-
-
News
News Highlights
- Books
Featured Books
- smt007 Magazine
Latest Issues
Current IssueIntelligent Test and Inspection
Are you ready to explore the cutting-edge advancements shaping the electronics manufacturing industry? The May 2025 issue of SMT007 Magazine is packed with insights, innovations, and expert perspectives that you won’t want to miss.
Do You Have X-ray Vision?
Has X-ray’s time finally come in electronics manufacturing? Join us in this issue of SMT007 Magazine, where we answer this question and others to bring more efficiency to your bottom line.
IPC APEX EXPO 2025: A Preview
It’s that time again. If you’re going to Anaheim for IPC APEX EXPO 2025, we’ll see you there. In the meantime, consider this issue of SMT007 Magazine to be your golden ticket to planning the show.
- Articles
- Columns
Search Console
- Links
- Media kit
||| MENU - smt007 Magazine
Soldering Fumes in Electronics Manufacturing: Damaging Effects and Solutions for Removal
August 14, 2017 | by Stefan Meissner, ULT AG, and Arne Neiser, Seho Systems GmbHEstimated reading time: 3 minutes
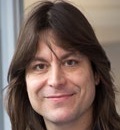
Modern electronics manufacturing is made up by a multiplicity of different separation and joining processes, with the later surely taking the vast majority of production technology. Alongside gluing, welding and laser processes, soldering still holds a primary position in electronic assemblies. However, soldering methods are not always equivalent, because there are quite a lot of different soldering technologies. Accordingly, you have to distinguish between automated and manual soldering procedures.
No matter which soldering process you analyze, all of them have one aspect in common: They produce airborne pollutants, which may have a negative impact on employees, plants and products as well.
Soldering Procedures in Electronics Manufacturing
There are a variety of soldering procedures, but not all of them are used in electronics manufacturing. Common soldering techniques in assembly production are:
• Wave soldering or flow soldering
• Reflow soldering
• Dip soldering
• Hot air soldering
• Selective soldering
• Laser soldering
• Vacuum soldering
• Vapor phase soldering
Figure 1: Selective soldering plant (Courtesy of SEHO Systems).
In the production of electronic assemblies, almost only soft soldering is used. The melting temperature of the solder is lower than the melting temperature of the elements to be joined (e.g. component leads to PCB pads [approx. 180 to 260°C]). The molten solder flows between the metal parts. The objective is to create a firm, airtight, corrosion-resistant, electrically and thermally conductive interconnection. The solder is mostly designed from alloys in the form of solder wire, solder bar or solder paste. Depending on the scope of application of the final product, these alloys are composed of tin, lead, antimony, silver and/or copper. In the solder, fluxing agents can be contained, which are compiled from different chemical compositions such as rosin. Normally, halogen-free flux agents are used to support the build of proper solder joints.
Automated Soldering Procedures and Hand Soldering
Figure 2: PCB during wave soldering process with soldering fumes (Courtesy of SEHO Systems).
Some decades ago, numerous workers, equipped with soldering irons, soldered electrical assemblies by hand, whereas today automated soldering systems of different size are used. These plants are highly specialized systems and perform a unique soldering technique (e.g. reflow soldering or selective soldering). The use of these systems depends on type and lot size of the assemblies. Many production lines feature different systems, which are used according to their distinct technology.
Hand soldering at manual workplaces is still found in the vast majority of assembly production plants. The main application area is for pre-production runs, prototyping and repair.
Released Airborne Pollutants
Depending on areas of application of the finished assembly and requirements of the components, various soldering alloys and flux agents are considered. During the soldering process, large parts of the flux agent and a small portion of the solder will evaporate. The emerging aerosols and particles could be released into ambient air. This will not only spread unpleasant odors, but these airborne pollutants can lead to serious medical conditions. Particularly dangerous substances are aldehydes, which emerge from materials containing colophony; some of them may be carcinogenic. In addition, gases are released from coatings, adhesives or substrates during heating of the assembly.
Figure 3: The threefold damaging effect of solder fumes.
These gases also transport sticky aerosols, which build up in the soldering machines or—even worse—on the products and contaminate them. This leads to increased cleaning and maintenance costs, and the operability of the plant can be impaired. In addition, the manufactured products may even be corroded by the contaminations, which could affect functionality and quality.
In conventional wave soldering processes, the entire printed circuit board is fluxed. The emerging spray mists from alcohol-based flux and other evaporations may lead to explosive, highly flammable vapor/air mixtures.
Differentiation and Legal Regulations
Airborne pollutants are classified according to particle size. This classification is set primarily by the influence of the emissions on the human organism. Thus, airborne pollutants are not only differentiated, whether they are brain, nerve or airway damaging. A distinction is made, whether they are inhalable (I-fraction) or alveolar (A-fraction). Pollutants of the A-fraction overcome the so-called lung-blood barrier, which separates air-filled cavities of the pulmonary alveolus from blood in the capillaries.
Therefore, the DIN EN 481 defines statutory limit values. According to technical rules for hazardous substances in various countries, there are limit values and legal regulations that determine the utilization of extraction and filtration technology to meet these regularities.
To read the full version of this article, which appeared in the August 2017 issue of SMT Magazine, click here.
Suggested Items
KYZEN to Focus on Aqueous Cleaning and Stencil Cleaning at SMTA Juarez
05/20/2025 | KYZEN'KYZEN, the global leader in innovative environmentally responsible cleaning chemistries, will exhibit at the SMTA Juarez Expo and Tech Forum, scheduled to take place Thursday, June 5 at the Injectronics Convention Center in Ciudad Jarez, Chihuahua.
Koh Young Installs 24,000th Inspection System at Top 20 EMS
05/14/2025 | Koh YoungKoh Young, the global leader in True 3D measurement-based inspection and metrology solutions, proudly announces the installation of its 24,000th inspection system at a Top 20 Global EMS in Thailand.
Indium’s Karthik Vijay to Present on Dual Alloy Solder Paste Systems at SMTA’s Electronics in Harsh Environments Conference
05/06/2025 | Indium CorporationIndium Corporation Technical Manager, Europe, Africa, and the Middle East Karthik Vijay will deliver a technical presentation on dual alloy solder paste systems at SMTA’s Electronics in Harsh Environments Conference, May 20-22 in Amsterdam, Netherlands.
SolderKing Achieves the Prestigious King’s Award for Enterprise in International Trade
05/06/2025 | SolderKingSolderKing Assembly Materials Ltd, a leading British manufacturer of high-performance soldering materials and consumables, has been honoured with a King’s Award for Enterprise, one of the UK’s most respected business honours.
Knocking Down the Bone Pile: Gold Mitigation for Class 2 Electronics
05/07/2025 | Nash Bell -- Column: Knocking Down the Bone PileIn electronic assemblies, the integrity of connections between components is paramount for ensuring reliability and performance. Gold embrittlement and dissolution are two critical phenomena that can compromise this integrity. Gold embrittlement occurs when gold diffuses into solder joints or alloys, resulting in mechanical brittleness and an increased susceptibility to cracking. Conversely, gold dissolution involves the melting away of gold into solder or metal matrices, potentially altering the electrical and mechanical properties of the joint.