, workforce training, new IPC leadership in the U.S. and Canada, the effects of tariffs, CFX standards, and much more—all designed to provide perspective as you move through the cloud bank of today's shifting economic market.
Intelligent Test and Inspection
Are you ready to explore the cutting-edge advancements shaping the electronics manufacturing industry? The May 2025 issue of SMT007 Magazine is packed with insights, innovations, and expert perspectives that you won’t want to miss.
- Articles
- Columns
- Links
- Media kit
||| MENU - smt007 Magazine
Solder Paste Printing: A User’s Perspective
June 22, 2016 | Stephen Las Marias, I-Connect007Estimated reading time: 3 minutes
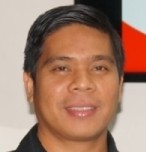
I recently sat down with Integrated Micro-Electronics' Joemar Apolinario, engineering manager; Aurelio Bantigue, DFM engineer; and Rodney Bebe, process engineer, to get their insights on the solder paste printing process. They discussed the challenges and key considerations to make when dealing with tighter tolerances and finer pitches in line with the continuing miniaturization trend in the electronics manufacturing industry. They also talked about the impact of solder pastes in the printing process, and the criteria for their selection and qualification. Finally, they highlighted design and process strategies to get the best solder paste printing results.
Stephen Las Marias: Please discuss the solder paste printing process and the challenges you face.
Joemar Apolinario: The solder paste printing process is the most challenging process in the SMT operation because majority of the defects—around 60 to 80%—are coming from this process. These include non-wetting, insufficient volume, and short (solder bridging). Factors that greatly impact the solder paste printing quality may vary from the stencil design, the solder paste type, the machine capability (parameters), setup and tooling, and even the engineering skills of those who handle this process.
The challenge is that the devices now are getting smaller and smaller. We also have the complex products—those boards that combine critical components such as BGAs and ICs, which require finer pitches and smallest diameters—and non-critical components. The third challenge is the reliability. We have products that require higher reliability—and those are very sensitive to solder cracks or voiding defects. For most of the defects that we have encountered, the solder volume being deposited to the pad does not meet the requirement.
Joemar Apolinario, Aurelio Bantigue, and Rodney Bebe, IMI
Las Marias: How do you address those challenges?
Aurelio Bantigue: From a DFM standpoint, what we have done so far is we review the stencil design or the aperture design for each of the components. In our view, we consider both the PCB design and the components that will be mounted to the board. We recognize that the trend is toward smaller components, and the challenge is the appropriate aperture design for smaller pins and pads. What we can do is consider the appropriate solder volume. But the more challenging issue is the complexity—you are mixing small components, and larger components that require more solder paste, in a board. So, it will be more difficult. There are several design considerations that we do. We can do electroform step stencils, or sometimes, we have to overprint the solder paste—you have the solder paste outside the pad, you will have enough volume for those larger components. We can deposit small volume for the small components and enough volume for the larger components.
Las Marias: How does the solder paste impact the printing process?
Apolinario: The solder paste has a big impact on printing as it is the main ingredient of the process and it has a direct impact on reliability. The choice of the right type and composition of solder paste may help achieve good printing quality. But, the key here is having the right parameter to use, for instance, the design of the pad and the stencil. We need to select the appropriate type of solder to match the stencil design and pad design to have a good printing result. Another factor is the machine. We need to use the appropriate machine to get good results.
We have different types of solder printing machines—we have the screen printing as our typical printing method; we are now also using jet printing process. So, that’s the factor. Apart from the multi-step stencil design to accommodate those complex PCBAs, we are now trying electroform nano-coated stencil. This is something new in our process—nano-coating by immersion coating process. The design of the stencil is electroformed, then it goes through a nano-coating process. This process makes the stencil smoother and non-sticky, to have a good transfer efficiency and to reduce cleaning sequence in the process.
Editor's Note: This article originally appeared in the June 2016 issue of SMT Magazine.
Suggested Items
IMI Wins Gold Award for Best Managed Technology Company at FinanceAsia’s 29th Asia’s Best Companies Awards
07/01/2025 | IMIIntegrated Micro-Electronics Inc. (IMI) has been awarded the prestigious Gold Award for Best Managed Technology Company at the 29th edition of the Asia’s Best Companies Awards, hosted by FinanceAsia.
IMI Signs Share Purchase Agreement to Sell Its Czech Republic Manufacturing Site
06/06/2025 | IMIIntegrated Micro-Electronics Inc (IMI), through its wholly-owned subsidiary, Coöperatief IMI Europe U.A., has signed a share purchase agreement to sell 100% of the shares in IMI Czech Republic (IMI CZ) to KEBODA Deutschland GmbH & Co. KG, a subsidiary of Keboda Technology Co., Ltd. (Keboda), a publicly listed company in China.
Moving Forward With Confidence: SMT007 Magazine June 2025
06/02/2025 | I-Connect007 Editorial TeamAre you as prepared to close a sale as you could be? IPC’s monthly EMS reports showed that EMS revenue increased in March and April. With a book-to-bill ratio of 1.41, things are moving fast. That said, EMS shipments in April were down 1.4%, and bookings in April decreased by 10% year over year. In the June 2025 issue of SMT007 Magazine, we discuss best practices to keep your business thriving.
Trouble in Your Tank: Yield Improvement and Reliability
05/22/2025 | Michael Carano -- Column: Trouble in Your TankThere’s a simple rule of business in manufacturing: “It is all about yields.” Higher yields for your products allow for increased profits and satisfied customers. When there are lower yields, overall cost to manufacture increases, and the additional time and strain on the factory floor affect the entire operation. Lower yields are often the result of “process drift,” when critical process parameters and specialized plating additives fall outside their acceptable ranges.
Siemens to Bring Advanced Timing Constraint Capabilities to EDA Design Flow with Excellicon Acquisition
05/19/2025 | SiemensSiemens has entered into an agreement to acquire Excellicon to bring its best-in-class software for the development, verification, and management of timing constraints to Siemens’ EDA portfolio of software for IC design