-
-
News
News Highlights
- Books
Featured Books
- smt007 Magazine
Latest Issues
Current IssueWhat's Your Sweet Spot?
Are you in a niche that’s growing or shrinking? Is it time to reassess and refocus? We spotlight companies thriving by redefining or reinforcing their niche. What are their insights?
Moving Forward With Confidence
In this issue, we focus on sales and quoting, workforce training, new IPC leadership in the U.S. and Canada, the effects of tariffs, CFX standards, and much more—all designed to provide perspective as you move through the cloud bank of today's shifting economic market.
Intelligent Test and Inspection
Are you ready to explore the cutting-edge advancements shaping the electronics manufacturing industry? The May 2025 issue of SMT007 Magazine is packed with insights, innovations, and expert perspectives that you won’t want to miss.
- Articles
- Columns
- Links
- Media kit
||| MENU - smt007 Magazine
Understanding the Benefits of CFX
November 30, 2018 | Stephen Las Marias, I-Connect007Estimated reading time: 5 minutes
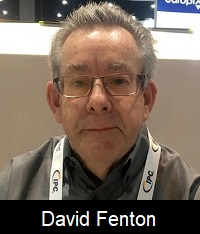
David Fenton is the group customer support manager for Blakell Europlacer. He is responsible for all of the service teams worldwide, including in China, Germany, Italy, France, the U.K., and U.S. In this interview with SMT007 Magazine, Fenton discusses technical challenges and the impact of the IPC Connected Factory Exchange (CFX) initiative on the PCB assembly industry, and what manufacturers can expect from this electronics assembly connectivity standard.
Stephen Las Marias: David, what has been your experience so far while working on and supporting CFX?
David Fenton: There has been talk around Industry 4.0 and smart factories for many years. Until very recently, we felt that it was just a lot of noise. Nobody knew what to expect out of Industry 4.0, and then other companies started to release their own standards under the Industry 4.0 banner. Europlacer stood back, listened, and waited to see what would happen. Then, we had an opportunity to listen to Michael Ford of Aegis Software in one of the exhibitions. We became interested in what they were doing with the IPC CFX standard. We realized Aegis was taking it very seriously, and that they had the power of IPC behind it. We’ve been working with Aegis for many years, so we know them very well. Once we saw they were involved, we started following the CFX standard to see how it was going. We regularly contact Michael. When we saw the original draft standards from IPC, we realized it was a standard that should be very easy to implement for our programmers, and could be a truly global standard. Thus, we started working with Michael and made some test code using a program provided by Aegis. For me, that was the key to making this work.
Aegis has done a lot of the groundwork to make it simple for vendors like Europlacer to take part in CFX. We had test codes up and running within 48 hours with receipt of the software development (SD) kit from Aegis. We realized this was going to be easy for us to do, so why not try it?
We have seen it gain traction. Vendors are being added to the list all the time, and we realized some of the big players were going down the CFX route. Then, we had the demonstration at IPC APEX EXPO, which went off without a hitch. The cloud server worked well and required minimal effort. We recently participated in the demonstration at SMT Hybrid Packaging Nuremberg, which also went very well.
In all of these cases, we used a cloud server provided by Aegis and IPC. Recently, we’ve gone out on our own such that we don’t necessarily need to involve any third party if the customer wants an entirely internal system without a cloud-based interface. We’ve taken that product standard further to have an in-house broker system. Again, it was relatively easy to develop. We also recently had an industry open day where Michael talked about Industry 4.0 and CFX. At the same time, we were able to demonstrate the Europlacer system in our facility.
That’s where we are today. We’ve offered to help IPC create messages for pick-and-place equipment. They are always looking for vendors to help construct the format of CFX to add new messages all the time. By getting in first, our messages will become a part of it. By doing this, we felt there would be less work for our programmers. If we’d gone down a path that wasn’t included in the standard, we would need to recode that. Volunteering on the committee writing the message standards will help us in the future.
We can also customize the messages to a certain degree for our equipment. For example, we have multiple heads on the machines.
The standard as it existed didn’t have any facilities to create messages for multiple-headed machines or give information on an individual head’s performance. We have sent those unique messages to IPC. Hopefully, they will be accepted to the draft standards.
Las Marias: What do you think is the challenge that CFX is trying to address?
Fenton: That is an interesting question because I am not sure that customers know they have a challenge yet. CFX is still an industry standard that is ahead of the demand. We have many customers worldwide, and it’s not something that is on their radar. The more we promote it, the more they realize there is a need. It’s slightly backward. As far as our customers in the small- to medium-end markets are concerned, they have never pushed us for this type of data gathering until very recently.
However, the challenge is that it would hopefully sell and be able to take in data from anybody’s machine—not just Europlacer’s—and display it on a standard dashboard without having to write custom front-end data for the dashboards. Over time, the challenge will be to combine data from multiple vendors into one common platform.
Las Marias: What can you say about the state of interest in CFX?
Fenton: To be perfectly honest, it is lower than I thought. We saw hundreds of people over the course of the previous show, and when we spoke with the various demonstrators, engineers, and salespeople, very few attendees had asked about CFX or Industry 4.0. At the moment, I still think it’s a bit of a tick box that the industry needs to promote the benefits. As the months go by, people will start to realize what CFX can do. Our customers are still confused as to what Industry 4.0 can do. CFX is not something that is as important to them as machine uptime, speed, and productivity.
Las Marias: In a nutshell, how is CFX impacting the PCB assembly industry and what are its benefits?
Fenton: Once the data gathering is established, the customer will be able to look at their overall efficiency, overall equipment effectiveness (OEE), underboards, bridges, and first-time yield, among others—which is something that they struggle with at the moment because the data is not in a standard format.
If they look at the OEE data from their automated optical inspection (AOI) machine, printer, or oven, they have to gather separate types of information and may have several different dashboards or ways to read the data. Overall, the effect of CFX will be to make productive decisions easier because users will be able to look at factory-wide statistics as opposed to individual machines. As a result, users will be able to turn the data from individual machines into a picture of what their overall factory efficiency is. I see this as the primary benefit. If you make something easy for a customer, they will start to use it, and then they’ll see the benefit of making changes in material handling or operator training. This is the type of thing where they will be able to make small changes to their methods and see the data immediately from any machine in the factory.
To read the full article, which appeared in the October 2018 issue of SMT007 Magazine, click here.
Suggested Items
TRI to Exhibit at SMTA Queretaro Expo 2025
07/16/2025 | TRITest Research, Inc. (TRI), the leading provider of test and inspection systems for the electronics manufacturing industry, is pleased to announce plans to exhibit at the SMTA Querétaro Expo 2025, scheduled to take place on July 24, 2025, at the Querétaro Centro de Congresos y Teatro Metropolitano.
Global PCB Connections: Let the Spec Fit the Board, Not Just the Brand
07/17/2025 | Jerome Larez -- Column: Global PCB ConnectionsIf you’ve ever seen an excellent PCB quote delayed, or worse, go cold because of a single line on the fab print, you’re not alone. Often, that line reads something like, “Use 370HR only,” or “IT-180A required.” These and other brand-name materials are proven performers, but unless your design needs that specific resin system (say, for RF performance, thermal reliability, or stringent CAF resistance), you may inadvertently be holding your job hostage.
IPC Hall of Fame Spotlight Series: Highlighting Lionel Fullwood
07/15/2025 | Dan Feinberg, I-Connect007Many IPC members who have contributed significantly to IPC and our industry have been awarded the IPC Raymond E. Pritchard Hall of Fame (HOF) Award. Though many early HOF members have passed away and are unknown to today’s IPC membership, their contributions still resonate. This special series on IPC Hall of Fame members provides a reminder of who was honored and why. As a bonus, for those who are still around, we get to find out what these talented individuals are up to today.
TRI Unveils New Platform for Diverse Board Sizes
07/14/2025 | TRITest Research, Inc. (TRI), the leading test and inspection systems provider for the electronics manufacturing industry, proudly introduces a new size configuration for SPI and AOI Models.
Seeing a Future in Mexico
07/09/2025 | Michelle Te, I-Connect007The Global Electronics Association (formerly known as IPC) has been instrumental in fostering a partnership with Guanajuato, a state north of Mexico City with 12 industrial clusters and close to 150 companies involved in electronics. This past spring, Alejandro Hernández, the undersecretary for investment promotion in Guanajuato, attended IPC APEX EXPO 2025 at the invitation of IPC Mexico Director Lorena Villanueva, where he met with several companies to discuss the opportunities available in Mexico. He is inviting electronics-related companies seeking long-term investment in a centrally located area with access to highways, railways, and ports.