-
- News
- Books
Featured Books
- smt007 Magazine
Latest Issues
Current IssueMoving Forward With Confidence
In this issue, we focus on sales and quoting, workforce training, new IPC leadership in the U.S. and Canada, the effects of tariffs, CFX standards, and much more—all designed to provide perspective as you move through the cloud bank of today's shifting economic market.
Intelligent Test and Inspection
Are you ready to explore the cutting-edge advancements shaping the electronics manufacturing industry? The May 2025 issue of SMT007 Magazine is packed with insights, innovations, and expert perspectives that you won’t want to miss.
Do You Have X-ray Vision?
Has X-ray’s time finally come in electronics manufacturing? Join us in this issue of SMT007 Magazine, where we answer this question and others to bring more efficiency to your bottom line.
- Articles
- Columns
- Links
- Media kit
||| MENU - smt007 Magazine
Surface Treatment Enabling Low-Temperature Soldering to Aluminum
July 15, 2019 | Divyakant Kadiwala, Averatek CorporationEstimated reading time: 4 minutes
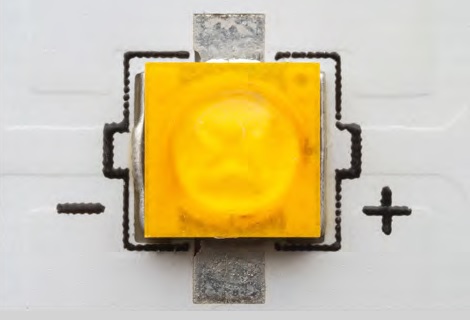
Abstract
The majority of flexible circuits are made by patterning copper metal that is laminated to a flexible substrate, which is usually polyimide film of varying thicknesses. An increasingly popular method to meet the need for lower cost circuitry is the use of aluminium on polyester (Al-PET) substrates. This material is gaining popularity and has found wide use in RFID tags, low-cost LED lighting, and other single-layer circuits. However, both aluminium and PET have their own constraints and require special processing to make finished circuits. Aluminum is not easy to solder components to at low temperatures, and PET cannot withstand high temperatures. Soldering to these materials requires either an additional surface treatment or the use of conductive epoxy to attach components. Surface treatment of aluminum includes the likes of electroless nickel immersion gold plating (ENIG), which is extensive wet chemistry and cost-prohibitive for mass adoption.
Conductive adhesives, including anisotropic conductive paste (ACP), are another alternative to soldering components. These result in component-substrate interfaces that are inferior to conventional solders in terms of performance and reliability. An advanced surface treatment technology will be presented that addresses all these constraints. Once applied on aluminum surfaces using conventional printing techniques such as screen, stencil, etc., it is thermally cured in a convection oven at low temperatures. This surface treatment is non-conductive. To attach a component, a solder bump on the component or solder printed on the treated pad is needed before placing the component. The aluminum circuit will pass through a reflow oven, as is commonly done in PCB assembly. This allows for the formation of a true metal-to-metal bond between the solder and the aluminum on the pads. This process paves the way for large-scale, low-cost manufacturing of Al-PET circuits.
Introduction
Aluminum is the most abundant metal in the earth’s crust. Its alloys have found wide use as a building material in the construction of automobiles, aircraft, bicycles, building frames, etc. Other uses range from electrical connectors, packaging cans and foils, and household utensils. While it is a material of choice in the above fields, it is second to copper in the field of flexible circuits.
This is despite the various advantages that aluminum has over copper. Aluminum is more than three times lighter than copper. The density of aluminum is 2.7 gm/cm3 while that of copper is 8.92 gm/cm3. Its electrical resistivity is 26.5 nΩ·m (at 20°C) while that of copper is 16.78 nΩ·m (at 20°C). Also, its thermal conductivity is 237 W/(m·K) while that of copper is 401 W/(m·K).
Although it is not as good an electrical and thermal conductor as copper, it can radiate heat better than copper due to its lower density. Overall, aluminum has 68% of the conductivity of copper but has only 30% of the weight of copper. This means that a bare wire of aluminum weighs half as much as a bare wire of copper that has the same electrical resistance. This will be similar for aluminium traces in the case of flexible circuits.
Also, aluminum is generally less expensive when compared to copper conductors. A recent check indicated the price of aluminium was 35% less than that of copper. It is three times less expensive than copper on an equal weight basis and six times less expensive on an actual usage basis. This is the biggest advantage that aluminum has over copper. Table 1 lists the comparative properties of the two metals relevant to flexible circuits.
Flexible Circuits and Al-PET Substrates
The majority of flexible circuits are made using copper on polyimide (Cu-PI) substrates. These consist of copper foil laminated onto polyimide film. Varying the thickness of copper and polyimide gives rise to various combinations of thicknesses of Cu-PI to suit the conductivity and dielectric requirements of the end applications. Traces are formed using photolithography followed by a print-and-etch process. Components are soldered on to make the finished circuits. A reasonable selection of solders is available that can easily bond to copper traces without the need for any special surface treatment.
Table 1: Properties of aluminum and copper.
An increasingly popular method to make flexible circuits is by using aluminum on PET (polyethylene terephthalate) or Al-PET substrates. These are available in varying thickness of aluminum foil laminated onto PET film (Figure 1).
While aluminum is less expensive than copper, PET is also significantly cheaper than polyimide film. Hence, lower material cost is a major driver for the increasing use of Al- PET substrates, but their use has been limited because of processing challenges.
Figure 1: Typical laminated construction of Al-PET substrates.
The process to generate the traces on aluminium substrates is similar to that of copper. A dry-film or liquid resist is used for photolithography, which is then followed by chemical print-and-etch to form aluminum traces. But attaching the components onto aluminium is a challenge. Unlike copper, it is not easy to solder to aluminum. Soldering to aluminum is difficult because of the presence of a thin layer of aluminum oxide. This layer forms naturally when the bare metal is exposed to air. Since most flexible circuit manufacturing is done under atmospheric conditions, all aluminum surfaces will have an oxide layer. While the formation of this natural oxide is self-limiting, its presence cannot be overcome by the flux used in existing solder pastes. If harsher fluxes are used within solder pastes to address the aluminum oxide problem, they will cause corrosion of the very thin aluminum layers and thus reliability problems.
There are two methods currently used to attach components to Al-PET substrates: one is the zincate and plating process while the second is using conductive epoxy.
To read the full article, which appeared in the July 2019 issue of SMT007 Magazine, click here.
Suggested Items
Hands-On Demos Now Available for Apollo Seiko’s EF and AF Selective Soldering Lines
06/30/2025 | Apollo SeikoApollo Seiko, a leading innovator in soldering technology, is excited to spotlight its expanded lineup of EF and AF Series Selective Soldering Systems, now available for live demonstrations in its newly dedicated demo room.
Indium Corporation Expert to Present on Automotive and Industrial Solder Bonding Solutions at Global Electronics Association Workshop
06/26/2025 | IndiumIndium Corporation Principal Engineer, Advanced Materials, Andy Mackie, Ph.D., MSc, will deliver a technical presentation on innovative solder bonding solutions for automotive and industrial applications at the Global Electronics A
Fresh PCB Concepts: Assembly Challenges with Micro Components and Standard Solder Mask Practices
06/26/2025 | Team NCAB -- Column: Fresh PCB ConceptsMicro components have redefined what is possible in PCB design. With package sizes like 01005 and 0201 becoming more common in high-density layouts, designers are now expected to pack more performance into smaller spaces than ever before. While these advancements support miniaturization and functionality, they introduce new assembly challenges, particularly with traditional solder mask and legend application processes.
Knocking Down the Bone Pile: Tin Whisker Mitigation in Aerospace Applications, Part 3
06/25/2025 | Nash Bell -- Column: Knocking Down the Bone PileTin whiskers are slender, hair-like metallic growths that can develop on the surface of tin-plated electronic components. Typically measuring a few micrometers in diameter and growing several millimeters in length, they form through an electrochemical process influenced by environmental factors such as temperature variations, mechanical or compressive stress, and the aging of solder alloys.
SolderKing’s Successful Approach to Modern Soldering Needs
06/18/2025 | Nolan Johnson, I-Connect007Chris Ward, co-founder of the family-owned SolderKing, discusses his company's rapid growth and recent recognition with the King’s Award for Enterprise. Chris shares how SolderKing has achieved these award-winning levels of service in such a short timeframe. Their secret? Being flexible in a changing market, technical prowess, and strong customer support.