-
- News
- Books
Featured Books
- smt007 Magazine
Latest Issues
Current IssueMoving Forward With Confidence
In this issue, we focus on sales and quoting, workforce training, new IPC leadership in the U.S. and Canada, the effects of tariffs, CFX standards, and much more—all designed to provide perspective as you move through the cloud bank of today's shifting economic market.
Intelligent Test and Inspection
Are you ready to explore the cutting-edge advancements shaping the electronics manufacturing industry? The May 2025 issue of SMT007 Magazine is packed with insights, innovations, and expert perspectives that you won’t want to miss.
Do You Have X-ray Vision?
Has X-ray’s time finally come in electronics manufacturing? Join us in this issue of SMT007 Magazine, where we answer this question and others to bring more efficiency to your bottom line.
- Articles
- Columns
- Links
- Media kit
||| MENU - smt007 Magazine
Smart Factory Transitions Are Attainable—With a Plan
June 4, 2019 | Nolan Johnson, I-Connect007Estimated reading time: 3 minutes
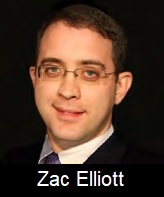
In his white paper A Generalized Approach Can Help All Manufacturers Move to Smart Factories, Zac Elliott, technical marketing engineer at Mentor, a Siemens company, outlines a structured organization for smart factory implementation. While there can be one set of challenges to overcome when building a smart factory on a greenfield site, firms restricted to pre-existing facilities face a different set of hurdles.
I-Connect007 Managing Editor Nolan Johnson caught up with Elliott to get his thoughts on how things have proceeded since the paper was published, and to talk strategies for smaller firms and brownfield companies.
Nolan Johnson: Zac, there are a lot of shops still using mostly manual processes, and facing a potential transition to becoming an Industry 4.0 facility? The first question is: are they too late to even participate?
Zac Elliott: It is not too late to participate in the smart factory transformation, but it is due time to start developing a strategy for your business. As discussed in the white paper, trends in the electronics industry are accelerating the pace of change for manufacturers. As businesses are pushed to evolve, there are many opportunities to implement smart factory operational improvements. Having a sound strategy means embracing the change and moving the business further, faster.
Johnson: That’s good news for our colleagues, I’m sure. How do they get started on such a process? If a company has to wait until they’ve changed everything to get the pieces to provide a return, that’s a daunting prospect. What’s the best strategy? What do they do first? Do they concentrate on the equipment on the floor? The ERP? Something else?
Elliott: The best strategy will go after quick wins in order to gain traction and realized returns early in the overall smart factory evolution. While most businesses in the industry have similar challenges, every factory is unique in terms of expertise, equipment, existing capabilities, and so on. A proven methodology is to use lean manufacturing tools like value steam mapping to identify waste in business and manufacturing processes and then to define the improved future state.
Once the future state is identified, a plan should be developed which prioritizes implementation phases based on the ROI of the various improvements. In the beginning, look at one-, three-, and five-year windows and focus on building a foundation which will consistently show a return along the way. Finally, adapt the plan over time as progress is made, technology improves, and challenges change.
As an example, consider the implementation of a manufacturing execution system on the shop floor. A phased approach could first address electronic work instructions as step towards a paperless factory. In this initial phase, some initial investment will be made in engineering effort, computer hardware, and implementation, but there is an immediate return realized by removing wasteful paper documentation. A next phase could be electronic data collection. Now, this added functionality is only an incremental improvement and investment that builds on what was implemented in the initial phase. Finally, machine data collection and process control may be implemented to complete the MES implementation. With this approach, each phase builds upon the previous with additional value and return.
Johnson: You wrote this white paper in 2018. A year or so on, how do you see the smaller shops plugging into your three-tiered factory infrastructure? For example, if I’m a single-facility shop, do I need enterprise-level apps? And how does that look different than a multilocation company?
Elliott: Do not get hung up on the top tier being “enterprise only.” The top tier is simply where high-level business requirements are managed. Without the corporate overhead, smaller shops are actually enabled to adapt and change more quickly than their enterprise counterparts. Although technology budgets may not be as large, smaller companies can eschew costly enterprise-grade solutions, which are usually more generalized, in lieu of purpose-built solutions streamlined for the electronics industry.
Specialized solutions can offer SMB manufacturers a streamlined implementation, focus on their industry, and ultimately more return sooner. Best in breed solutions available today offer a mix both of flexibility for good coverage of business processes and specialization to simplify implementation.
To read the full article, which appears in the June 2019 issue of SMT007 Magazine, click here.
Suggested Items
I-Connect007 Editor’s Choice: Five Must-Reads for the Week
06/27/2025 | Nolan Johnson, I-Connect007While news outside our industry keeps our attention occupied, the big news inside the industry is the rechristening of IPC as the Global Electronics Association. My must-reads begins with Marcy LaRont’s exclusive and informative interview with Dr. John Mitchell, president and CEO of the Global Electronics Association. For designers, have we finally reached the point in time where autorouters will fulfill their potential?
Reflections and Priorities: An Update to I-Connect007 Readers
06/24/2025 | Marcy LaRont, I-Connect007The electronics and manufacturing industry is evolving rapidly—with new technologies, deeper global connections, and a growing drive toward sustainability. To reflect these changes and our place in this dynamic space, we’re refreshing our brand.
The Knowledge Base: Building the Workforce of Tomorrow With EMAC
06/24/2025 | Mike Konrad -- Column: The Knowledge BaseAs the electronics manufacturing industry races to meet rising global demand and technological complexity, the need for a highly skilled, future-ready workforce has never been greater. At the forefront of addressing this challenge is The Electronics Manufacturing & Assembly Collaborative (EMAC)—a national initiative dedicated to strengthening the talent pipeline through strategic collaboration with SMTA, education, and government stakeholders.
IPC Rebrands as Global Electronics Association: Interview With Dr. John W. Mitchell
06/22/2025 | Marcy LaRont, I-Connect007Today, following a major announcement, IPC is embracing the rapid advancement of technology with a bold decision to change its name to the Global Electronics Association. This name more accurately reflects the full breadth of its work and the modern realities of electronics manufacturing. In this exclusive interview, Global Electronics Association President and CEO Dr. John W. Mitchell shares the story behind the rebrand: Why now, what it means for the industry, and how it aligns with the organization’s mission.
Global Electronics Association Debuts; New Name Elevates IPC’s 70-Year Legacy as Voice of $6 Trillion Electronics Industry
06/25/2025 | Global Electronics AssociationToday begins a new chapter for IPC as it officially becomes the Global Electronics Association, reflecting its role as the voice of the electronics industry. Guided by the vision of “Better electronics for a better world,” the Global Electronics Association (electronics.org) is dedicated to enhancing supply chain resilience and promoting accelerated growth through engagement with more than 3,000 member companies, thousands of partners, and dozens of governments across the globe.