-
- News
- Books
Featured Books
- smt007 Magazine
Latest Issues
Current IssueWhat's Your Sweet Spot?
Are you in a niche that’s growing or shrinking? Is it time to reassess and refocus? We spotlight companies thriving by redefining or reinforcing their niche. What are their insights?
Moving Forward With Confidence
In this issue, we focus on sales and quoting, workforce training, new IPC leadership in the U.S. and Canada, the effects of tariffs, CFX standards, and much more—all designed to provide perspective as you move through the cloud bank of today's shifting economic market.
Intelligent Test and Inspection
Are you ready to explore the cutting-edge advancements shaping the electronics manufacturing industry? The May 2025 issue of SMT007 Magazine is packed with insights, innovations, and expert perspectives that you won’t want to miss.
- Articles
- Columns
- Links
- Media kit
||| MENU - smt007 Magazine
Mentor and Seica Partner for Data Prep and Testing Big Boards
January 18, 2019 | Pete Starkey, I-Connect007Estimated reading time: 9 minutes
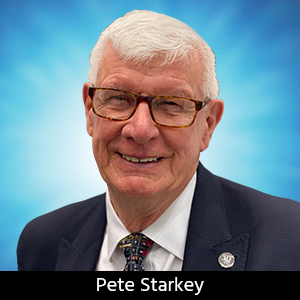
Mark Laing, business development manager of the Valor division at Mentor, a Siemens company, and Luca Corli, director of sales at Seica, address the partnership between their two companies, which enables efficient data preparation for testing big boards, and accelerates new product introduction (NPI) cycles.
Pete Starkey: Today, I’m here with Mark Laing and Luca Corli to talk about a good example of how two experts in their own fields can cooperate to bring about a synergistic benefit. Gentlemen, it's great to meet you both. Thanks for taking the time to join me. Luca, can you give me a bit of background? We identify Seica as a leading supplier of flying probe test equipment, but what have been the challenges that you've had to address recently?
Luca Corli: First of all, thank you for inviting me to this conversation. Seica has been in the business of flying probes for 23 years now. For 20 years, Seica has been as a manufacturer of flying probe testers from the mechanics to the hardware of measurements and software. We have been able to manage data coming from our customers to generate the test program—CAD data, design data—on our own by developing some software converters internally to transfer the design information into the language of our machine.
Three years ago, we finally came up with the idea to assign this part of the job to experts of the software environment because our customers were showing us multiple and more complex, different formats of their designs. Since the generation or translation of data is not really the main purpose of a tester, we decided to look around and find a partner—an expert in this environment—and use their expertise into our product. We found Mentor, a Siemens Business, as the best choice to fit our need.
Starkey: It's nice to hear an honest statement, and I think it's a very logical thing to do. You build testing machines, while Mentor is an expert in design and generating the right software for the right application.
Corli: Exactly, and the name of their software—Valor Process Preparation—means exactly what was needed by Seica to prepare to do the next step, which is the actual test of the board. This preparation phase was becoming too heavy to be managed only by Seica engineers. In our software, we already had a sort of wizard where we identified three phases: prepare, verify, and test. We want to focus now more on verify and test, so the prepare phase has been assigned to our friends at Mentor.
Starkey: What sort of boards are you finding the most challenging presently?
Corli: It's funny; most people are thinking about small components and devices, and the downsizing of boards because some products like smartphones are driving the market of devices. Meanwhile, we keep finding more and more customers building huge boards. And especially for flying probes, we have been driven to make a bigger machine instead of a smaller one. Our standard machine can test a board 24 by 21 inches, which is quite big—610 by 540 millimeters. However, it was not enough for some customers in the American market who are building even bigger boards.
So, we came up with the Pilot V8 Excel version of our flying probe, which can manage boards up to 31 by 25 inches. Of course, when you have such a big board full of components, you’re talking about a board with 7,000–8,000 nets and more than 20,000 components. You can imagine the amount of data they have to process at the design level and the amount of data we have to transfer into the prober to generate the test program. Mentor was dramatically helpful in that case, and we have been able to sell these kinds of machines because we are the only one able to process the data. This is fantastic for us and shows the win-win situation of this partnership between Mentor and Seica.
Starkey: Thank you, Luca. Mark, could I ask you to tell the story from your point of view? At what stage of the design generation are you taking the data to prepare the information needed to drive the tester?
Mark Laing: Traditionally, we use the results of design, and we look to do that not just for electrical tests but also for placement equipment, stencils, etc., and process that data once. As Luca mentioned, these sorts of datasets are getting larger and larger now—it's a lot of information. We benefit from being able to integrate with the design environment as well. There are changes in the design that can be made to further improve the coverage that we can pass on to our partners such as Seica, who can benefit from that from the design perspective. The types of board that Luca described are getting more and more common today, but we're also learning that these boards are going to get even bigger physically—and in terms of complexity—in the following years.
We very much need to understand not just how they're designing them, but also how they will ultimately test them as well. We prepare the data from the manufacturing perspective to pass that information to Seica, and also look upstream into the design environment and how those are being designed. We also advise further so that what ultimately gets delivered to the manufacturing test floor is something that can truly be tested to a very high degree as opposed to being constrained by that design as well. We’re in a unique position of being able to leverage the information from a design perspective and provide some consultancy to the customers to improve that, which ultimately allows Seica to do a better job in testing it.
There are a lot of scenarios today where they can feel constrained and not be able to do as good a job because of a sub-optimal layout. We're not just preparing that data for them, but we're helping the customer get a much better product out the door through the ability to improve that design to the benefit of the flying probe systems downstream that are having to deal with very complex designs with thousands and thousands of nets and components. That's what we see today. We're already hearing that this will increase into the next few years as well.
Luca makes a good point. We always hear about how things are getting smaller and smaller with IoT devices, and here we are with some things are getting bigger and bigger. It has certainly been challenging, and most of the solutions out there have not been able to handle what we've seen. We've taken advantage of both of our particular areas of expertise to provide solutions to this part of the market.
Starkey: If I'm a PCB fabricator or an engineer in an EMS company, at what stage do I get involved in this?
Laing: We certainly benefit from that involvement. The challenge is that these areas have been quite fragmented until now. One of the areas that we focus on—particularly from a DFM perspective—is that you can design the product, but ultimately, you need to build it. It doesn't matter that you can design the best product in the world. If you can't build it—which means building and testing it as well—these areas have to come together to be able to achieve that. When it involves simple products, that's one thing, but we see thousands and thousands of components placed down with these types of products; we're talking tens, hundreds, and even thousands of solder joints. That's a lot of verification that has to go on, and it requires the design and the manufacturing people to come together to evolve that design to allow it to be assembled and tested—not just designed.
Starkey: Really, we're in a situation where the whole of the supply chain gets involved. Again—putting myself in the position of the bare board fabricator or the assembler—if the job is been designed, verified, and presented properly, can you place it with anybody that has the capability to fabricate the bare board or to build the assembly?
Laing: Ultimately, you can get the job done. We can fabricate and build that board. The question is, how efficiently can we do that, and how much cost is going to go into achieving that? That can be enough to make or break the product. Whereas, if we get those groups to work together and learn from mistakes that were made in the past to effect change in the design, then we make it more efficient and cost-effective moving forward.
Starkey: It's about breaking down barriers. In my days as a fabricator, I spent a lot of my time beating my head against brick walls to try and knock them down. The designer would do their design, then throw it over the wall into a fabrication shop. The fabricator would do their job, then throw it over the wall into the assembly shop. They wouldn't talk to each other or understand one another’s problems or limitations. Each one effectively worked in isolation. We're in a situation now where everybody is talking to everybody all the way down the line such that at the end of the line, you have a product that works, is reliable, and has been manufactured cost-effectively.
Laing: In these sorts of examples, you have to do that. It's not optional. It's a mandatory ability to have design, manufacturing, and test all working together because the products are so complex with many opportunities for issues. We need to cover all of those bases; otherwise, you wouldn't even build one.
Starkey: Is there anything more that we need to talk about? I think we've covered a lot of ground.
Corli: I could add one more thing. This world is running so fast, sometimes too fast. However, people expect a quick result from a flying prober in terms of tests. A flying prober is something where I give you the data, and you give me the completed test on the same day. There is no time to lose because the data does not match the format the machine is expecting. Before, it was more okay to have a few more hours or days to fix the data and change the format. Today, customers are looking to get it done and tested as soon as they get the board. So, the transition time between taking the data and putting the data into the machine is almost zero. That's why we need something working immediately, and that's why the expert can do that.
Starkey: I think you've made that very clear between the two of you. Thank you very much for your time. It’s been most interesting. We’ll include a link to the press release about this partnership as well.
Laing: Thank you very much.
Corli: Thank you.
Suggested Items
SHENMAO Strengthens Semiconductor Capabilities with Acquisition of PMTC
07/10/2025 | SHENMAOSHENMAO America, Inc. has announced the acquisition of Profound Material Technology Co., Ltd. (PMTC), a premier Taiwan-based manufacturer of high-performance solder balls for semiconductor packaging.
KYZEN to Highlight Understencil and PCB Cleaners at SMTA Querétaro Expo and Tech Forum
07/09/2025 | KYZEN'KYZEN, the global leader in innovative environmentally responsible cleaning chemistries, will exhibit at the SMTA Querétaro Expo & Tech Forum, scheduled to take place Thursday, July 24, at Centro de Congresos y Teatro Metropolitano de Querétaro.
Driving Innovation: Direct Imaging vs. Conventional Exposure
07/01/2025 | Simon Khesin -- Column: Driving InnovationMy first camera used Kodak film. I even experimented with developing photos in the bathroom, though I usually dropped the film off at a Kodak center and received the prints two weeks later, only to discover that some images were out of focus or poorly framed. Today, every smartphone contains a high-quality camera capable of producing stunning images instantly.
Hands-On Demos Now Available for Apollo Seiko’s EF and AF Selective Soldering Lines
06/30/2025 | Apollo SeikoApollo Seiko, a leading innovator in soldering technology, is excited to spotlight its expanded lineup of EF and AF Series Selective Soldering Systems, now available for live demonstrations in its newly dedicated demo room.
Indium Corporation Expert to Present on Automotive and Industrial Solder Bonding Solutions at Global Electronics Association Workshop
06/26/2025 | IndiumIndium Corporation Principal Engineer, Advanced Materials, Andy Mackie, Ph.D., MSc, will deliver a technical presentation on innovative solder bonding solutions for automotive and industrial applications at the Global Electronics A