-
- News
- Books
Featured Books
- smt007 Magazine
Latest Issues
Current IssueIntelligent Test and Inspection
Are you ready to explore the cutting-edge advancements shaping the electronics manufacturing industry? The May 2025 issue of SMT007 Magazine is packed with insights, innovations, and expert perspectives that you won’t want to miss.
Do You Have X-ray Vision?
Has X-ray’s time finally come in electronics manufacturing? Join us in this issue of SMT007 Magazine, where we answer this question and others to bring more efficiency to your bottom line.
IPC APEX EXPO 2025: A Preview
It’s that time again. If you’re going to Anaheim for IPC APEX EXPO 2025, we’ll see you there. In the meantime, consider this issue of SMT007 Magazine to be your golden ticket to planning the show.
- Articles
- Columns
Search Console
- Links
- Media kit
||| MENU - smt007 Magazine
Industry 4.0: Making the First Move
July 26, 2016 | Michael Ford, Mentor GraphicsEstimated reading time: 4 minutes
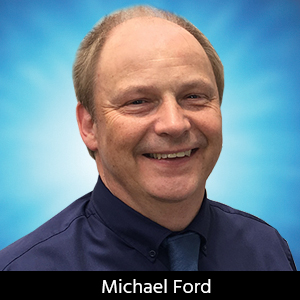
After two or three years of hearing about Industry 4.0, many companies now have active Industry 4.0, Internet of Manufacturing (IoM), or smart factory projects. In each case, different approaches were taken that appeared to best fit the project requirements and that would deliver the intended benefits versus the cost and effort investment needed. Like a game of chess, the first move can be the most important. Let’s take a look at the most common approaches adopted so far, and check in to see how things are going, what can be learned from the experiences, and how things could be done better.
The earliest adopters of any new idea are often motivated by more than simply a provable return on investment. The search is on for the proof of concept, to show industry leadership, and to move toward a technology that in the future should bring future competitiveness. The company size, allocation of IT resources, the systems and machines currently in use, whether OEM or EMS, and the sector in which the company is doing business determine the approach to be taken. These approaches can be more or less summarized into the following categories:
- In-house development
- Application of an existing generic standard
- The machine vendor environment
- Middleware
- An established MES solution
- The application of OML (Open Manufacturing Language).
However, there is no best solution. Each of these are valid solutions in certain conditions, and we have to remember that each represents a pioneering attitude that only the most progressive of companies have been able to consider. Looking at what might be the average experience today within each of these categories of solutions has flagged some interesting issues and potential solutions.
In-House Development
The headline stories for smart factory internal development projects come from Foxconn and Flex, who each presented their achievement of a model smart factory at the recent IoM event in San Jose and at the IPC APEX EXPO in Las Vegas, respectively. The largest EMS companies in the world are among the first adopters to attract new business and reduce operational costs. In both presentations, their results were compelling. The achievement of linking equipment their internal systems and the use of the resultant information seems perfectly in line with their expectations. Even for companies of this magnitude, one of the key challenges was acquiring data from all of the different processes on the shop-floor. Having considerable purchasing power at their disposal, they were able to work with machine vendors to mutually work out the communication on a specifically agreed basis, which appeared to be unique for each vendor
Significant development resource is needed in this instance, which perhaps is acceptable for companies of this size. But what about the reliability and the degree of on-going maintenance, as older machines are phased out and newer automation introduced? The IT resources have to be maintained indefinitely, as do the close tie-ins to the machine vendors who cooperate. This is perhaps the most expensive way to achieve shop-floor communication, through “brute force,” with the underlying expectation that costs will reduce as communication capabilities and standards improve.
Both Flex and Foxconn are to be commended in their achievement, which to the rest of the industry may seem like a fairy tale, but is in fact real, with real associated benefits. What is less clear so far is how these benefits compare to the initial and continued investment of the projects.
Application of an Existing Generic Standard
Standards such as CAM-X and SECS-GEM were introduced about 15 or 20 years ago, a time when SMT operations were a lot simpler and more rigid than they are today. In particular, the IPC-sponsored CAM-X was the first real standard that featured an infrastructure, a protocol and, to some extent, a definition of standard machine events. The attraction of CAMX to some companies was enough of a trigger to start them looking at the standardization of shop-floor communication. All seemed to go well for a short time, until CAM-X had some critical weaknesses in the network bandwidth required to support a wasteful infrastructure and protocol and in the ability to support anything beyond the simplest of commonly defined event attributes.
Rather than continue to work to refine the standard, the IPC seemed to let it go as commercial entities sprung up, offering hardware and software solutions based on CAM-X and customizations, which meant that CAM-X was no longer the standard it was meant to be. Instead of every process getting connected as standard, significant amounts of customization were needed on top of the purchase of what were becoming proprietary solutions. This situation seems to have “poisoned” the market away from believing that a real, complete, and open standard could ever exist.
If the IPC could not do it, then who could? Key companies who invested heavily in these broken standards now find themselves with momentum but going nowhere. Once again, commercial entities have come in to take advantage of the situation, offering upgrades to better and more modern protocols, such as XMPP, which although superior in many ways, is seen to be somewhat unreliable in their definition, already with a multitude of variations. The result is an endless pattern of returning to square one; as new equipment comes in, communication capability needs development, with endless maintenance, a real and substantial revenue stream for the commercial providers of solutions based on older standards.
However, the choice to implement the standard is still smart, with benefits achieved before the Internet of Manufacturing was ever conceived. These companies are the true pioneers of the industry, and are the ones likely to get arrows in their backs as history shows. Respect is due to the many people and companies who made it happen; but they must now be thinking that they are like aircraft, endlessly circling the airport, unable to find a way to land.
To read this entire article, which appeared in the July 2016 issue of SMT Magazine, click here.
Suggested Items
LITEON Technology Reports Consolidated April Sales of NT$13.4 Billion Up 27% YoY
05/09/2025 | LITEON TechnologyLITEON Technology reported its April consolidated revenue of NT$13.4 billion. Thanks to the growth from power management in cloud computing, advanced server, and networking, the revenue is up 27% YoY.
PTCRB Certification Adds New IoT Chipset Certification Category, Certifies Sony's Altair ALT1350 CTIA Certification
04/23/2025 | PRNewswireCTIA Certification announced the first PTCRB certified IoT chipset, Sony's Altair ALT1350.
UHDI Fundamentals: UHDI Drives Unique IoT Innovation in Farming
04/22/2025 | Anaya Vardya, American Standard CircuitsThe combination of UHDI's high-bandwidth capabilities and IoT's real-time data processing can lead to more efficient, immersive, and smarter IoT systems. This convergence of two revolutionary technologies is enabling quantum advancements in some very “unconventional” applications. The typical discussions around UHDI focus on our standard electronics industry market segments like milaero, medical, consumer electronics, etc. IoT is all about machines talking to other machines, machine learning, and artificial intelligence, but again, typically applied in our PCB and assembly operations.
Mouser Electronics Named Best New Product Promoter for 2024 by Diotec Semiconductor
04/18/2025 | BUSINESS WIREMouser Electronics, Inc., the authorized global distributor with the newest electronic components and industrial automation products, proudly announces that it has been named the Best New Product Promoter for 2024 by Diotec Semiconductor, a leading manufacturer of diodes, transistors,
UK, Cyprus Strengthen Space Ties
04/14/2025 | ESAThe first Cyprus-UK Bilateral Cooperation Event brought together representatives from the space sectors and governments of both countries, with the support of the European Space Agency (ESA).