-
- News
- Books
Featured Books
- smt007 Magazine
Latest Issues
Current IssueMoving Forward With Confidence
In this issue, we focus on sales and quoting, workforce training, new IPC leadership in the U.S. and Canada, the effects of tariffs, CFX standards, and much more—all designed to provide perspective as you move through the cloud bank of today's shifting economic market.
Intelligent Test and Inspection
Are you ready to explore the cutting-edge advancements shaping the electronics manufacturing industry? The May 2025 issue of SMT007 Magazine is packed with insights, innovations, and expert perspectives that you won’t want to miss.
Do You Have X-ray Vision?
Has X-ray’s time finally come in electronics manufacturing? Join us in this issue of SMT007 Magazine, where we answer this question and others to bring more efficiency to your bottom line.
- Articles
- Columns
Search Console
- Links
- Media kit
||| MENU - smt007 Magazine
How to Create the Perfect SMT Reflow Oven Profile
December 22, 2016 | Richard Barratt, JJS ManufacturingEstimated reading time: 5 minutes
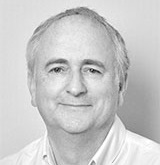
Although some original equipment manufacturers (OEMs) view printed circuit board assemblies (PCBAs) as commodity items, consistently producing them in volume takes time to perfect. While electronics manufacturing services (EMS) providers will have their own preference when it comes to machine type and brand, broadly speaking, the process steps they go through to produce PCBAs are the same.
However, in our opinion, one step that can make all of the difference when it comes to quality and consistency is reflow. If you fail to profile the oven correctly, then all of the hard work and effort that has gone into loading feeders, programming the machines, optimizing the build and then running the production line will be wasted.
So how do EMS companies go about creating the perfect surface mount (SMT) reflow oven profile? Let's find out.
Working on the Baseline
The NPI engineer will usually start the process by selecting an oven profile they have used before and have stored on their system. Some EMS providers will have taken time to develop a range of "baseline" profiles, which can then be selected depending on the PCBA they are working on. Time taken to perfect the baseline profile will pay dividends as most assemblies will then fall within one of these.
Baseline profiles may include:
- One dedicated to densely populated assemblies with elevated temperatures
- One dedicated to "standard" assemblies
- One dedicated to assemblies that contain sensitive parts and require lower temperatures
Using their skill, judgement and experience, the NPI engineer will select the profile and temperature settings they believe suits the new assembly the best.
Requesting a Sample PCBA
Ideally, the OEM will have provided their assembly partner with a populated PCBA. If one isn't provided the NPI engineer may request one so it can be used during the set-up process. The NPI engineer will attach thermocouples to multiple locations across the sample board. These should be attached to a range of components with varying degrees of heat dissipation – i.e. a transformer, ball grid array (BGA) and passive devices.
Dependent on the size of the PCBA, it is recommended that between three and six thermocouples are attached and it's critical they are connected properly. Quite often EMS providers will tape these in place but, unfortunately, there is a risk they lift during the process, which results in the air temperature being measured rather than board and lead temperature.
For a secure connection, we recommend applying:
- High temperature solder to secure the thermocouple to the component lead
- An adhesive, such as Chipbonder, ensuring residual glue is not found between mating surfaces
Special attention should be given to BGAs. For the best results, a thermocouple should be placed underneath the device making direct contact with the terminations. This can be achieved by drilling a small hole through the underside of the board but is a destructive process - hence the requirement for a sample PCBA from the outset.
The PCBA will then be run through the reflow oven with thermocouples attached to a data logger. It's important that that the data logger is positioned correctly so that it doesn't affect the movement of the PCBA through the oven. Once the PCBA has passed through the oven, the results from the data logger will be downloaded into the chosen oven profiling software and this is where the first real analysis of the profile begins.
It's All in the Detail
Each solder paste manufacturer will recommend a baseline profile with + and - tolerances. Where possible, the EMS provider will try and achieve a result in the middle of these tolerance bands. However, certain component requirements will require the EMS provider works at the upper or lower limits of these tolerances.
The NPI engineer will pay close attention to the following three areas and below recommendations assume a typical lead-free alloy with a melting point of 217 degrees Celsius (°C) is used:
- Ramp – this is the rate of temperature increase measured in °C per second and should be between 1-3°C per second. This will be more noticeable at the beginning of the profile where the board temperature changes from ambient to 120°C. Failing to comply with this could lead to component damage and this is one area component manufacturers typically specify.
- Soak – normally occupies 33-50 per cent of the total heated tunnel length and exposes the PCB to a relatively steady temperature that will allow the components of different mass to be uniform in temperature. The soak zone also allows the flux to concentrate and the volatiles to escape from the paste.
- Reflow – this is the area where the temperature is elevated to between 230 and 250°C. A critical measure is the time above reflow, which typically lasts between 45 and 90 seconds. It's important to check component specifications for maximum temperature.
Fine-Tuning the Profile
Depending on the data logger output, the NPI engineer may decide to "fine tune" the profile further. Using the oven profiling software, the NPI engineer has the ability to amend certain oven parameters (speed/temperature) through the oven profiling software and then view the "predicted" results. In our experience, we have found the prediction tool to be highly accurate - however, it does rely on ensuring the oven is accurately represented within the software. To do this, the software will need to understand the oven make and model, number of zones and length of each zone.
Providing the NPI engineer is happy with the predicted results, they will then make physical changes to the oven parameters and store the profile under a unique reference number, which typically consists of the item code, revision level and whether the profile is for the top or bottom side of the PCBA.
And there you have it: a quick overview of how an EMS provider sets about creating the perfect oven profile, which ensures your products are built consistently to a high standard. Of course, this process does assume that the ovens they use are set up correctly in the first place and regularly monitored. If they're not, all of the above will have been a waste of time!
The post originally appeared on the JJS Manufacturing blog which can be found here.
Suggested Items
Preventing Surface Prep Defects and Ensuring Reliability
06/10/2025 | Marcy LaRont, PCB007 MagazineIn printed circuit board (PCB) fabrication, surface preparation is a critical process that ensures strong adhesion, reliable plating, and long-term product performance. Without proper surface treatment, manufacturers may encounter defects such as delamination, poor solder mask adhesion, and plating failures. This article examines key surface preparation techniques, common defects resulting from improper processes, and real-world case studies that illustrate best practices.
Breaking Silos with Intelligence: Connectivity of Component-level Data Across the SMT Line
06/09/2025 | Dr. Eyal Weiss, CybordAs the complexity and demands of electronics manufacturing continue to rise, the smart factory is no longer a distant vision; it has become a necessity. While machine connectivity and line-level data integration have gained traction in recent years, one of the most overlooked opportunities lies in the component itself. Specifically, in the data captured just milliseconds before a component is placed onto the PCB, which often goes unexamined and is permanently lost once reflow begins.
BEST Inc. Introduces StikNPeel Rework Stencil for Fast, Simple and Reliable Solder Paste Printing
06/02/2025 | BEST Inc.BEST Inc., a leader in electronic component rework services, training, and products is pleased to introduce StikNPeel™ rework stencils. This innovative product is designed for printing solder paste for placement of gull wing devices such as quad flat packs (QFPs) or bottom terminated components.
See TopLine’s Next Gen Braided Solder Column Technology at SPACE TECH EXPO 2025
05/28/2025 | TopLineAerospace and Defense applications in demanding environments have a solution now in TopLine’s Braided Solder Columns, which can withstand the rigors of deep space cold and cryogenic environments.
INEMI Interim Report: Interconnection Modeling and Simulation Results for Low-Temp Materials in First-Level Interconnect
05/30/2025 | iNEMIOne of the greatest challenges of integrating different types of silicon, memory, and other extended processing units (XPUs) in a single package is in attaching these various types of chips in a reliable way.