-
-
News
News Highlights
- Books
Featured Books
- smt007 Magazine
Latest Issues
Current IssueWhat's Your Sweet Spot?
Are you in a niche that’s growing or shrinking? Is it time to reassess and refocus? We spotlight companies thriving by redefining or reinforcing their niche. What are their insights?
Moving Forward With Confidence
In this issue, we focus on sales and quoting, workforce training, new IPC leadership in the U.S. and Canada, the effects of tariffs, CFX standards, and much more—all designed to provide perspective as you move through the cloud bank of today's shifting economic market.
Intelligent Test and Inspection
Are you ready to explore the cutting-edge advancements shaping the electronics manufacturing industry? The May 2025 issue of SMT007 Magazine is packed with insights, innovations, and expert perspectives that you won’t want to miss.
- Articles
- Columns
- Links
- Media kit
||| MENU - smt007 Magazine
How Do I Get Smart With IPC CFX? (Part 1)
July 30, 2019 | Michael Ford, Aegis Software Corp.Estimated reading time: 13 minutes
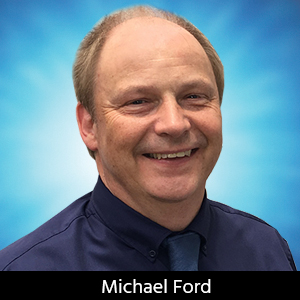
Situational Analysis: 30 Years of Bad Experience
One of the original criticisms during the introduction of automation has been the inevitable loss of visibility and control of the operation. In SMT assembly, we see placement machines working faster than the eye can follow, placing materials that the human eye cannot see unaided, leaving human production operators and management completely dependent on their equipment and the data it produces. This is most unlike a human-driven production process where the operational flow can be continuously refined with Kaizen activities.
By contrast, high-speed machines seem pretty much fixed in the way that they operate, following instructions that they are given. However, this assumption is not true. There are many areas in which the operation of automation is compromised in terms of performance, driven by inefficient programs, poor planning, inadequate material logistics, and incompatibilities in the product design. In the past, Kaizen tools have been somewhat overlooked when dealing with automated assembly processes due to the lack of data and visibility of the machine operation. Though machines in the SMT operation do have interfaces to the outside world, these were created more with the intention of machine diagnostics rather than providing customer-driven MES value, leading to a situation where each machine has its own proprietary interface, and more significantly, proprietary data content.
For a manufacturing organization to make use of machine data, sophisticated software—and in many cases, hardware—is required to extract data and make it meaningful in context with other data gathered from machines of different vendors. Once developed, machine interfaces are liable to change as machine software is updated and enhanced by the vendor (often without consideration for who is using the data), resulting in the sudden unexpected failures of data collection, which can often be hidden for a while until incorrect or inconsistent data is noticed. Therefore, very significant effort has to be put into the support of machine communication to ensure that it works effectively and continuously. With such elevated costs and an otherwise high risk of failure, innovation in the use of data from automated processes has been severely restricted.
Thinking of data derived from manual processes, the issue becomes more severe as the latitude to record data in different ways varies from person to person, even where standard forms are concerned. It is not surprising to hear cases reported where 80% of issues in manufacturing come from 20% of manual operations. Thus, the application of data from across the shop floor is usable with human levels of interpretation, which is certainly not good enough for automated use by ERP or PLN, for example.
Challenge: The Next Generation Is Coming
Today's assembly factories are seeing the biggest challenge to face the industry in a generation, called by many the next industrial revolution. However, in essence, the challenge is a simple extrapolation of trends that have been occurring and increasing in assembly manufacturing for decades. As product lifecycles diminish, competition grows, and technology changes accelerate, and online visibility from customers increases, the potential cost and risk of holding stock of finished goods become an increasing burden on the business.
Depreciation in the value of material stock adds to the traditional costs of warehousing and logistics, especially where products are assembled remotely from their target market. The effect of this on the assembly factory has been to drive the need for flexibility to be more of an in-line process with delivery demand rather than working on a batch basis and relying on the finished goods warehouse to create the impression of flexibility while retaining batch production.
Therefore, losses in assembly manufacturing due to the lack of visibility and management of automated assembly processes is multiplied several-fold. Productivity levels are seen to reduce significantly as product mix increases and batch sizes reduce, even to the level of single-piece production, which is no longer experienced only in exceptional cases. The resultant serious threat to business success is driving the need to look for a new solution to get to another level of understanding and optimization in the operation of automated processes.
As a result, the creation of Industry 4.0 and the drive towards smart factories has been created to provide innovation for the creation of tools that assist and augment key management decisions and engineering projects, and to an increasing extent, perform decision-making automatically. Unfortunately, for this to happen, we also need a related step change in the quality, availability, and value generation ability of data obtained from automated machine processes to make it happen.
Though electronics assembly has been a focal point for machine communication in the assembly industry as a whole, due to the nature of the technology and sheer complexity of the bill of materials, the requirements for digitalization in other areas of assembly manufacturing is also developing. The need has arisen for consistency and completeness throughout the whole of assembly manufacturing, driven by the increasing amount of electromechanical devices and products. Automation in assembly outside of electronics could be thought of as being simpler and lacks historical issues around legacy bespoke interfaces, but it’s an area that is effectively starting from scratch in terms of advanced digital communication and needs to be included.
The Human Element
Factories are not fully automated through the use of assembly machines and robots and are not likely to be in the foreseeable future, as processes requiring humans will continue to be needed. Therefore, the inclusion of human operations is essential as part of the digitalized factory. For example, the digitalized factory could also use augmented reality to enable humans to be a key part of the operation, performing a far wider range of tasks than before with higher value, driven by a continuous feed of expert knowledge enabling participation in many key roles and enhancing their job satisfaction.
Values and Challenges of Digitalization Today
The concept of digitalization and Industry 4.0 offers manufacturers a compelling business solution where flexible factories are managed and optimized, achieving levels of productivity once enjoyed with higher volumes and simple product mix. However, the barrier of visibility and acquisition of data is a significant issue, holding back the majority of factories in the market from making the decision to go forward.
Machine vendors experience a great deal of frustration, as customers approach them to provide an “MES interface” tailored for their needs. Many customers have similar requests but with different defined requirements; thus, the development and support overhead borne by machine vendors has escalated rapidly in recent years. In many cases, requests relate to defined metrics that a particular operation are using because it is easier that way or the specific data points needed to calculate the metrics are not available through the legacy machine interface. The permutations seem infinite. For IT teams within manufacturing—as well as software solution providers that understand the power that direct machine connectivity can bring—there are so many different machine vendor solutions that need to be developed and supported in each factory, no matter what level of co-operation the machine vendors provide, that interfaces again become a very significant overhead.
Page 1 of 3
Suggested Items
Dispense Works RPX Series Robotic Dispensing Machines for Precision Assembly and Custom Automation
07/18/2025 | Dispense Works Inc.Dispense Works Inc., a leader in automated dispensing and precision assembly solutions, offers the RPX Series of robotic dispensing systems.
INSPECTIS AB ‘Makes it a Meal’ with Series U50s Advanced Kit
07/18/2025 | INSPECTIS ABFamous chefs the world over maintain that an entrée doesn’t make a great meal without side dishes. At INSPECTIS, we call those ‘sides’ an Advanced Kit.
Technica USA Introduces Frank Silva as PCBA Representative for Southern CA and Southern NV Territories
07/16/2025 | Technica USATechnica USA is pleased to announce the partnership with veteran Frank Silva as our PCBA Sales Representative, supporting both supply partners and PCBA customers across Southern California and Southern Nevada.
Staying—and Excelling—in Their Lane
07/16/2025 | Nolan Johnson, SMT007 MagazineMichael Seltzer, chief commercial officer at Zentech Manufacturing, helps define his company’s niche and why it has mattered to them over nearly three decades. Should a company shift with the markets or stay true to its mission? Find out how Michael has helped the company truly understand its vision.
Electronics Manufacturing & Assembly Collaborative (EMAC) Announces Innovative Student Competition
07/15/2025 | EMACThe Electronics Manufacturing & Assembly Collaborative (EMAC) recently announced the launch of the Bright Manufacturing Challenge 2025, a revolutionary hands-on competition that transforms how students experience electronics manufacturing and robotics engineering.