-
- News
- Books
Featured Books
- smt007 Magazine
Latest Issues
Current IssueWhat's Your Sweet Spot?
Are you in a niche that’s growing or shrinking? Is it time to reassess and refocus? We spotlight companies thriving by redefining or reinforcing their niche. What are their insights?
Moving Forward With Confidence
In this issue, we focus on sales and quoting, workforce training, new IPC leadership in the U.S. and Canada, the effects of tariffs, CFX standards, and much more—all designed to provide perspective as you move through the cloud bank of today's shifting economic market.
Intelligent Test and Inspection
Are you ready to explore the cutting-edge advancements shaping the electronics manufacturing industry? The May 2025 issue of SMT007 Magazine is packed with insights, innovations, and expert perspectives that you won’t want to miss.
- Articles
- Columns
- Links
- Media kit
||| MENU - smt007 Magazine
Evaluation of the Use of ENEPIG in Small Solder Joints
January 19, 2017 | Ben Gumpert, William Fox, and C. Don Dupriest, Lockheed MartinEstimated reading time: 6 minutes
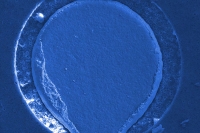
Abstract
The surface finish of a printed circuit board provides a number of functions, with impacts starting at the point of design and continuing through the life of the assembled product. Electroless nickel electroless palladium immersion gold (ENEPIG) is a surface finish that has been demonstrated to have a variety of benefits, and to be suitable for both SnPb and Pb-free circuit card assembly. Extensive testing of ENEPIG has demonstrated the reliability of this surface finish and resulted in the creation of an industry standard for its application: IPC-4556 Specification for Electroless Nickel/Electroless Palladium/Immersion Gold (ENEPIG) Plating for Printed Circuit Boards. When soldering to ENEPIG, all of the palladium is dissolved into the solder joint, and creates a palladium-rich region at the base (Pd source) of the solder joint. This palladium-rich microstructure can spall off, exhibiting a columnar shape. With ever decreasing size of parts used in electronics assembly, the size of the solder joints correspondingly continues to shrink, which causes the relative size of this palladium-rich microstructure to grow relative to the overall joint thickness. In this study, the impact of industry standard Pd thicknesses on thin solder joints is evaluated through shear testing.
Introduction
ENEPIG is a multi-layer surface finish for circuit boards. For soldering, the gold and Pd are applied to protect the solderability of the underlying Ni, and they are ultimately dissolved into the solder joint. Excessive amounts of these metals in the solder joint can potentially cause weakness of the solder joint, impacting reliability.
There is an industry specification (IPC-4556) that describes the requirements for ENEPIG, and the finish has some use in the industry, but is limited due to availability and the increased cost of the printed board (PB) relative to other surface finishes. The plated layers of ENEPIG are very flat, as all plated surface finishes are relative to Hot Air Solder Leveling (HASL), which makes it advantageous for smaller PB design features. As electronic component packaging technology advances and parts get smaller, the PB must have finer features to attach these parts. This decrease in feature size typically drives a decrease in solder paste stencil thickness for effective solder release, resulting in smaller solder joint volume. As the solder joint size gets smaller, the thickness of the surface finish on the PCB remains constant, so that the relative volume of gold and palladium in the solder joint increases. ENEPIG has been demonstrated to have acceptable performance and reliability for many current packages and solder joint configurations, but some studies raise concerns for use of ENEPIG at high concentrations or in very small solder joints1.
Round robin testing for the development of the IPC-4556 specification included palladium thicknesses of up to 17.95 microinches (µin). A 0.005-inch-thick stencil was used with a 0.025-inch diameter SnPb solder sphere, resulting a solder joint containing approximately 0.17% Pd. Shear testing of the solder ball on pad resulted in both lifted pads and cohesive failure in the bulk solder.
IPC-7095C Design and Assembly Process Implementation for BGAs warns of reliability impacts from excessive and non-uniform intermetallic compound (IMC) layer growth. IPC-4556 mentions a 3% limit for gold and palladium, and other sources have identified 2% as a limit2, but these limits based on a percentage are misleading when applied to Pd. Gold can (and is desired to) disperse throughout a solder joint to minimize impact, but Pd tends to form a distinct and concentrated IMC layer above the Ni.
Palladium has a slower solubility rate in molten solder than other metals. During soldering, the tin-palladium intermetallic compounds (either PdSn3 or PdSn4) will rapidly grow in the form of a thick lamellar structure perpendicular to the original palladium surface. Solder, consisting of a lead-rich phase, will be present between the lamellae. Further aging of solder joint can result in the movement (spalling) of the tin-palladium layer into the bulk solder and likely leave tin-palladium crystals within the bulk solder.
ENEPIG has been found to be prone to brittle fractures. The tin-palladium layers that form directly above the nickel plating has been found to be brittle, although some studies indicate that this may be based on weakness of a phosphorus rich nickel layer, not necessarily the Pd intermetallics3. The presence of tin-palladium crystals within the bulk solder has not been well-documented in terms of the effect on solder joint integrity; however as a comparison, tin-gold intermetallic crystals in bulk solder have been shown to embrittle a solder joint, enabling fracture of the solder joint along the gold intermetallics. It has not been shown that Pd intermetallics can have a similar effect within the bulk solder, the typical failure is associated with brittle fracture at the PB pad.
Based on the initial formation of a thick lamellar Pd intermetallic structure above the Ni layer, a limit on Pd thickness may be more appropriate to prevent excessive intermetallic layer thickness. A higher Pd thickness leads to an increased interfacial IMC thickness, specifically when SnPb solder is used. A thin palladium layer should dissolve rapidly into molten solder and result in no detrimental effect on solder joint mechanical properties. A variety of Pd thickness percentages or thickness limits have been proposed, some of which are lower than the 12 µin limit in IPC-4556. One paper suggests a limit of 7.8 µin4, although one study found that Pd thickness as high as 20 µin had no impact on solder joint shear strength5.
In this study, PBs plated with a typical ENEPIG surface finish (per IPC-4556) will be assembled with a minimum amount of solder to create a very small solder joint where the Pd concentration becomes larger relative to the overall solder joint. Solder shear strength and solder joint analysis will be used to investigate the acceptability of using ENEPIG with SnPb solder in these very small solder joints.
Experimental Procedure
For assembly and testing, an existing test vehicle was selected for use with a small LGA package. Using an LGA package limits the solder volume in the solder joint since there is no contribution from a solder ball as there is in a BGA package, resulting in a higher Pd concentration in the solder joint. A small LGA package of 6 x 6 pad array was selected and will be installed at the four corners of a larger BGA footprint in a manner so that only the middle 4 x 4 array of pads on the part are soldered. This will be done to increase the quantity of data points for the shear test, and to limit the number of solder joints which will limit the shear force required to remove the part.
The test vehicles (24 total) were separated into four sets, with three of these sets going to three separate vendors (each of which used a different plating chemistry) for application of the ENEPIG finish, and the remaining set coated with HASL (control set). Once returned, the PBs were subjected to XRF for measurement of the tri-metal layer thicknesses. The data from these measurements is shown in Figure 2 (each vendor represented by a different color).
A stencil of 3 mil thickness was used for solder paste application. The apertures of the stencil were matched to the PB pads (as designed) at 14.8 mil diameter. Half of the assemblies were soldered using Sn63Pb37 solder of type 3 with RMA flux. The remainder of the assemblies were soldered using Sn62Pb36Ag2 solder of similar type and flux content.
Results
Fabrication of the test vehicles was completed and it was determined that the solder mask thickness was greater than desired (approximately 3.5–4.5 mil compared to 1.0 mil pad thickness). This was discovered during PB fabrication, as the thickness of the solder mask interfered with board electrical testing and the HASL process. Additional boards were fabricated with thinner solder mask to enable the HASL process on the control units. PBs with ENEPIG surface finish were not replaced.
To read this entire article, which appeared in the January 2017 issue of SMT Magazine, click here.
Suggested Items
SHENMAO Strengthens Semiconductor Capabilities with Acquisition of PMTC
07/10/2025 | SHENMAOSHENMAO America, Inc. has announced the acquisition of Profound Material Technology Co., Ltd. (PMTC), a premier Taiwan-based manufacturer of high-performance solder balls for semiconductor packaging.
KYZEN to Highlight Understencil and PCB Cleaners at SMTA Querétaro Expo and Tech Forum
07/09/2025 | KYZEN'KYZEN, the global leader in innovative environmentally responsible cleaning chemistries, will exhibit at the SMTA Querétaro Expo & Tech Forum, scheduled to take place Thursday, July 24, at Centro de Congresos y Teatro Metropolitano de Querétaro.
Driving Innovation: Direct Imaging vs. Conventional Exposure
07/01/2025 | Simon Khesin -- Column: Driving InnovationMy first camera used Kodak film. I even experimented with developing photos in the bathroom, though I usually dropped the film off at a Kodak center and received the prints two weeks later, only to discover that some images were out of focus or poorly framed. Today, every smartphone contains a high-quality camera capable of producing stunning images instantly.
Hands-On Demos Now Available for Apollo Seiko’s EF and AF Selective Soldering Lines
06/30/2025 | Apollo SeikoApollo Seiko, a leading innovator in soldering technology, is excited to spotlight its expanded lineup of EF and AF Series Selective Soldering Systems, now available for live demonstrations in its newly dedicated demo room.
Indium Corporation Expert to Present on Automotive and Industrial Solder Bonding Solutions at Global Electronics Association Workshop
06/26/2025 | IndiumIndium Corporation Principal Engineer, Advanced Materials, Andy Mackie, Ph.D., MSc, will deliver a technical presentation on innovative solder bonding solutions for automotive and industrial applications at the Global Electronics A