-
-
News
News Highlights
- Books
Featured Books
- pcb007 Magazine
Latest Issues
Current IssueThe Hole Truth: Via Integrity in an HDI World
From the drilled hole to registration across multiple sequential lamination cycles, to the quality of your copper plating, via reliability in an HDI world is becoming an ever-greater challenge. This month we look at “The Hole Truth,” from creating the “perfect” via to how you can assure via quality and reliability, the first time, every time.
In Pursuit of Perfection: Defect Reduction
For bare PCB board fabrication, defect reduction is a critical aspect of a company's bottom line profitability. In this issue, we examine how imaging, etching, and plating processes can provide information and insight into reducing defects and increasing yields.
Voices of the Industry
We take the pulse of the PCB industry by sharing insights from leading fabricators and suppliers in this month's issue. We've gathered their thoughts on the new U.S. administration, spending, the war in Ukraine, and their most pressing needs. It’s an eye-opening and enlightening look behind the curtain.
- Articles
- Columns
- Links
- Media kit
||| MENU - pcb007 Magazine
Making Materials Succeed: Past, Present, and Future Trends
May 20, 2019 | Nolan Johnson, I-Connect007Estimated reading time: 7 minutes
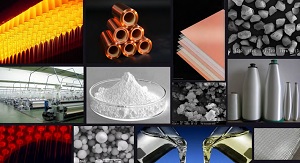
Tony Senese—manager, business development group, Panasonic EMBD—gives Nolan Johnson an overview of materials and components as well as changing business models and methods to make materials succeed and how to stay profitable.
Nolan Johnson: Can you describe the changes you’ve seen in the cost and structure of materials?
Tony Senese: It’s a lot easier for people to talk about cost than it is price because the price is considered to be negotiable. Forget inflation. Everybody wants to talk about all of the technical integration that’s required, but nobody understands the structural changes that we’ve gone through in the last 30–40 years.
I’ll start with a global overview of what materials existed in terms of what people were using, what materials exist now, and the changes. In 1980, about 90% of all materials used to make circuit boards were some form of FR-4. By now, about 60% of materials are some form of FR-4, meaning that the basic constituent is epoxy resin, E-glass fiberglass, and copper. There are differences that we could debate about, but the cost drivers are the same.
The materials that everybody likes to talk about are 40% of everything else. Fabricators, OEMs, and material suppliers like to talk about those because of the value that they offer to each, and they are all different. Laminators have been making low margins for so long that they’ve forgotten what it was like to make FR-4 in 1980, for example. Back then, FR-4 was a very profitable business. Gross margins without overhead were in the neighborhood of 70%.
The three basic materials that we use are resin, glass, and copper and are still the primary cost drivers in the materials business. But the big difference then and now is we were able to leverage those three materials, which were completely commodity materials at the time. All of us that were in the business thought about them as technical materials because we were doing a lot of research on how we made things better.
The most basic two-part epoxy resin, which is the same kind you would buy in a glue today, was almost all of what Panasonic made. It cost about $1 per pound and was available from 10 different resin suppliers in North America as well as 2–3 in Europe where it was being made. In some cases, Asia was just starting to get into the business, but it was such an easy product to make that the first people in the business there made their own. These products were a commodity and very cheap. They are still extremely high-quality adhesives and resins to use in a composite as we do.
Fiberglass has also been around for quite a while. Most of the glass styles that we used in 1980 had been available for industrial use for other products for a while. That glass would sell for $1–2 per square meter, and that price hasn’t changed much today. Further, electroplated copper was only used in our business. The applications that we have today, including batteries, didn’t exist in any volume. Copper price was dictated by the commodity price of copper and the conversion cost, which is electricity and capital. Copper cost about 30 cents per square foot in 1980.
When you added up those three to a 0.059 material, which was still a large part of the business and sold for around $2.50 per square foot with 70% gross margin. But that margin seems like a distant memory. Most people would argue with me about whether or not that was the real gross margin because our net profits were in low, double-digit numbers, but there was a lot of money being spent on many other things. All of these large companies that were in the business at the time were quite profitable. Price negotiations were really a question of your position in the market and supply and demand; it didn’t have as much to do with cost.
Today, overall prices for standard FR-4 material haven’t changed very much. In 40 years of inflation, no matter what you count as inflation, the cost of those materials has decreased by 30–40% in relative dollars. The margins, however, have decreased by at least an order of magnitude to the point where the net profit of making those FR-4 materials is in the low single digits unless you’re making a couple of billion dollars’ worth of that material in a very high volume environment. Many people would say that’s not making money.
Johnson: These margins are down in the grocery store range.
Senese: Yes, if you’re good. And if you’re bad, you’re going to go out of business; it’s one of the drivers for laminators to look for materials that offer other value and try to change it up. That’s driven us into specialization. The raw material suppliers for resin, glass, and copper have changed even more. Epoxy resin for our business in the United States is only available from one supplier, and it’s not inexpensive. In China, Japan, and Taiwan, a lot of the volume of that epoxy resin is made in-house. For them to make a profit, they’ve had to vertically integrate downward to survive; they can make their own resin as cheaply in that volume as anybody can sell it.
The specialty resins that constitute the other 40% are still extremely expensive. Compared to that $1 per pound price, they’re anywhere from 10–20 times more expensive. Copper foil is in the same price range that it was then, and it depends a lot on demand. It’s hard to find new vendors for copper foil. Capacity that was dedicated to electronic circuit boards has gone to battery production. Some dedicated suppliers have gone out of business, and there has been some consolidation. It is a very low-margin business as well; all the copper foil suppliers are competing on the foil that’s going into high-end products because they can eke out a bit more profit there.
The glass business is a similar story to copper. The price of glass hasn’t changed very much. In fact, it has gone down over the years for style-to-style comparisons, which has allowed most of us to keep our per square foot price of FR-4 down. But a lot of the companies, in this business, have chosen to not develop products on the low end because there’s no profit in it. No matter what the glass cost is, it’s unprofitable. And the new innovations in glass cloth are much more expensive. For instance, quartz glass, which is the lowest loss glass fabric you can buy, is over 10 times as much as E-glass; everything else falls somewhere in between.
We have gone from a commodity-based raw materials supply to suppliers that are trying to survive by making specialty materials. Whether the resins are PPO, cyanate ester, polybutadiene, polybenzoxazine, etc., all of those are very low-volume engineering thermosets that have been adopted to our business. In most cases, we’re not the biggest part of their customer base, but we’re still a significant part of those suppliers’ customer base that they can afford to develop new products. That means that we are all using a supply chain that is not set up for huge volumes of inventory and instant access to a never-ending flow of material. This has created a very crowded space at the top of that technology pyramid.
This is one of the things that drives the fact that we need to know the end users and their customers as well as the markets that drive change. Are they telling us the true story? And not because our customers and their customers are lying to us, but because these things are all projected based on assumptions that sometimes are true but sometimes not. When you go to a glass supplier, the question is, “We love your E-glass and use it for our FR-4. It’s perfect, and we can count on it. We also like the low Dk glass that you developed 10–15 years ago. We started using it about two years ago, but we need something a little better. What can you do for us?”
These people trying to report to their boss what they’re going to do look at you like you’re from another planet because they don’t even want to ask the question, “How much are you going to buy and when?” They know we don’t have a good answer (laughs). It’s a waste of time to ask us that question. They go straight to the end users now. Laminators are talking to end users, but so are raw material suppliers because they’re trying to get a handle on how much time they have to do this, and when they get it to the market, when are you going to buy some. Our challenge is driven by cost and the supply chain. We are no longer in a commodity zone. Everyone in the supply chain, because of what has happened in terms of transferring to lower cost areas of the world, is hugely risk-averse. They are looking for the next thing that’s going to disrupt the status quo.
To read the full article, which appeared in the May 2019 issue of PCB007 Magazine, click here.
Suggested Items
The Evolution of Picosecond Laser Drilling
06/19/2025 | Marcy LaRont, PCB007 MagazineIs it hard to imagine a single laser pulse reduced not only from nanoseconds to picoseconds in its pulse duration, but even to femtoseconds? Well, buckle up because it seems we are there. In this interview, Dr. Stefan Rung, technical director of laser machines at Schmoll Maschinen GmbH, traces the technology trajectory of the laser drill from the CO2 laser to cutting-edge picosecond and hybrid laser drilling systems, highlighting the benefits and limitations of each method, and demonstrating how laser innovations are shaping the future of PCB fabrication.
Day 2: More Cutting-edge Insights at the EIPC Summer Conference
06/18/2025 | Pete Starkey, I-Connect007The European Institute for the PCB Community (EIPC) summer conference took place this year in Edinburgh, Scotland, June 3-4. This is the third of three articles on the conference. The other two cover Day 1’s sessions and the opening keynote speech. Below is a recap of the second day’s sessions.
Day 1: Cutting Edge Insights at the EIPC Summer Conference
06/17/2025 | Pete Starkey, I-Connect007The European Institute for the PCB Community (EIPC) Summer Conference took place this year in Edinburgh, Scotland, June 3-4. This is the second of three articles on the conference. The other two cover the keynote speeches and Day 2 of the technical conference. Below is a recap of the first day’s sessions.
Preventing Surface Prep Defects and Ensuring Reliability
06/10/2025 | Marcy LaRont, PCB007 MagazineIn printed circuit board (PCB) fabrication, surface preparation is a critical process that ensures strong adhesion, reliable plating, and long-term product performance. Without proper surface treatment, manufacturers may encounter defects such as delamination, poor solder mask adhesion, and plating failures. This article examines key surface preparation techniques, common defects resulting from improper processes, and real-world case studies that illustrate best practices.
RF PCB Design Tips and Tricks
05/08/2025 | Cherie Litson, EPTAC MIT CID/CID+There are many great books, videos, and information online about designing PCBs for RF circuits. A few of my favorite RF sources are Hans Rosenberg, Stephen Chavez, and Rick Hartley, but there are many more. These PCB design engineers have a very good perspective on what it takes to take an RF design from schematic concept to PCB layout.