Metal Printing Offers Low-Cost Way to Make Flexible, Stretchable Electronics
December 29, 2017 | North Carolina State UniversityEstimated reading time: 1 minute
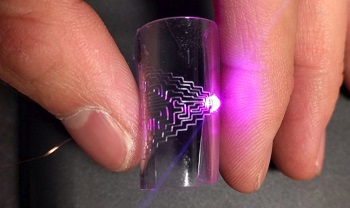
Researchers from North Carolina State University have developed a new technique for directly printing metal circuits, creating flexible, stretchable electronics. The technique can use multiple metals and substrates and is compatible with existing manufacturing systems that employ direct printing technologies.
“Flexible electronics hold promise for use in many fields, but there are significant manufacturing costs involved – which poses a challenge in making them practical for commercial use,” says Jingyan Dong, corresponding author of a paper on the work and an associate professor in NC State’s Edward P. Fitts Department of Industrial & Systems Engineering.
“Our approach should reduce cost and offer an efficient means of producing circuits with high resolution, making them viable for integrating into commercial devices,” Dong says.
The technique uses existing electrohydrodynamic printing technology, which is already used in many manufacturing processes that use functional inks. But instead of ink, Dong’s team uses molten metal alloys with melting points as low as 60 degrees Celsius. The researchers have demonstrated their technique using three different alloys, printing on four different substrates: one glass, one paper and two stretchable polymers.
“This is direct printing,” Dong says. “There is no mask, no etching and no molds, making the process much more straightforward.”
The researchers tested the resilience of the circuits on a polymer substrate and found that the circuit’s conductivity was unaffected even after being bent 1,000 times. The circuits were still electrically stable even when stretched to 70 percent of tensile strain.
The researchers also found that the circuits are capable of “healing” themselves if they are broken by being bent or stretched too far.
“Because of the low melting point, you can simply heat the affected area up to around 70 degrees Celsius and the metal flows back together, repairing the relevant damage,” Dong says.
The researchers demonstrated the functionality of the printing technique by creating a high-density touch sensor, fitting a 400-pixel array into one square centimeter.
“We’ve demonstrated the resilience and functionality of our approach, and we’re open to working with the industry sector to implement the technique in manufacturing wearable sensors or other electronic devices,” Dong says.
Suggested Items
Tata Electronics, Bosch Sign MoU for Strategic Collaboration in Electronics and Semiconductor Manufacturing
07/18/2025 | Tata ElectronicsTata Electronics, a leading player in the Indian electronics and semiconductor manufacturing sector, and Robert Bosch GmbH, a leading global supplier of technology and services, announced that they have signed a Memorandum of Understanding (MoU) to collaborate on several key areas within the electronics and semiconductor industries.
HANZA Accelerates the LYNX Program Through Acquisition of Defense Manufacturer
07/18/2025 | HANZAHANZA AB has signed an agreement to acquire the contract manufacturing division of Milectria, a group of companies focused on the defense sector.
NEOTech’s Agave 1 Facility Earns AS9100 Certification for Commercial Aerospace Manufacturing Excellence
07/17/2025 | NEOTechNEOTech, a premier provider of electronic manufacturing services (EMS), integrated design engineering, and advanced supply chain solutions for the aerospace and defense, medical device, and high-tech industrial markets, proudly announces that its Agave 1 manufacturing facility in Juarez, Mexico has officially received AS9100 certification.
Libra Industries Launches In-House High Precision Underfill Capabilities
07/17/2025 | Libra IndustriesLibra Industries, a leading provider of systems integration and electronics manufacturing services (EMS), is excited to announce the addition of high-precision underfill to its in‑house manufacturing capabilities.
Fraunhofer IPMS, DIVE Optimize Semiconductor Processes with Cutting-Edge Measurement System
07/17/2025 | Fraunhofer IPMSThe Fraunhofer Institute for Photonic Microsystems IPMS, in collaboration with DIVE imaging systems GmbH, has achieved a major milestone in resource-efficient semiconductor manufacturing.