-
- News
- Books
Featured Books
- pcb007 Magazine
Latest Issues
Current IssueInventing the Future with SEL
Two years after launching its state-of-the-art PCB facility, SEL shares lessons in vision, execution, and innovation, plus insights from industry icons and technology leaders shaping the future of PCB fabrication.
Sales: From Pitch to PO
From the first cold call to finally receiving that first purchase order, the July PCB007 Magazine breaks down some critical parts of the sales stack. To up your sales game, read on!
The Hole Truth: Via Integrity in an HDI World
From the drilled hole to registration across multiple sequential lamination cycles, to the quality of your copper plating, via reliability in an HDI world is becoming an ever-greater challenge. This month we look at “The Hole Truth,” from creating the “perfect” via to how you can assure via quality and reliability, the first time, every time.
- Articles
- Columns
- Links
- Media kit
||| MENU - pcb007 Magazine
3D Additive Electronics Manufacturing: Are We Nearing an Inflection Point?
May 28, 2020 | Dan Feinberg, I-Connect007Estimated reading time: 7 minutes
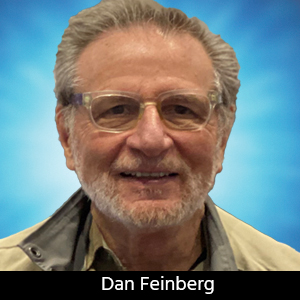
I have been following the advances in 3D additive circuit manufacturing for the past six years, from post-conception to fast-turn prototype production, and from simple printing of conductors on a dielectric to being able to make a loaded circuit board complete with printed resistors and capacitors. In terms of volume, we have gone from very low volume prototypes to moderate volume production circuits. It seems that the rate of progress has accelerated significantly.
We are progressing from the production of a standard circuit board using only 3D printing to printing both the circuit and some components directly onto a base unit. For example, a circuit assembly designed to measure and report temperature can be printed directly onto the component or cylinder that generates the heat. Antennas can be printed directly into a helmet or onto a transmitting/receiving device, and connectors can be printed instead of mounted and connected.
Today, fully functional PCBs with integrated circuit components and other embedded semiconductor devices can be created with 3D printers. The more advanced 3D printing equipment and consumables can produce resolution near micron-level. More than one type of material can be deposited at the same time, which allows for 3D printing of integrated circuits because the co-deposition of conductors and semiconducting materials must be done at the same time. Applications, such as semiconductor chip fabrication, require the integration of different materials simultaneously.
3D additive manufacturing of electronic devices may be at the point, both technically and commercially, where standard circuit board manufacturing was in the ‘50s and ‘60s. That’s when we began the transition from chassis-mounted, hard-wired vacuum tube sockets and point-to-point hand-soldered components to circuit boards with discrete transistors and passive components.
3D-Printed Electronics Webinar
Recently, I was invited to attend a detailed and broadly informative webinar “The Strength of 3D-Printed Electronics” by nScrypt, which covered the status and advances in the use of 3D printing for electronic device design and manufacture.
nScrypt is an Orlando-based company founded in 2002 that focuses on 3D printing. Here’s what I learned about the company: “nScrypt provides tools and processes for next-generation electronic products. Their Factory in a Tool (FiT) has the ability to make complete products on a single platform by using multi-material and multi-processes using precision motion and control. Existing nScrypt machines are made for the existing factory floor where precision processes matter in high volume or stand-alone for personalized products manufactured using digital files. nScrypt tools are made to run 24/7/365 manufacturing products, even when you sleep.”
This webinar focused on the current and future uses of 3D additive manufacturing. I found the speakers to be very informative as they discussed their experience with a broad range of 3D additive manufacturing capabilities, and what they expect as they plan ahead. Here’s what I learned from each of the speakers.
James Zunino
James Zunino is co-founder of the U.S. Army’s additive manufacturing community of practice and a materials engineer at the Combat Capabilities Development Command Armaments Center (CCDCAC) in New Jersey.
He talked about transformative manufacturing techniques for novel printed armament technologies in the areas of additive manufacturing, 3D printing of polymers and metals for flex hybrid electronics, smart manufacturing, automation, robotics, and digital manufacturing. These advanced manufacturing capabilities, James said, are now being used at 18 sites in the United States. Some of the current system efforts include munition power sources, ammunition and warheads, instrumentation for training and simulation, armaments and munitions, remote weapons, and special operations.
My overall impressions are that 3D processes are being used by the military to significantly improve the capability of weapons and provide power solutions with the goal to print as much as possible.
Dr. Kenneth Church
Dr. Kenneth Church is the CEO of nScrypt and detailed current and future efforts in printing electronics. Take the evolution of the smartphone as an example, he said.
The latest phones are full of “stuff,” such as glue and solder—much of which can be eliminated with additive manufacturing that uses printed adhesives, solder, printed antennas, and components. Ken demonstrated with a four-element-phased array antenna complete with an RF structure—a relatively complicated 3D-printed device.
He also mentioned that, as a partner with NASA, they now have a 3D-printing device used on the International Space Station.Page 1 of 2
Testimonial
"Advertising in PCB007 Magazine has been a great way to showcase our bare board testers to the right audience. The I-Connect007 team makes the process smooth and professional. We’re proud to be featured in such a trusted publication."
Klaus Koziol - atgSuggested Items
Indium Promotes Huang to Senior Manager, Marketing Communications
08/28/2025 | Indium CorporationWith its commitment to innovation and growth through employee development, Indium Corporation announces the promotion of Jingya Huang to Senior Manager, Marketing Communications, to continue to lead the company’s branding and promotional efforts.
Rehm Academy Expands Its Training Program
08/28/2025 | Rehm Thermal SystemsThe demands on modern industrial companies and employees continue to rise, and therefore, the topic of further education is becoming increasingly important today.
MacDermid Alpha Awarded for Innovation: Driving Process Optimization and Efficiency with Major Indian EMS Provider
08/28/2025 | MacDermid Alpha Electronics SolutionsMacDermid Alpha Electronics Solutions, a leading global supplier of integrated materials for the electronics industry, is recognized by one of India’s top EMS providers, Syrma SGS, with an award for innovation that advanced process optimization, enhanced operational efficiency, and yield gains.
Integrated Solutions for Board-level Reliability: A Smarter Path Forward
08/27/2025 | Alan Gardner, MacDermid Alpha Electronics SolutionsIn today’s electronics manufacturing landscape, reliability is no longer just a benchmark but a business imperative. As industries such as automotive, aerospace, and high-performance computing (HPC) push the boundaries of innovation, the demand for dependable board-level performance under extreme conditions has never been greater.
ZESTRON Expands Capabilities with Addition of the EPS by i-Tech AG 75 Pallet Cleaning System
08/26/2025 | ZESTRONZESTRON, the global leader in high-precision cleaning solutions and services, is excited to announce the addition of a new capability in its Technical Center in Manassas, VA: