Which IPC-A-610 Class is Best for Your PCBA?
April 8, 2019 | Neil Sharp, JJS ManufacturingEstimated reading time: 3 minutes
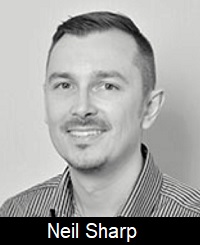
When you think about what makes a good electronics assembly, what are the most common expectations that come to mind? If the assembly works as intended, then surely that indicates a certain level of acceptability, right? But what about the product's longer-term reliability? And what if you'd also like it to look good too?
Printed circuit board assembly (PCBA) is a surprisingly complex thing. There’s the PCB itself with all of its materials, finishes, and various components, and the solder that holds everything together. Within that, there’s also a fair amount of scope for things to be good, bad, or somewhere in between.
For many electronics manufacturing services (EMS) providers, IPC-A-610: Acceptability of Electronic Assemblies is the agreed standard that we use to define what's acceptable and what's not in the world of PCBA production. The standard is comprised of three Classes: 1, 2, and 3. As an original equipment manufacturer (OEM), it’s important that you're clear on the basic principles that separate those classes so that you have a clear and realistic expectation of what the results are going to be.
Class 1
The lowest IPC-A-610 class, Class 1, is the most lenient when it comes to making allowances for potential defects. When we think of the functionality of the electronics assembly within a simple toy, for example, the PCBA is likely to be hidden well away inside the body of the item, so the quality of the solder joints or component positions may not be such a high priority. The product is also likely to be manufactured to very tight margins (read "as cheaply as possible"). So, as long as the item still functions as expected and its operational life sits within an acceptable timeframe, then that will probably be sufficient.
Class 2
Class 2 is typically the most requested for non-critical electronic assemblies where longer-term reliability is desirable, but perhaps not essential. Class 2 still allows for a certain degree of imperfection. Surface-mount components that have been placed slightly off pad, for instance, are usually still fine electrically and mechanically even though they may look wrong aesthetically.
Class 3
The highest standard of IPC-A-610 is Class 3, which means an electronic assembly must be built per all of the IPC criteria. This includes laminate selection, plating thickness, material qualifications, manufacturing processes, and inspection. Typically, Class 3 is aimed at more critical PCB assemblies.
However, achieving that standard may also come at a premium. It might be necessary to slow down the surface-mount machines to ensure the desired placement accuracy, which will mean a longer build time and additional cost. It may also be necessary to make allowance for higher degrees of scrap in cases where materials can’t be reworked or to allow time for extra inspection or additional cleaning.
Working With Your EMS partner
Many would argue that a reliable EMS provider will always aim to manufacture the products they build to the Class 3 standard, regardless. Any EMS provider that is genuinely serious about compliance is also undoubtedly going to have well-established internal training programs to promote awareness within their manufacturing facility. Also, this compliance is likely to extend not just to the inspection of the end products but also to monitoring every process of the build. The best way to achieve this and maintain the standards required will be for them to appoint in-house IPC trainers who will be externally re-certified.
In the majority of cases, the IPC-A-610 standard will suffice, but there may be situations where an OEM prefers to produce their own criteria to either enhance or replace the existing standard. If you do choose to create your own set of guidelines, then it will be important to ensure that your EMS partner is crystal clear about your expectations from the outset. Thus, you should reference your specific criteria on every request for quotation (RFQ) or purchase order that you submit.
Neil Sharp is the director of marketing for JJS Manufacturing.
Testimonial
"In a year when every marketing dollar mattered, I chose to keep I-Connect007 in our 2025 plan. Their commitment to high-quality, insightful content aligns with Koh Young’s values and helps readers navigate a changing industry. "
Brent Fischthal - Koh YoungSuggested Items
MacDermid Alpha Electronics Solutions Unveils Unified Global Website to Deepen Customer, Talent, and Stakeholder Engagement
07/31/2025 | MacDermid Alpha Electronics SolutionsMacDermid Alpha Electronics Solutions, the electronics business of Elements Solutions Inc, today launched macdermidalpha.com - a unified global website built to deepen digital engagement. The launch marks a significant milestone in the business’ ongoing commitment to delivering more meaningful, interactive, and impactful experiences for its customers, talent, and stakeholders worldwide.
KOKI to Showcase Analytical Services and New HF1200 Solder Paste at SMTA Guadalajara 2025
07/31/2025 | KOKIKOKI, a global leader in advanced soldering materials and process optimization services, will exhibit at the SMTA Guadalajara Expo & Tech Forum, taking place September 17 & 18, 2025 at Expo Guadalajara, Salón Jalisco Halls D & E in Guadalajara, Mexico.
Weller Tools Supports Future Talent with Exclusive Donation to SMTA Michigan Student Soldering Competition
07/23/2025 | Weller ToolsWeller Tools, the industry leader in hand soldering solutions, is proud to announce its support of the upcoming SMTA Michigan Expo & Tech Forum by donating a limited-edition 80th Anniversary Black Soldering Set to the event’s student soldering competition.
Koh Young Appoints Tom Hattori as President of Koh Young Japan
07/21/2025 | Koh YoungKoh Young Technology, the global leader in True 3D measurement-based inspection solutions, announced the appointment of Tom Hattori as President of Koh Young Japan (JKY).
Silicon Mountain Contract Services Enhances SMT Capabilities with New HELLER Reflow Oven
07/17/2025 | Silicon Mountain Contract ServicesSilicon Mountain Contract Services, a leading provider of custom electronics manufacturing solutions, is proud to announce a significant upgrade to its SMT production capability with the addition of a HELLER 2043 MK5 10‑zone reflow oven to its Nampa facility.