-
- News
- Books
Featured Books
- smt007 Magazine
Latest Issues
Current IssueMoving Forward With Confidence
In this issue, we focus on sales and quoting, workforce training, new IPC leadership in the U.S. and Canada, the effects of tariffs, CFX standards, and much more—all designed to provide perspective as you move through the cloud bank of today's shifting economic market.
Intelligent Test and Inspection
Are you ready to explore the cutting-edge advancements shaping the electronics manufacturing industry? The May 2025 issue of SMT007 Magazine is packed with insights, innovations, and expert perspectives that you won’t want to miss.
Do You Have X-ray Vision?
Has X-ray’s time finally come in electronics manufacturing? Join us in this issue of SMT007 Magazine, where we answer this question and others to bring more efficiency to your bottom line.
- Articles
- Columns
- Links
- Media kit
||| MENU - smt007 Magazine
Indium's Karthik Vijay Talks Engineering for Automotive Applications
January 22, 2018 | Barry Matties, I-Connect007Estimated reading time: 16 minutes
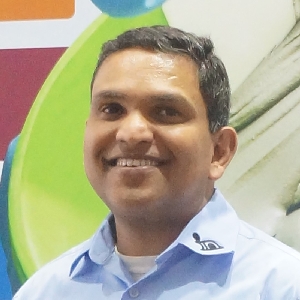
As head of Indium Corporation’s application support team in Europe, Karthik Vijay is at the center of the complex material challenges faced by the world’s biggest automotive manufacturers in their creation of PCBs and power modules. Barry Matties met with Karthik at last year's productronica, where everything from stencils and laser cutting to flux technology and jetting were discussed. If you want to know about where material technology currently stands in the automotive landscape, you’ll want to read on.
Barry Matties: Karthik, why don't you just tell me a little bit about yourself.
Karthik Vijay: Sure. In my current role, I'm responsible for the application support team in Europe, and we are responsible for supporting customers by providing technical knowledge, helping them with evaluations, and ongoing product assistance. I’ve been with Indium Corporation for close to 14 years.
Matties: You're in a unique position as an application engineer. You must get to see a lot of the different projects and challenges out there. What are some of the most interesting ones you've come across so far?
Vijay: I'd say automotive. Three to five years ago, it wasn’t considered as exciting; however, this is a good time to be in automotive electronics. We are seeing multiple technology drivers. For instance, there are different levels of autonomy leading eventually to the fully autonomous vehicle, more electrification of normal cars, as well as semi-hybrids and hybrids. Then there are driverless systems that are going to become mandatory because they're safety related with a lot of sensors.
There is 48-volt technology that basically helps reduce even further CO2 emissions. With all this, it throws up some very unique challenges and obvious opportunities, because in the automotive industry, the mindset has always been, "Once you're in, you're in." It becomes difficult to break in, but because of all the challenges, the automotive industry has opened up like no time before. With the level of miniaturization that we’re seeing and being in sync with, say, mobile technology in terms of miniaturization and the complexity, the industry is catching up really fast.
Matties: So that's a general overview of the challenges, but what are some of the specific challenges that your customers are facing?
Vijay: Again, in the context of the technology drivers and the autonomous vehicles, the challenges are from a materials standpoint. If you look at fluxes in the past, they needed to be rated from an electrical reliability standpoint. At minimum, I'll say a value of 100 megaohms needed to be measured over 168 hours, or seven days, for a voltage of five volts and a pitch of 0.5 millimeter. Today, customers are asking for 5,000 megaohms for 1,000 hours with a voltage of 10 to 50 volts, and a pitch of 0.2 to 0.3 millimeters—so a world of difference. Additionally, if you look at mechanical thermal cycling reliability, what was rated for 1,000 cycles before now needs to be rated to 3,000 to 6,000 cycles, and surface temperature has increased from 125°C to 150°C. At that temperature, traditional alloys don’t perform as well because the delta between the melting point of the alloy and the surface temperature has now decreased significantly. That means there's a higher chance of failure during thermal cycling.
Alloy selection must take into consideration not only mechanical rigidity or hardness, but with increased surface temperature, you've got exponentially different CTE mismatches which means you've got to have ductility as well. Hitting that sweet spot between hardness and ductility is key to withstanding more stringent performance requirements at increased surface temperatures with enhanced reliability. In addition, we need to eliminate head-in-pillow and graping, so it's not an either/or. It's got to check all these boxes. That's where material technology becomes very important.
Matties: Because it's all mission-critical in automobiles, right? Especially the autonomous.
Vijay: Absolutely.
Matties: When you start looking at the autonomous vehicles, how great of a challenge is that in the engineering phase or what do you see has the greatest challenge in the autonomous?
Vijay: There are five levels of autonomy. It is estimated to be 20-30 years for autonomous vehicles to become mainstream technology. Having said that, if you are looking at the various levels of semi-autonomy, which it's going to come to, that is imminent. In the next 24 months to the next five years, where qualifications are going on as we speak, for it to be fully functional for production validation (PV) and start of production (SOP) builds, say in the next two to three years. Because it's safety related, a lot of work goes into it. The challenges tie in with what I mentioned earlier. As an example, with autonomous or semi-autonomous vehicles, in addition to camera and vision systems, and radar and lidar, there are now sensors.
For all of this, there’s active and passive safety. Passive safety is an example of a camera sending an image and then the driver decides to react. Active safety is the camera seeing something, sending a message, and telling the car to do something specific. The requirements and challenges of active safety from a complexity standpoint are monumentally different compared to passive safety. Now you've got temperature-sensitive components, and the temperature-sensitive components have, for example, a vision system that can only see up to 240°C. A traditional SAC alloy becomes a challenge because your peak temperature, dealing with the reflow profile, can be anywhere in the region of 235–255°C. That means a need for lower melting point alloys.
Matties: So it's at risk for failure.
Vijay: Exactly. But if you look at lower melting point alloys, they have not yet really been proven for these stringent reliability requirements. It is a challenge, but again, it becomes an opportunity as well.
Matties: Are there new standards being created as we talk for this application?
Vijay: Oh, yes.
Matties: Are you a part of that process?
Vijay: Yes. The automotive industry is involved both with the end customers as well as their tier one suppliers. They are also involved as a supplier because it goes down the supply chain. We are all involved in this discussion especially in safety systems.
Page 1 of 4
Suggested Items
Hands-On Demos Now Available for Apollo Seiko’s EF and AF Selective Soldering Lines
06/30/2025 | Apollo SeikoApollo Seiko, a leading innovator in soldering technology, is excited to spotlight its expanded lineup of EF and AF Series Selective Soldering Systems, now available for live demonstrations in its newly dedicated demo room.
Indium Corporation Expert to Present on Automotive and Industrial Solder Bonding Solutions at Global Electronics Association Workshop
06/26/2025 | IndiumIndium Corporation Principal Engineer, Advanced Materials, Andy Mackie, Ph.D., MSc, will deliver a technical presentation on innovative solder bonding solutions for automotive and industrial applications at the Global Electronics A
Fresh PCB Concepts: Assembly Challenges with Micro Components and Standard Solder Mask Practices
06/26/2025 | Team NCAB -- Column: Fresh PCB ConceptsMicro components have redefined what is possible in PCB design. With package sizes like 01005 and 0201 becoming more common in high-density layouts, designers are now expected to pack more performance into smaller spaces than ever before. While these advancements support miniaturization and functionality, they introduce new assembly challenges, particularly with traditional solder mask and legend application processes.
Knocking Down the Bone Pile: Tin Whisker Mitigation in Aerospace Applications, Part 3
06/25/2025 | Nash Bell -- Column: Knocking Down the Bone PileTin whiskers are slender, hair-like metallic growths that can develop on the surface of tin-plated electronic components. Typically measuring a few micrometers in diameter and growing several millimeters in length, they form through an electrochemical process influenced by environmental factors such as temperature variations, mechanical or compressive stress, and the aging of solder alloys.
SolderKing’s Successful Approach to Modern Soldering Needs
06/18/2025 | Nolan Johnson, I-Connect007Chris Ward, co-founder of the family-owned SolderKing, discusses his company's rapid growth and recent recognition with the King’s Award for Enterprise. Chris shares how SolderKing has achieved these award-winning levels of service in such a short timeframe. Their secret? Being flexible in a changing market, technical prowess, and strong customer support.