-
- News
- Books
Featured Books
- pcb007 Magazine
Latest Issues
Current IssueVoices of the Industry
We take the pulse of the PCB industry by sharing insights from leading fabricators and suppliers in this month's issue. We've gathered their thoughts on the new U.S. administration, spending, the war in Ukraine, and their most pressing needs. It’s an eye-opening and enlightening look behind the curtain.
The Essential Guide to Surface Finishes
We go back to basics this month with a recount of a little history, and look forward to addressing the many challenges that high density, high frequency, adhesion, SI, and corrosion concerns for harsh environments bring to the fore. We compare and contrast surface finishes by type and application, take a hard look at the many iterations of gold plating, and address palladium as a surface finish.
It's Show Time!
In this month’s issue of PCB007 Magazine we reimagine the possibilities featuring stories all about IPC APEX EXPO 2025—covering what to look forward to, and what you don’t want to miss.
- Articles
- Columns
Search Console
- Links
- Media kit
||| MENU - pcb007 Magazine
Nano Dimension CEO Gives Company Update
July 19, 2019 | Nolan Johnson and Dan Feinberg, I-Connect007Estimated reading time: 16 minutes
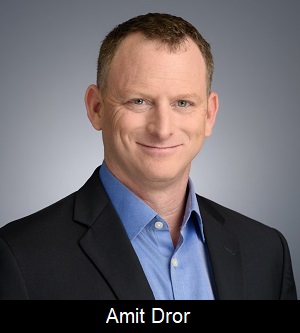
Dan Feinberg and Nolan Johnson speak with Amit Dror, CEO of Nano Dimension, about recent company events and the company’s focus on high-mix/low-volume and agile local manufacturing.
Nolan Johnson: Amit, Nano Dimension has been quite busy recently. Can you start by sharing a review of the news that you’ve been posting in the last 90 days and what general trends you see at Nano Dimension moving forward?
Amit Dror: As you know, we’ve been working hard to come up with a product that brings this disruptive technology to the market, and it took us a few years. Over the last year and a half since we launched the DragonFly printer to the market, we received a lot of feedback. Much of our news is related to the adoption of different silos or segments within the market of electronics. Other news is on our success to penetrate new and different geographical areas, including sales in the U.S. and Japan.
Another trend we’ve presented is how Nano Dimension—in some cases, together with our partners and customers—comes up with new types of applications. Looking at the early days, it was more about PCB prototyping. But as we continue to evolve, we are getting more and more use cases, which we considered as different technologies or unique applications that can be achieved with 3D printing for electronics.
Presenting side mounts on PCB in an easy implementation for our unique technology as well as 3D-printed RF antennas and capacitors. It was nice to see our customer in Japan, which has been the capital of electronics for many years, sharing his 3D-printed applications in Tokyo. It says a lot about the level we’ve reached and the readiness and the willingness of customers to adopt this new type of technology.
Dan Feinberg: Looking at the units that you’ve sold, have any companies bought a second unit yet?
Dror: Yes. TTM Technologies already bought three units. That came after they participated in a pilot stage two years ago with a preliminary Beta system. Today, they have three DragonFly Pro systems.
Feinberg: That’s important because that means it’s part of their production now and what they do every day. When they only have one unit, they could be trying it, but we don’t know how much they’re using it. But when they get another, you know they have justified its use.
One reason I asked that is because I receive hundreds requests from circuit board manufacturers China every day on my LinkedIn account. They always ask if I recommend anyone who needs or makes circuit boards. Then, I ask, “Are you capable of making 3D-printed circuits? And if so, which kind of printer do you use?” I’m not telling them if I’m interested in buying circuits or anything else, but they usually respond, “We can make prototypes quickly, even in half a day, and we don’t need the 3D printer.” I write back, “That’s the only thing I’m interested in, but for more reasons than speed.”
I’ve had a few lately that have said that they are now interested in and are looking at 3D printing. To me, it’s not just a way of making prototypes; it’s a way to make something totally different that you can’t do with standard processes, which is why I ask.
Also, how are your consumable sales doing? That’s a good indication of whether the technology is starting to take off.
Dror: Without getting into numbers, which we share on a quarterly basis since we are a public company, it’s growing from one quarter to the other because the installed base of machines is growing. We’re selling machines, and there were some customers that acquired more than one system. The usage by most of our customers is one of two types: PCB prototyping, in which it depends on how close that customer is to a PCB factory in a way, or how fast could they interact with the factory, which you probably know is also a combination of the complexity the boards are creating. The more complex the board is, the longer it normally takes, and the more expensive it is to prototype it. That would be one usage of the DragonFly system.
Another usage is the one that you commented about, which is making new types of applications that are more difficult, and in some cases, almost impossible to manufacture by traditional means. Sometimes, they don’t even have to be that complex and are still difficult to manufacture. I’ll give you a few examples. Multilayer PCBs are something that traditional manufacturing can make easily. If I want to add an antenna to that PCB, you could manufacture an antenna and assemble it out on top of the PCB or 3D print it all at once with the PCB as part of the 3D print. If you also wanted to add a partial 3D form that could have a battery somewhat embedded, in 3D printing, you could create the battery placeholder as a part of the print and have the antenna and PCB with the battery. Now, we’re starting to move forward toward something more complex. And I just used elements that you could make in a traditional way. However, combining them within the same print increases the complexity significantly. High complexity is a big advantage for 3D printing over traditional manufacturing. None of the things I mentioned are big issues for 3D printing technology.
Feinberg: It increases the complexity, but it reduces the size. It also makes it part of the device itself instead of an add-on component.
Dror: Exactly. That’s another key strength when talking about a premium application, like the one we developed together with Harris Corporation. We’ve been funded now for the second time by Space Florida for an innovative 3D-printed RF amplifier that is designed by Harris and is targeted for nanosatellites. Harris found a way to use Nano Dimension’s technology and materials to reduce the size and weight of RF amplifiers in a way that is worth potentially hundreds of thousands of dollars per satellite. Satellites are expensive, and if we’re talking about nanosatellites, then weight and size are measured in an even smaller scale. Thus, being able to utilize our flexibility in design to reduce the size and weight makes a big difference. By the end of the day, the real cost in 3D is the cost of materials, which is significantly lower in this case compared with the cost of setup and work by traditional manufacturing for such complex devices.
I use that as an example of a premium type of application that can be achieved with 3D-printed electronics. Also, with consumer products, you can get to lower costs when the complexity is high, and the number of units you need to manufacture is not that high; for example, an IoT device for medical devices that combines a few elements and is small in dimensions. Imagine a small, round, cup-like device with an eight-millimeter diameter and three millimeters in height. It has a coil wrapped around it, which is 3D printed, and in the center, you could fit in a very small battery. In the bottom of it, you have the flats conductive area that serves as an antenna for the device. If you were able to follow my description, I created a small device that has a certain shape. When 3D printed, you don’t need a mold to create it. Instead of a PCB, it simply has the conductive coil. For a medical device that might need to be manufactured in the thousands per year, you save a lot cost. With the purchasing, integrating, and testing of such a device, the overhead itself could cost you a lot of money, which can be saved when you 3D print it.
Page 1 of 4
Suggested Items
Intervala Hosts Employee Car and Motorcycle Show, Benefit Nonprofits
08/27/2024 | IntervalaIntervala hosted an employee car and motorcycle show, aptly named the Vala-Cruise and it was a roaring success! Employees had the chance to show off their prized wheels, and it was incredible to see the variety and passion on display.
KIC Honored with IPC Recognition for 25 Years of Membership and Contributions to Electronics Manufacturing Industry
06/24/2024 | KICKIC, a renowned pioneer in thermal process and temperature measurement solutions for electronics manufacturing, is proud to announce that it has been recognized by IPC for 25 years of membership and significant contributions to electronics manufacturing.
Boeing Starliner Spacecraft Completes Successful Crewed Docking with International Space Station
06/07/2024 | BoeingNASA astronauts Barry "Butch" Wilmore and Sunita "Suni" Williams successfully docked Boeing's Starliner spacecraft to the International Space Station (ISS), about 26 hours after launching from Cape Canaveral Space Force Station.
KIC’s Miles Moreau to Present Profiling Basics and Best Practices at SMTA Wisconsin Chapter PCBA Profile Workshop
01/25/2024 | KICKIC, a renowned pioneer in thermal process and temperature measurement solutions for electronics manufacturing, announces that Miles Moreau, General Manager, will be a featured speaker at the SMTA Wisconsin Chapter In-Person PCBA Profile Workshop.
The Drive Toward UHDI and Substrates
09/20/2023 | I-Connect007 Editorial TeamPanasonic’s Darren Hitchcock spoke with the I-Connect007 Editorial Team on the complexities of moving toward ultra HDI manufacturing. As we learn in this conversation, the number of shifting constraints relative to traditional PCB fabrication is quite large and can sometimes conflict with each other.