-
- News
- Books
Featured Books
- smt007 Magazine
Latest Issues
Current IssueWhat's Your Sweet Spot?
Are you in a niche that’s growing or shrinking? Is it time to reassess and refocus? We spotlight companies thriving by redefining or reinforcing their niche. What are their insights?
Moving Forward With Confidence
In this issue, we focus on sales and quoting, workforce training, new IPC leadership in the U.S. and Canada, the effects of tariffs, CFX standards, and much more—all designed to provide perspective as you move through the cloud bank of today's shifting economic market.
Intelligent Test and Inspection
Are you ready to explore the cutting-edge advancements shaping the electronics manufacturing industry? The May 2025 issue of SMT007 Magazine is packed with insights, innovations, and expert perspectives that you won’t want to miss.
- Articles
- Columns
- Links
- Media kit
||| MENU - smt007 Magazine
Use of Lean Manufacturing Principles Enhances Quality and Productivity
August 22, 2018 | Mike Baldwin, Spectrum Assembly Inc.Estimated reading time: 2 minutes
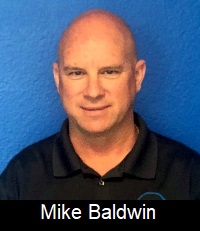
Regional EMS providers typically provide greater flexibility and responsiveness to their box build customers via use of work-cell-based batch assembly processes. Production volumes are fairly low, so the creation of dedicated continuous flow paced assembly lines is rare. However, we often see larger footprints and more complex projects with higher volumes.
Our cable, harness and PCBA manufacturing capabilities attract companies with products requiring complex subassemblies. As a result, it utilizes both work-cell-based and continuous-flow-line assembly in its box build assembly area.
One recent project example illustrates why this flexibility is important. The customer develops sports therapy devices used by trainers and professional sports teams. They had a next-generation product that increased functionality and, as a result, became mechanically much more complex. They needed a contract manufacturer capable of assisting them with development of mechanical manufacturing process instructions in addition to manufacturing the product. SAI helped develop the manufacturing process instructions as part of its new product introduction (NPI) services. The customer’s documentation for wire and cable assemblies, electronic assemblies, mechanical assemblies and cosmetics requirements is transmitted to the Aegis system and used to create visual work instructions that are utilized by the production team.
This project included cables, harnesses, PCBAs, electro-mechanical, fluidic, air and water subassemblies as well as chassis, sheet metal, plastics and hardware components. Routing the tubing in a limited chassis space was a challenge. Our team used the same process templates used in developing efficient wire and harness routing to route the fluidic, air and water lines. Trial builds were performed to ensure correct air pressure and water flow, and once nailed down, a tubing cut list was developed to make sure that all tubing was cut to appropriate lengths for the preferred routing. The customer validated the process. While computer modeling of this type of routing seems efficient, a routing that looks great on the computer screen can turn out to be an inefficient order of operations on the production line based on the obstacles that operators encounter during the assembly process. Having a combination of computer modelling and hands-on trial builds meant nothing was missed and that the order of operations was fully optimized.
Initially, the project was planned as a batch build process in several dedicated work cells, however, the volumes quickly outgrew that model. Our team utilized Lean manufacturing principles to redesign production flow from a cellular manufacturing process to a single conveyorized production line that integrated subassemblies with final assembly. Lean manufacturing principles were a core part of this redesign effort.
In the original process, cables, harnesses, PCBAs and subassemblies were assembled separately and pulled from stock. Final units were assembled sequentially by a pair of production operators.
The redesigned line has seven "feeder" work cells where production operators build electronic subassemblies consisting of multiple PCBAs, an onboard computer and associated harnesses; the fluidics; heating elements, cooling elements and additional subassemblies. In total, there are over 800 line items, seven custom PCBAs and 37 custom cables. At each station, operators add their subassembly to the base unit as it moves down the conveyor line. Programming, serialization, functional test, burn-in and crating are located at the end of the line. As part of this process, a 17-page device history record (DHR) is created and electronically filed for future use.
To read the full version of the article, which appeared in the July 2018 issue of SMT007 Magazine, click here.
Suggested Items
Flex CEO Sees US Manufacturing Resurgence
06/18/2025 | I-Connect007In a June 16 interview on Bloomberg Open Interest, Flex CEO Revathi Advaithi said the supply chain is already shifting, with more goods now being manufactured in the U.S.
Altus Supports Phoenix Systems in Advancing THT Assembly with Robotic Soldering
05/27/2025 | Altus GroupAltus Group, a leading distributor of capital equipment in the UK and Ireland, has successfully supported Phoenix Systems UK Ltd in its investment in robotic soldering technology to further enhance its through-hole technology (THT) assembly processes.
Vertical Aerospace Makes Aviation History with Piloted eVTOL Flight in Open Airspace
05/27/2025 | BUSINESS WIREVertical Aerospace, a global aerospace and technology company that is pioneering electric aviation, announced it has made European aviation history with the first-ever piloted wingborne flight of a winged electric vertical take-off and landing (eVTOL) aircraft in open airspace.
Harnessing Connections: EWPTE 2025 Draws Nearly 3,000 Attendees
05/19/2025 | IPCThe 2025 Electrical Wire Processing Technology Expo (EWPTE), held May 6-8 at Baird Center in Milwaukee, Wis., provided 2,994 attendees the opportunity to meet, network and learn from the industry leading innovators and suppliers.
AI Helps Build Smarter, More Resilient Power Grids
05/16/2025 | BUSINESS WIREAs society’s reliance on electricity deepens, artificial intelligence (AI) is reshaping how we manage power grids and optimize energy sources.