-
- News
- Books
Featured Books
- smt007 Magazine
Latest Issues
Current IssueIntelligent Test and Inspection
Are you ready to explore the cutting-edge advancements shaping the electronics manufacturing industry? The May 2025 issue of SMT007 Magazine is packed with insights, innovations, and expert perspectives that you won’t want to miss.
Do You Have X-ray Vision?
Has X-ray’s time finally come in electronics manufacturing? Join us in this issue of SMT007 Magazine, where we answer this question and others to bring more efficiency to your bottom line.
IPC APEX EXPO 2025: A Preview
It’s that time again. If you’re going to Anaheim for IPC APEX EXPO 2025, we’ll see you there. In the meantime, consider this issue of SMT007 Magazine to be your golden ticket to planning the show.
- Articles
- Columns
Search Console
- Links
- Media kit
||| MENU - smt007 Magazine
To Clean or No Clean?
June 23, 2016 | Barry Matties, I-Connect007Estimated reading time: 19 minutes
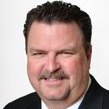
The addition of a cleaning process to your manufacturing line will amount to an added 5–6 cents per board produced. Mike Konrad of Aqueous Technologies believes that is a small price to pay for the added value, testing, and reduced liability and insurance that a cleaning solution can provide; however, he is the first to admit cleaning isn’t for everyone. I sat down with Mike to determine which potential customers could benefit most from cleaning and to discuss the recent change in tolerance, ECM, and the need for updated standards.
Barry Matties: Mike, why don't you begin by talking a little bit about Aqueous and what it does?
Mike Konrad: Aqueous is a manufacturer of cleaning equipment. A lot of people call our machines "de-fluxing" machines. We like to refer to them as cleaning machines because we remove more than flux. We have fully automated cleaning systems designed for post re-flow circuit assemblies. And we have ionic contamination testers, ROSE testers (resistivity of solvent extract). They are designed to test to see how clean boards are after they've been cleaned. It is an IPC and military requirement. Then we also have cleaning systems for stencils and misprinted assemblies. We clean up some mistakes and we clean up the tools that are used in the assembly process.
Matties: What are the most common problems that you see in the industry around cleaning?
Konrad: Pretty much the entire industry used to clean their assemblies after soldering or reflow. Up until the mid- to late-90s. Then, due to environmental regulations, specifically the Montreal Protocol, the solvents that were used to clean circuit assemblies were eliminated and no good drop-in-replacement solvent really took its place. That void fueled a new technology called "no clean" flux and a whole new species of flux and solder pastes evolved that were designed not to be cleaned and they were labeled, quite inappropriately, "no clean." More appropriately, they should be named "low residue.”
Shortly after the introduction of no cleans, many companies, given the choice of adapting a new solder paste or flux vs. going to a new cleaning process, chose the former and stopped cleaning altogether. The problem that we have today is the results of yesterday were actually quite successful. They left a little bit of residue on the board and everything worked well. What we're seeing today, due to a number of reasons that have been widely reported on, like miniaturization and the switch from leaded base alloys to lead-free alloys, combined with a higher reliance on quality standards, is an attitude to not just fix the symptom, but rather determine the cause and fix the problem.
ISO, TQM, Six-Sigma, and all of those quality acronyms really are forcing people to look at what the causes of problems are—and more and more assemblers are realizing the problem today is the amount of residue on the assembly may be no more than yesterday, but today it's just less tolerable. There's not a light that turns on when things become intolerable. It happens slowly and they see their quality yields drop. Manufacturers see more products being returned. In some cases they see more civil litigation because products are failing in the field and then they find out that if they spent 5 cents cleaning the product they would have saved millions of dollars in litigation. Those are the issues we're seeing today.
A lot of people are coming to us knowing they have a problem, but not knowing why they have a problem. They compare the results of five or 10 years ago and demand an answer to “Why isn't that still working today?”
Matties: Isn't the obvious answer or reason tighter tolerances, finer features?
Konrad: That's basically it, tighter tolerances and more harsh manufacturing environments, like with higher re-flow temperatures for example. So really the amount of residue tolerable to an assembly today is much less than it was just a few years ago. What manufacturers frequently fail to realize is when they stopped cleaning flux, they stopped cleaning everything. That's why we don't really like calling it a "de-fluxing" process because that definition is really too narrow. It's really a cleaning process. Even though the flux companies are accurate when they say, "We leave so little residue, it really is practically harmless." It may be true, and at face value let's assume it is true.
When boards were being cleaned as part of the normal assembly process, pre-1990s, not only were we removing flux, which back then was harmful if left on, we were removing etch residues, developer chemicals, silicone mold releases, fingerprints, HASL fluids, Dorito potato chip residues, and flux. While the flux may be less harmful, we were not cleaning anything else. The stowaways, board fab, component fab, and assembly residues, are allowed to be present on the board. When we have the stowaways, we then put flux on it which at best case is just a little bit of residue. The totality of all of those residues is creating a problem whereby the footprint between cathodes and anodes on an assembly is much smaller and the gap between components is much smaller than ever before. That produces kind of a perfect storm for electro-chemical migration.
Electro-chemical migration or ECM takes two popular and one less popular form. The two popular forms are dendritic growth, which is where dendritic growth occurs on a board and it catches fire or it shorts or otherwise fails, and it's quite dramatic. Less dramatic is electrical leakage, AKA parasitic leakage. That problem occurs only when certain conditions are present. When one of the conditions is removed it goes away for a while and then it comes back.
Then there's CAF, conductive anodic filament based failures, which is an ECM issue, but it's between the board layers and that can't be solved by cleaning externally. It can be solved by other things, mainly baking. ECM is presenting itself more frequently than it did before and many assemblers are in denial because they are going by the experience of a few years ago where everything was cool. Now all of a sudden things aren't cool anymore they don't know what changed. That's basically the amount of residue an assembly can tolerate.
Page 1 of 4
Suggested Items
Aqueous Technologies to Hold SMT Wars Live Webinar on August 7
07/31/2018 | Aqueous TechnologiesOn August 7, 2018, Aqueous Technologies' Tech-Tuesday 2018 Webinars continue with "SMT-WARS - Lessons Learned from a Contract Manufacturer and Their Customer Who Sued Them."
ZESTRON Academy to Host Soldering, Cleaning and Coating Workshop
03/30/2018 | ZESTRONZESTRON will present at the Soldering, Cleaning and Coating Workshop with Arbell, Alpha Assembly Solutions, Aqueous Technologies, and MG Chemicals. This free, collaborative workshop will be held on Tuesday, April 17, 2018 in Vancouver, Canada.
Aqueous Technologies Webinar Tackles Cleanliness Quantification Techniques
03/12/2018 | Aqueous TechnologiesAqueous Technologies will be holding a webinar titled “Cleanliness Quantification Techniques... How Clean is Clean Enough?” on March 20, 2018.
Webinar on Cleaning Circuit Assemblies
12/26/2017 | Aqueous TechnologiesAqueous Technologies will kick off its 2018 Tech Tuesday Webinar series with “A Beginner’s Guide to Cleaning Circuit Assemblies.”
Team of Industry Experts to Present Cleaning/Materials/X-ray Workshop
03/23/2016 | Reliability WorkshopCircuit Technology, KIC, KYZEN, Nordson DAGE, Aqueous Technologies and AIM Solder are working together to present the “Reliability Workshop: Cleaning – Materials – X-ray” in Raleigh, NC on Tuesday, April 12 and Asheville, NC on Thursday, April 14. Both workshops will take place from 8 a.m.-4:30 p.m.