-
- News
- Books
Featured Books
- smt007 Magazine
Latest Issues
Current IssueMoving Forward With Confidence
In this issue, we focus on sales and quoting, workforce training, new IPC leadership in the U.S. and Canada, the effects of tariffs, CFX standards, and much more—all designed to provide perspective as you move through the cloud bank of today's shifting economic market.
Intelligent Test and Inspection
Are you ready to explore the cutting-edge advancements shaping the electronics manufacturing industry? The May 2025 issue of SMT007 Magazine is packed with insights, innovations, and expert perspectives that you won’t want to miss.
Do You Have X-ray Vision?
Has X-ray’s time finally come in electronics manufacturing? Join us in this issue of SMT007 Magazine, where we answer this question and others to bring more efficiency to your bottom line.
- Articles
- Columns
- Links
- Media kit
||| MENU - smt007 Magazine
Conformal Coating Processes and Trends
August 27, 2019 | I-Connect007 Editorial TeamEstimated reading time: 4 minutes
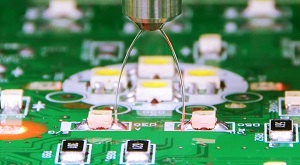
The I-Connect007 editorial team spoke with one of Nordson ASYMTEK's conformal coating experts, Camille Sybert, to discuss where the coating industry is trending and, with the rise of Industry 4.0 and automation, how it is much less about providing the right applicator and more about addressing the entire conformal coating process.
Nolan Johnson: Camille, can you tell us a little bit about yourself?
Camille Sybert: I'm a product marketing engineer, and I’ve been with ASYMTEK for about seven years. I started in applications supporting both our precision dispensing and conformal coating. I ended up focusing on the conformal coating. Now, my responsibilities cover the product management aspects of our conformal coatings product lines as well as addressing our EMI spray solutions.
Johnson: Next, can you give us an overview of conformal coatings and the available technologies for applying them?
Sybert: Conformal coating is generally a process that's put in place because it’s required as opposed to being a nice thing to have. Its function largely serves to increase product yields in the field and the reliability of products, especially in harsh environments. Conformal coatings protect electronics from external factors, such as extreme heat, humidity, moisture, and dust. They also protect from internal factors, such as circuit board corrosion, whisker growth, and shorts within the system.
Overall, they serve as an insulation layer that makes sure that the different components stay focused and dedicated to what it is that they’re doing as opposed to getting in trouble and causing premature failures on boards. As we start to see electronics in a variety of different applications, and as we incorporate some more into things like automobiles, then the need for higher reliability in these electronic products increases significantly.
Johnson: Do standards play a big role in why conformal coating is required rather than it being just "nice to have" for cars, etc.?
Sybert: Your question addresses a number of different items that are coming up as far as what is required in the industry. The world’s increasing dependence on electronics demands that these products need higher levels of performance and capabilities. The industry accepts this and defines what those requirements and standards are. In addition to the ability to put down conformal coating, there’s also the requirement to add degrees of overall process tracking and traceability. Everything that goes into the development of these electronic components is recorded and monitored and can be researched retrospectively if an issue should arise. If there’s a problem with an electronic component that comes up down the line, that can be addressed as well as similar issues. Then, the specific source of the problem can be identified too.
Johnson: That’s an interesting point. The traceability requirement falls to the equipment, doesn’t it?
Sybert: Right, there are many different factors that go into conformal coating, which is only one piece of the entire puzzle that goes together. Currently, people in the industry talk a lot about Industry 4.0 and IoT; much of that stems from data collection and traceability. Many systems involved in the process require closed-loop controls. Now, when we talk about conformal coating, the industry tends to focus on the conformal coating machine. But conformal coating is an entire process itself from board preparation to coating. Then, your coating quality has to be maintained by whatever curing process that you put in your manufacturing line. Inspection is another critical component to verify that your coating processes are within the target.
As we talk about closed-loop controls or the move to more automated operator-less factories, pieces of equipment must be more independent in the sense that they monitor themselves. They correct internally so that you don't require operators to intervene. With automated coating inspection, you can take out a lot of operator subjectivity by setting pass/fail criteria around what you’re inspecting. You verify that you're putting the coating material where you need it to be. You're verifying that it's not where it shouldn’t be and that your final product is within your accepted tolerance. The same is true with ovens and other systems having closed-loop controls to make sure that temperature is being appropriately regulated. You don't want an incomplete cure that may potentially cause other concerns and considerations.
A lot of what's required around these pieces of equipment is that they can collect data and gather information, but also that they're able to share it and take action on that information. Nordson ASYMTEK has been big on process controls for decades. For conformal coating, we came up with laser fan width control to make sure that the coating fan pattern is within tolerance and can make adjustments. Monitoring and controlling flow rate is critically important as well as making sure that fluid temperature remains consistent, so the coating pattern is not affected by the environment; changes in environmental temperature can negatively impact your material viscosity, which would then change how your fluid comes out of the applicator.
To read the full article, which appeared in the August 2019 issue of SMT007 Magazine, click here.
Suggested Items
Intervala Hosts Employee Car and Motorcycle Show, Benefit Nonprofits
08/27/2024 | IntervalaIntervala hosted an employee car and motorcycle show, aptly named the Vala-Cruise and it was a roaring success! Employees had the chance to show off their prized wheels, and it was incredible to see the variety and passion on display.
KIC Honored with IPC Recognition for 25 Years of Membership and Contributions to Electronics Manufacturing Industry
06/24/2024 | KICKIC, a renowned pioneer in thermal process and temperature measurement solutions for electronics manufacturing, is proud to announce that it has been recognized by IPC for 25 years of membership and significant contributions to electronics manufacturing.
Boeing Starliner Spacecraft Completes Successful Crewed Docking with International Space Station
06/07/2024 | BoeingNASA astronauts Barry "Butch" Wilmore and Sunita "Suni" Williams successfully docked Boeing's Starliner spacecraft to the International Space Station (ISS), about 26 hours after launching from Cape Canaveral Space Force Station.
KIC’s Miles Moreau to Present Profiling Basics and Best Practices at SMTA Wisconsin Chapter PCBA Profile Workshop
01/25/2024 | KICKIC, a renowned pioneer in thermal process and temperature measurement solutions for electronics manufacturing, announces that Miles Moreau, General Manager, will be a featured speaker at the SMTA Wisconsin Chapter In-Person PCBA Profile Workshop.
The Drive Toward UHDI and Substrates
09/20/2023 | I-Connect007 Editorial TeamPanasonic’s Darren Hitchcock spoke with the I-Connect007 Editorial Team on the complexities of moving toward ultra HDI manufacturing. As we learn in this conversation, the number of shifting constraints relative to traditional PCB fabrication is quite large and can sometimes conflict with each other.