Made in Brazil: The Evolution and Revolution of Impedance Control in PCB Production
July 21, 2016 | Renato Peres, Circuibras Circuitos Impressos ProfissionaisEstimated reading time: 1 minute
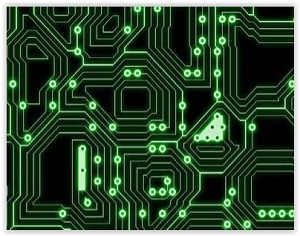
The PCB industry in Brazil has gone through several changes over the last decade. Our customers have been demanding better quality and higher-reliability products more than ever before, but few things have changed as much as impedance control. PCBs with impedance control requirements have become the engine of the market, and finding solutions to fit the customer’s needs is extremely challenging.
Ten years ago, the Brazilian PCB industry was a little vague on this subject, and very few PCB shops were doing impedance testing. About five years ago, with the evolution of the national PCB industry, customers started producing prototypes requiring impedance control and the market started to develop. However, it seemed to me that neither the customers nor the PCB shops really knew what to order and to deliver at that time.
There always were differences between the specs for the board, the coupon measured, and the simulation software. As a best practice, many PCB shops used to appeal to a cross-section analysis to verify the PCB build up. In the end, impedance simulation software was more reliable than the TDR measurements.
I remember I felt a bit normal last year when I read the article written by Dan Beaulieu and Bob Tarzwell for The PCB Design Magazine, "Controlled Impedance: A Real-World Look at the PCB Side." Coupons that don’t fit the specs of the customers, cross-section analyses, differences in resin flow during lamination, copper thickness variation, and many other issues described in the article were very similar to the problems we faced daily.
Nevertheless, the industry in Brazil has gone further, pressing the suppliers to develop new controls, not yet usual to the national market.
To read this entire article, which appeared in the July 2016 issue of The PCB Magazine, click here.
Testimonial
"The I-Connect007 team is outstanding—kind, responsive, and a true marketing partner. Their design team created fresh, eye-catching ads, and their editorial support polished our content to let our brand shine. Thank you all! "
Sweeney Ng - CEE PCBSuggested Items
How Good Design Enables Sustainable PCBs
08/21/2025 | Gerry Partida, Summit InterconnectSustainability has become a key focus for PCB companies seeking to reduce waste, conserve energy, and optimize resources. While many discussions on sustainability center around materials or energy-efficient processes, PCB design is an often overlooked factor that lies at the heart of manufacturing. Good design practices, especially those based on established IPC standards, play a central role in enabling sustainable PCB production. By ensuring designs are manufacturable and reliable, engineers can significantly reduce the environmental impact of their products.
50% Copper Tariffs, 100% Chip Uncertainty, and a Truce
08/19/2025 | Andy Shaughnessy, I-Connect007If you’re like me, tariffs were not on your radar screen until a few months ago, but now political rhetoric has turned to presidential action. Tariffs are front-page news with major developments coming directly from the Oval Office. These are not typical times. President Donald Trump campaigned on tariff reform, and he’s now busy revamping America’s tariff policy.
Global PCB Connections: Understanding the General Fabrication Process—A Designer’s Hidden Advantage
08/14/2025 | Markus Voeltz -- Column: Global PCB ConnectionsDesigners don’t need to become fabricators, but understanding the basics of PCB fabrication can save you time, money, and frustration. The more you understand what’s happening on the shop floor, the better you’ll be able to prevent downstream issues. As you move into more advanced designs like HDI, flex circuits, stacked vias, and embedded components, this foundational knowledge becomes even more critical. Remember: the fabricator is your partner.
MKS’ Atotech to Participate in IPCA Electronics Expo 2025
08/11/2025 | AtotechMKS Inc., a global provider of enabling technologies that transform our world, announced that its strategic brands ESI® (laser systems) and Atotech® (process chemicals, equipment, software, and services) will showcase their latest range of leading manufacturing solutions for printed circuit board (PCB) and package substrate manufacturing at the upcoming 17th IPCA Show to be held at Pragati Maidan, New Delhi from August 21-23, 2025.
MKS Showcases Next-generation PCB Manufacturing Solutions at the Thailand Electronics Circuit Asia 2025
08/06/2025 | MKS Instruments, Inc.MKS Inc, a global provider of enabling technologies that transform our world, today announced its participation in Thailand Electronics Circuit Asia 2025 (THECA 2025), taking place August 20–22 at BITEC in Bangkok.