-
- News
- Books
Featured Books
- smt007 Magazine
Latest Issues
Current IssueMoving Forward With Confidence
In this issue, we focus on sales and quoting, workforce training, new IPC leadership in the U.S. and Canada, the effects of tariffs, CFX standards, and much more—all designed to provide perspective as you move through the cloud bank of today's shifting economic market.
Intelligent Test and Inspection
Are you ready to explore the cutting-edge advancements shaping the electronics manufacturing industry? The May 2025 issue of SMT007 Magazine is packed with insights, innovations, and expert perspectives that you won’t want to miss.
Do You Have X-ray Vision?
Has X-ray’s time finally come in electronics manufacturing? Join us in this issue of SMT007 Magazine, where we answer this question and others to bring more efficiency to your bottom line.
- Articles
- Columns
- Links
- Media kit
||| MENU - smt007 Magazine
Low-Temperature SMT Solder Evaluation
July 5, 2019 | H. Osgood, D. Geiger, R. Pennings, C. Biederman, J. Jiang, and J. Bernal, Flex Inc.Estimated reading time: 5 minutes
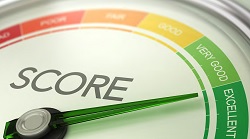
Abstract
The electronics industry could benefit greatly from using a reliable, manufacturable, reduced-temperature, SMT solder material (alloy composition), which is cost competitive with traditional Sn3Ag0.5Cu (SAC305) solder. The many possible advantages and some disadvantages or challenges are discussed. Until recently, the use of Sn/Bi-based materials has been investigated with negative consequences for high strain rate (drop-shock) applications; thus, these alloys have been avoided. Recent advances in alloy “doping” have opened the door to revisit Sn/Bi alloys as a possible alternative to SAC-305 for many applications.
We tested the manufacturability and reliability of three low-temperature and one SAC-305 (used as a control) solder paste materials. Two of these materials are doped Sn/Bi/Ag, and one is just Sn/Bi/Ag1%. We will discuss the tests and related results. Lastly, we will discuss the prospects, applications, and possible implications (based on this evaluation) of these materials together with future actions.
Introduction
A typical SAC305 (Sn3Ag0.5Cu) reflow profile will have peak temperatures in the range of 235–245°C. Tin/bismuth or tin/bismuth/silver solder alloys may use a peak temperature in the range of 165–195°C. This represents a peak temperature delta of more than 50°C. Aside from the obvious energy cost savings, there are many other benefits to using a low-temperature solder (LTS) material, and they will be discussed later in this article. We also discuss some of the known and unknown risks as well.
Tin/bismuth and tin/bismuth/silver alloys are well-known to the industry and have been used routinely in consumer products that are not likely to be subjected to shock, drop, vibration, or high temperatures, such as TVs and some appliances. These alloys are more brittle than SAC-305 and more creep resistant. This makes them well-suited for low strain rate stresses (temperature changes) but not well-suited for high strain rate stresses (shock, drop, vibration, bend, etc.).
Some solder material suppliers have been working for several years to develop a version of this (low-temperature) alloy, which is comparable to SAC-305 in terms of higher strain rate reliability.
Historically, they had come close, but only recently have they hit the mark using “secret” recipes that include trace amounts of “dopant” materials to make the alloy more ductile and crack resistant. Other papers [1 & 2] discuss the dopant effects on lattice and grain structures by adding trace amounts of elements, such as copper, nickel, manganese, and antimony. We will not go into that detail here, but the main point is that some suppliers seem to have found an appropriate recipe that maintains the bulk alloy (and hence low melting point) but alters its properties in a sufficiently beneficial way.
Another key factor in our consideration was that there had to be more than just one supplier of these types of materials before we performed any serious evaluations. We tended to avoid embracing proprietary processes or materials, which are only available from a single source.
Advantages
Some of the possible advantages of LTS include:
• Reduced board and component warp
• Reduced head-in-pillow
• Lower residual stress
• Reduced pad cratering
• Reduced CTE geometrical effects (scale factor)
– Allows for smaller land pads/footprints
• Less expensive materials
– PCBs
– Components
• Less thermal exposure
– Thermally sensitive components
– Semiconductors
• Lower energy and maintenance costs
– Estimated 20–25% lower energy cost depending on the profile
– Lower maintenance cost on oven moving parts
• Possible hybrid assembly
– SAC-305 on one side and low temp on the other
• Reduced voiding
– ~50% void reductions observed
Disadvantages
As with any new material, there are unknown risks that may not come to light until the material is in use for some time. Some of the known risks include:
• Package warp—hot tearing
– Large BGA packages that were previously designed to flatten out at over 210°C can cause “hot tearing” in the solder joint because the package never completely flattens and remains warped throughout the reflow cycle. One remedy for this is to use more solder paste to make up for the gap difference. The lower-temperature alloys did not tend to wet as aggressively (discussed in more detail later) and therefore can allow more solder per unit area without bridging. If the industry moves towards accepting these alloys on a large scale, it is likely the packaging vendors will adjust accordingly and may offer “LTS” versions of these packages
• Rework
– Solder wire: Very limited (only one known source and it is not commercially available yet) and it is brittle
– Cracked solder pots: Bismuth expands when it cools, so it can cause some solder pots (wave solder) to crack
• Wide liquidus/solidus range
– We observed that a very rapid cooling was necessary to guarantee that the assembly was below 138°C exiting the conveyor reflow oven
• Flux residue
– We observed a considerable amount of flux residue after reflow. In time, these solder pastes may evolve to improve this
• More slump and less wetting
– Our tests indicate a bit more slump (hot and cold) than our controlled material, but again, this is more likely to do with the maturity of the paste. However, the alloy itself does not wet as aggressively as SAC-305, which can be an issue in certain circumstances, although we still found it to be acceptable. In some cases, less wetting can be an advantage as well, such as for paste in hole
Experimental and Results
Materials Tested
Figure 1 shows the materials tested.
Figure 1: Materials tested.
Material A is the control material. Materials B and D are the “doped” alloys, and Material C has no dopants added.
Assembly Conditions
All test boards were baked, inspected, and labeled before solder screen print. Solder paste inspection (SPI) was performed as well as SMT assembly and reflow.
Reflow Profile for LTS
Although peak temperatures as low as 165°C can be used (and should be used when appropriate), a higher temperature of 190°C was used to drive mixing on the SAC-305 BGAs. The solder paste and BGA ball interface experiences a sufficient phase change at these temperatures to drive diffusion and hence mixing of the BGA ball with the solder paste.
Mixing of the BGA with the SnBi paste was approximately 50%. This is comparable to Time 0 as well as a characteristic of all the solder joints we observed, which fell into the 40–60% mixing range.
To read the full article, which appeared in the July 2019 issue of SMT007, click here.
Suggested Items
Hands-On Demos Now Available for Apollo Seiko’s EF and AF Selective Soldering Lines
06/30/2025 | Apollo SeikoApollo Seiko, a leading innovator in soldering technology, is excited to spotlight its expanded lineup of EF and AF Series Selective Soldering Systems, now available for live demonstrations in its newly dedicated demo room.
Indium Corporation Expert to Present on Automotive and Industrial Solder Bonding Solutions at Global Electronics Association Workshop
06/26/2025 | IndiumIndium Corporation Principal Engineer, Advanced Materials, Andy Mackie, Ph.D., MSc, will deliver a technical presentation on innovative solder bonding solutions for automotive and industrial applications at the Global Electronics A
Fresh PCB Concepts: Assembly Challenges with Micro Components and Standard Solder Mask Practices
06/26/2025 | Team NCAB -- Column: Fresh PCB ConceptsMicro components have redefined what is possible in PCB design. With package sizes like 01005 and 0201 becoming more common in high-density layouts, designers are now expected to pack more performance into smaller spaces than ever before. While these advancements support miniaturization and functionality, they introduce new assembly challenges, particularly with traditional solder mask and legend application processes.
Knocking Down the Bone Pile: Tin Whisker Mitigation in Aerospace Applications, Part 3
06/25/2025 | Nash Bell -- Column: Knocking Down the Bone PileTin whiskers are slender, hair-like metallic growths that can develop on the surface of tin-plated electronic components. Typically measuring a few micrometers in diameter and growing several millimeters in length, they form through an electrochemical process influenced by environmental factors such as temperature variations, mechanical or compressive stress, and the aging of solder alloys.
SolderKing’s Successful Approach to Modern Soldering Needs
06/18/2025 | Nolan Johnson, I-Connect007Chris Ward, co-founder of the family-owned SolderKing, discusses his company's rapid growth and recent recognition with the King’s Award for Enterprise. Chris shares how SolderKing has achieved these award-winning levels of service in such a short timeframe. Their secret? Being flexible in a changing market, technical prowess, and strong customer support.