All About Flex: Taguchi Design of Experiments and Flexible Circuits
July 14, 2016 | Dave Becker, All FlexEstimated reading time: 4 minutes
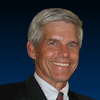
Reducing variability in a process, or a sequence of processes, can require a significant and structured amount of work and analysis. One must develop an understanding of critical variables and determine methods to control them. Statistically based experiments are often needed for proper analysis.
Classical Design of Experiments
One strategy is to use classical design of experiments (DOE).
With DOE, the technical team needs to first identify variables that are suspected to have a significant impact on the output. With best estimates of critical variables, the methodology then defines a high point and low of each identified variable. Variables don’t necessarily fall into “high” and “low” categories. They may include options like bake or no bake, alternative surface finishes, material types, etc. A series of experimental runs are designed that have variables run at the high point and a low point in combination with all the other variables low and high. The output of the experiment (i.e., the consequence of the variety of inputs), is best if it can be defined numerically.
The table below illustrates a simple two variable experimental design.
The design above is called full factorial because every combination of high and low variables is run. Of course with two variables, only four experimental runs are required to test every combination of high and low. For three variables, eight or 23 runs are required. A four-variable experiment would require 16 unique runs.
A key requirement for proper experimental design is to randomize the experimental order. This avoids results being contaminated by other conditions that were not controlled during the experiment. Randomizing the order of runs reduces the risk of built in experimental bias confounding the results.
A full factorial experiment provides the main effects of each variable plus all the interaction effects.
Designed experiments are valuable, but disruptive for three primary reasons:
- They should be performed on production equipment
- Proper examination of variables may involve a large number of experiments; if six variables are to be examined, a full factorial experiment would require 64 different runs
- Randomization adds set-up times and cost in a highly capitalized production environment
A more realistic type of DOE is called fractional factorial. Fractional factorial experiments are designed to only find out the main effects and major interactions; as such, they require fewer runs. Many good reference documents are available to assist with DOE layout, statistical interpretation, and factorial design.
Taguchi Design of Experiments
Taguchi design of experiments is a variation of fractional factorial experiments, but with a one major difference. It addresses the fact that it is not realistic to control every single variable that might affect the process. Outside temperature, humidity, time of day, raw material supplier and operator are just a few examples of variables that are either impossible or highly impractical to control. If the experiments are being done in production, they may need to be spread out over several weeks so production schedules can be accommodated. Randomizing the experiment in a full scale production environment is often prohibitively expensive.
The Taguchi method allows for the reality faced when conducting designed experiments in production: it is often not practical to properly randomize an experiment. So in addition to all the critical variables tested, another variable, noise, is allowed and defined. The noise contains all the variables that are not controlled. The high level might be the noise variables set at one realistic extreme and the low level might be all the noise variables set the other realistic extreme. One of the goals of the experiment is to determine what variables and variable settings yield the most robust results. These are settings where there is zero interaction effect with the noise variable.
Page 1 of 2
Testimonial
"We’re proud to call I-Connect007 a trusted partner. Their innovative approach and industry insight made our podcast collaboration a success by connecting us with the right audience and delivering real results."
Julia McCaffrey - NCAB GroupSuggested Items
How Good Design Enables Sustainable PCBs
08/21/2025 | Gerry Partida, Summit InterconnectSustainability has become a key focus for PCB companies seeking to reduce waste, conserve energy, and optimize resources. While many discussions on sustainability center around materials or energy-efficient processes, PCB design is an often overlooked factor that lies at the heart of manufacturing. Good design practices, especially those based on established IPC standards, play a central role in enabling sustainable PCB production. By ensuring designs are manufacturable and reliable, engineers can significantly reduce the environmental impact of their products.
50% Copper Tariffs, 100% Chip Uncertainty, and a Truce
08/19/2025 | Andy Shaughnessy, I-Connect007If you’re like me, tariffs were not on your radar screen until a few months ago, but now political rhetoric has turned to presidential action. Tariffs are front-page news with major developments coming directly from the Oval Office. These are not typical times. President Donald Trump campaigned on tariff reform, and he’s now busy revamping America’s tariff policy.
Global PCB Connections: Understanding the General Fabrication Process—A Designer’s Hidden Advantage
08/14/2025 | Markus Voeltz -- Column: Global PCB ConnectionsDesigners don’t need to become fabricators, but understanding the basics of PCB fabrication can save you time, money, and frustration. The more you understand what’s happening on the shop floor, the better you’ll be able to prevent downstream issues. As you move into more advanced designs like HDI, flex circuits, stacked vias, and embedded components, this foundational knowledge becomes even more critical. Remember: the fabricator is your partner.
MKS’ Atotech to Participate in IPCA Electronics Expo 2025
08/11/2025 | AtotechMKS Inc., a global provider of enabling technologies that transform our world, announced that its strategic brands ESI® (laser systems) and Atotech® (process chemicals, equipment, software, and services) will showcase their latest range of leading manufacturing solutions for printed circuit board (PCB) and package substrate manufacturing at the upcoming 17th IPCA Show to be held at Pragati Maidan, New Delhi from August 21-23, 2025.
MKS Showcases Next-generation PCB Manufacturing Solutions at the Thailand Electronics Circuit Asia 2025
08/06/2025 | MKS Instruments, Inc.MKS Inc, a global provider of enabling technologies that transform our world, today announced its participation in Thailand Electronics Circuit Asia 2025 (THECA 2025), taking place August 20–22 at BITEC in Bangkok.