-
- News
- Books
Featured Books
- smt007 Magazine
Latest Issues
Current IssueSpotlight on India
We invite you on a virtual tour of India’s thriving ecosystem, guided by the Global Electronics Association’s India office staff, who share their insights into the region’s growth and opportunities.
Supply Chain Strategies
A successful brand is built on strong customer relationships—anchored by a well-orchestrated supply chain at its core. This month, we look at how managing your supply chain directly influences customer perception.
What's Your Sweet Spot?
Are you in a niche that’s growing or shrinking? Is it time to reassess and refocus? We spotlight companies thriving by redefining or reinforcing their niche. What are their insights?
- Articles
- Columns
- Links
- Media kit
||| MENU - smt007 Magazine
Rework and Reliability: Less is More!
September 15, 2017 | Karen Tellefsen, Alpha Assembly SolutionsEstimated reading time: 4 minutes
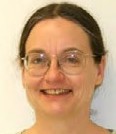
Circuit boards are not always perfect after reflow or wave soldering. Scrapping boards with one or two defects is expensive, so rework happens. A good concept for rework is less is more, especially less flux. Use as little rework flux as possible, as in the old Brylcreem ads, "Just a little dab'll do ya."
Liquid flux for rework is often supplied in felt-tipped applicator pens that make applying a few microliters of flux to a solder joint easy. Small squeeze bottles with tiny needle tips also work well. Paste/gel flux can be supplied in small syringes; use a small applicator tip to ensure that only a small dot of flux is applied to the rework site. Of course, using only no-clean, flux-cored solder wire without any assisting flux is the most electrochemically reliable way to do no-clean rework. The core flux in the wire will be properly heat deactivated because it will not flow until the wire is melted. Additionally, because core flux is mostly rosin or resin and hard, any activator remaining will be trapped in the flux residue. No-clean core fluxes are usually light colored and glass-like in appearance, providing nice cosmetics.
Most low solids, no-clean soldering fluxes must be exposed to soldering temperatures to become deactivated. The activator systems of these fluxes contain organic acids that remove oxides and allow solder to wet. When these organic acids are exposed to high enough temperatures for a long enough time, the activators volatilize and go away. If this doesn’t happen, the unheated or under-heated flux residues can allow electrochemical failures to occur, such as corrosion, reduction of insulation resistance, and, worst of all, electrochemical migration (Figure 1). If too much flux is applied to a rework site, some of the flux can move to nearby parts of the board that will not be exposed to the heat of the soldering tool. This often happens when flux is dispensed in large squeeze bottles with coarse tips. All those spikes in the SIR of the unheated flux are caused by the formation of dendrites between conductors.
Figure 1: SIR measurement of heated and unheated liquid, low-solids, no-clean flux.
So, how do unheated flux residues (and other contaminants) allow electrochemical problems to happen? A diagram showing these failure mechanisms is given in Figure 2. Many flux residues are hygroscopic, that is they absorb moisture from the air. This forms an electrolytic film on the board. The presence of this film allows small currents to flow between conductors at different voltages, reducing the surface insulation resistance (SIR). In some cases, the small current may cause electrolytic corrosion, which is the dissolution of metal from positively biased conductors. This rarely will cause a conductor to be completely eaten away and become an open circuit. It also can provide metal cations in the electrolyte film.
Figure 2: Electrochemical failure mechanisms caused by contaminants on circuit boards.
Now comes the worse and most destructive failure, electrochemical migration (ECM). Those metal ions in the electrolyte film will migrate to the cathodic, or negatively bias conductor because of the electrical field between the two conductors. When the metal cation gets to the cathode, it can pick up some electrons and deposit on the conductor. This deposition will usually occur at high energy locations, causing the formation of tree-like structures called dendrites. These dendrites will grow all the way to the opposing conductor causing a short circuit. These dendrites are delicate and can be destroyed by the resistive heating current flowing though the thin conductor. Noise results from the repeated forming and breaking of the dendrites, as seen in Figure 1.
Only J-STD-004B type -L0 and -L1 fluxes should be used for no-clean rework; fluxes that contain some rosin or a similar encapsulating resin, such as ROL0 and REL1, are even better. The rosin or resin in the flux will harden and help trap activators that weren’t completely heat deactivated.
Some circuit assemblers clean reworked areas with isopropyl alcohol or another solvent. For no-clean material rework, this is usually done for cosmetic reasons and more likely to hurt the electrochemical reliability than help it. No-clean fluxes are designed to be left on the circuit board. Spot cleaning may only move the dirt around. For circuits boards that are usually cleaned, spot cleaning reworked areas are not recommended. The board should be reworked with washable fluxes, and it should be put through the usual washing process again to ensure all rework fluxes are adequately removed from the board. This is especially important if the finished circuit is to be conformally coated, as coating over some flux residues can be worse than not coating at all.
In conclusion, be careful not to leave excessive or improperly heated flux residues after reworking circuit boards, or you might have more problems.
This article was originally published in the September 2017 issue of SMT Magazine.
Testimonial
"We’re proud to call I-Connect007 a trusted partner. Their innovative approach and industry insight made our podcast collaboration a success by connecting us with the right audience and delivering real results."
Julia McCaffrey - NCAB GroupSuggested Items
Indium Promotes Huang to Senior Manager, Marketing Communications
08/28/2025 | Indium CorporationWith its commitment to innovation and growth through employee development, Indium Corporation announces the promotion of Jingya Huang to Senior Manager, Marketing Communications, to continue to lead the company’s branding and promotional efforts.
Rehm Academy Expands Its Training Program
08/28/2025 | Rehm Thermal SystemsThe demands on modern industrial companies and employees continue to rise, and therefore, the topic of further education is becoming increasingly important today.
MacDermid Alpha Awarded for Innovation: Driving Process Optimization and Efficiency with Major Indian EMS Provider
08/28/2025 | MacDermid Alpha Electronics SolutionsMacDermid Alpha Electronics Solutions, a leading global supplier of integrated materials for the electronics industry, is recognized by one of India’s top EMS providers, Syrma SGS, with an award for innovation that advanced process optimization, enhanced operational efficiency, and yield gains.
Integrated Solutions for Board-level Reliability: A Smarter Path Forward
08/27/2025 | Alan Gardner, MacDermid Alpha Electronics SolutionsIn today’s electronics manufacturing landscape, reliability is no longer just a benchmark but a business imperative. As industries such as automotive, aerospace, and high-performance computing (HPC) push the boundaries of innovation, the demand for dependable board-level performance under extreme conditions has never been greater.
ZESTRON Expands Capabilities with Addition of the EPS by i-Tech AG 75 Pallet Cleaning System
08/26/2025 | ZESTRONZESTRON, the global leader in high-precision cleaning solutions and services, is excited to announce the addition of a new capability in its Technical Center in Manassas, VA: