-
- News
- Books
Featured Books
- pcb007 Magazine
Latest Issues
Current IssueThe Hole Truth: Via Integrity in an HDI World
From the drilled hole to registration across multiple sequential lamination cycles, to the quality of your copper plating, via reliability in an HDI world is becoming an ever-greater challenge. This month we look at “The Hole Truth,” from creating the “perfect” via to how you can assure via quality and reliability, the first time, every time.
In Pursuit of Perfection: Defect Reduction
For bare PCB board fabrication, defect reduction is a critical aspect of a company's bottom line profitability. In this issue, we examine how imaging, etching, and plating processes can provide information and insight into reducing defects and increasing yields.
Voices of the Industry
We take the pulse of the PCB industry by sharing insights from leading fabricators and suppliers in this month's issue. We've gathered their thoughts on the new U.S. administration, spending, the war in Ukraine, and their most pressing needs. It’s an eye-opening and enlightening look behind the curtain.
- Articles
- Columns
- Links
- Media kit
||| MENU - pcb007 Magazine
The Use of Insoluble Anodes in Acid Copper Plating
September 17, 2019 | George Milad, Uyemura International CorporationEstimated reading time: 10 minutes
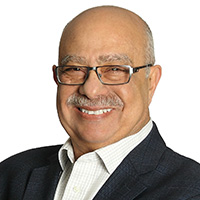
Introduction
Electrolytic acid copper is the process that builds the traces that carry the current throughout a PCB. How to optimize your electrolytic acid copper plating for today’s designs—aspect ratios >20:1 for through-holes and >1:1 aspect ratios for blind via fill—is the challenge. The use of insoluble (mixed metal oxide-coated, or MMO-coated, titanium mesh) produces a consistent and reproducible plated product, is environmentally friendly (eliminates waste), and eliminates anode maintenance, thus increasing the productivity of the plating line.
Vertical acid copper plating remains a very common way for plating PCBs. For best results, the equipment should be optimized with proper rectification and connectivity. The electrolyte and the additives used, along with the plating current density, all play a role in the copper thickness distribution on the plated panel. The anodes have a direct impact on copper thickness distribution. The anode shape, size, and location play a critical role in the thickness distribution of the plated copper in vertical plating of panels in a tank. The vertical plating tank is challenging in its own way, unlike horizontal conveyorized plating where all the panels are exposed to the identical set of anodes, as the part is conveyed through the plating module. In horizontal plating, if the anode setup is not optimum, the thickness distribution within the panel may vary; however, the variation from panel to panel is eliminated.
Soluble Anodes
Soluble anodes need to be filmed for proper dissolution. This is achieved by dummying a fresh copper anode at low current density for 2–3 hours. Once filmed, the film is renewed as the dissolution proceeds. As a byproduct of anode film formation, this film (copper oxide) will sluff off the anodic copper, and if left unattended, will create nodules on the surface of the plated panel. To keep the sluffed copper oxide—referred to as sludge—from contaminating the bath, the anodes are bagged. The bags should be replaced during anode maintenance.
In vertical plating tanks, panels are plated in different cells and various locations within the cell. To minimize variation in copper thickness distribution from the panel racked on the outside edge of the tank relative to the panel in the center of the flight bar and from cell to cell in the tank and from tank to tank requires a good understanding of the role of the anode.
Anode Placement
Proper placement relative to the cathode window of the anode baskets or slabs has a direct impact on the copper thickness distribution. In the case of panel plating, the copper thickness will always be higher toward the edges versus the center of the panel. The outside 2–3”, top, bottom, left, and right edges will exhibit a much higher thickness as compared to the inside area. The thickness increases as the measuring location goes further out away from the center. The increase could be >50%; as an example, the area away from the edges could average 1.0 mil. And as you move toward the outside 2–3 inches of edge, the thickness will gradually increase up to 1.5–2.0 mils at the extreme end of the edge (Figure 1).
Figure 1: Copper thickness distribution.
Ideally, the length of the anode should be 3–4 inches short of the bottom of the panel. This will minimize the increased thickness at the bottom edge of the panel. Butting the vertical edges (of panels) together eliminates the extra thickness along the vertical edges, virtually making the cathode one large panel with only the extreme outside edges needing special attention. The easiest way to reduce over-plating on the outside vertical edges is to tuck the anodes inside the cathode window by 3–4 inches. This leaves the top horizontal edge plated with thicker copper. The remedy here is a lot simpler. Rack the panels within 1 inch of solution level. This will cut off the lines of flux that would cause excessive plating at the top edge of the panel (Figure 2).
Figure 2: Ideal anode placement.
Anodes that are excessively short of the bottom of the panel will favor the top of the panel and plate less on the lower part (Figure 3). If the anode is too long, exceeding the length of the panel; this will favor plating on the lower half of the panel as compared to the top half (Figure 4).
Figure 3: Effect of a short anode on distribution.
Figure 4: Effect of a long anode on distribution.
In short, the length and placement of the anodes plays a very important role in the copper thickness distribution on the surface. If properly maintained this anode configuration relative to the cathode (panels) will yield good, consistent copper thickness distribution.
Page 1 of 3
Suggested Items
Trump Copper Tariffs Spark Concern
07/10/2025 | I-Connect007 Editorial TeamPresident Donald Trump stated on July 8 that he plans to impose a 50% tariff on copper imports, sparking concern in a global industry whose output is critical to electric vehicles, military hardware, semiconductors, and a wide range of consumer goods. According to Yahoo Finance, copper futures climbed over 2% following tariff confirmation.
Happy’s Tech Talk #40: Factors in PTH Reliability—Hole Voids
07/09/2025 | Happy Holden -- Column: Happy’s Tech TalkWhen we consider via reliability, the major contributing factors are typically processing deviations. These can be subtle and not always visible. One particularly insightful column was by Mike Carano, “Causes of Plating Voids, Pre-electroless Copper,” where he outlined some of the possible causes of hole defects for both plated through-hole (PTH) and blind vias.
Trouble in Your Tank: Can You Drill the Perfect Hole?
07/07/2025 | Michael Carano -- Column: Trouble in Your TankIn the movie “Friday Night Lights,” the head football coach (played by Billy Bob Thornton) addresses his high school football team on a hot day in August in West Texas. He asks his players one question: “Can you be perfect?” That is an interesting question, in football and the printed circuit board fabrication world, where being perfect is somewhat elusive. When it comes to mechanical drilling and via formation, can you drill the perfect hole time after time?
The Evolution of Picosecond Laser Drilling
06/19/2025 | Marcy LaRont, PCB007 MagazineIs it hard to imagine a single laser pulse reduced not only from nanoseconds to picoseconds in its pulse duration, but even to femtoseconds? Well, buckle up because it seems we are there. In this interview, Dr. Stefan Rung, technical director of laser machines at Schmoll Maschinen GmbH, traces the technology trajectory of the laser drill from the CO2 laser to cutting-edge picosecond and hybrid laser drilling systems, highlighting the benefits and limitations of each method, and demonstrating how laser innovations are shaping the future of PCB fabrication.
Day 2: More Cutting-edge Insights at the EIPC Summer Conference
06/18/2025 | Pete Starkey, I-Connect007The European Institute for the PCB Community (EIPC) summer conference took place this year in Edinburgh, Scotland, June 3-4. This is the third of three articles on the conference. The other two cover Day 1’s sessions and the opening keynote speech. Below is a recap of the second day’s sessions.