-
- News
- Books
Featured Books
- smt007 Magazine
Latest Issues
Current IssueMoving Forward With Confidence
In this issue, we focus on sales and quoting, workforce training, new IPC leadership in the U.S. and Canada, the effects of tariffs, CFX standards, and much more—all designed to provide perspective as you move through the cloud bank of today's shifting economic market.
Intelligent Test and Inspection
Are you ready to explore the cutting-edge advancements shaping the electronics manufacturing industry? The May 2025 issue of SMT007 Magazine is packed with insights, innovations, and expert perspectives that you won’t want to miss.
Do You Have X-ray Vision?
Has X-ray’s time finally come in electronics manufacturing? Join us in this issue of SMT007 Magazine, where we answer this question and others to bring more efficiency to your bottom line.
- Articles
- Columns
- Links
- Media kit
||| MENU - smt007 Magazine
DELO Launches Liquid Pressure-sensitive Adhesives
November 5, 2020 | Delo Industrial AdhesivesEstimated reading time: 2 minutes
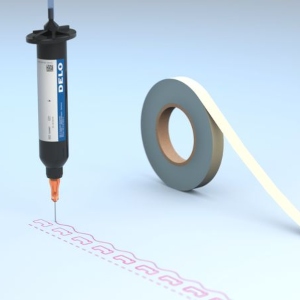
DELO has developed adhesives that have similar properties to (double-sided) adhesive tapes but are applied in liquid form. This helps users save time and costs in the production process. The liquid pressure-sensitive adhesives can be dispensed accurately and once the components have been joined, they can be further processed immediately in a fully automated process. The adhesives are particularly suitable for electronic applications such as smartphone speakers or display frames.
Adhesive tapes are used for numerous bonding applications in the electronics industry. Their advantage is the immediate adhesion after two components have been pressed together. However, adhesive tapes have two major disadvantages. The first is: When using small or complex tape geometries, automated handling becomes very time-consuming or even impossible due to the low stiffness of the carrier material and the high adhesive force. The second is that structures with a low fill factor, like those found in frame bonding, involve a large amount of waste from cutting the geometric shapes, which increases component costs.
The liquid pressure-sensitive adhesives from DELO now open up new possibilities. They are dispensed in liquid form directly onto the component and then irradiated by UV light. This creates a tacky surface, which is characteristic for tapes. Since the adhesive reaches its initial strength immediately after the second component is pressed on, the bonded assembly can be processed directly and without any fixing devices. This is a great advantage over many standard liquid adhesives.
The entire process, from precise dispensing even on tiny components or three-dimensional geometries to irradiation and mechanical pressing, can be fully automated. This makes the liquid pressure-sensitive adhesives particularly suitable for high-output production.
Depending on the requirements, users can choose liquid pressure-sensitive adhesives with different chemical bases. The acrylate-based adhesive DELO PHOTOBOND PS4130 has very similar properties to typical adhesive tape in terms of flexibility, peel resistance and strength. It is particularly suitable for adhesive applications with short cycle times and moderate requirements on final strength. Thanks to its excellent damping properties and low outgassing values, DELO PHOTOBOND PS4130 is already being used, for example, in the assembly of smartphone speakers.
The epoxy-based adhesive DELO KATIOBOND PS6372, on the other hand, was developed specifically for structural bonding applications requiring high strength. Once the initial strength has been achieved by pressing on the components, the assembly can be processed immediately, with the strength of the bonded joint increasing afterwards. When fully cured, DELO KATIOBOND PS6372 achieves compression shear strengths of over 30 MPa on aluminum and over 10 MPa on FR4. Its high resistance to temperature and media makes it also suitable for automotive applications.
Suggested Items
Count On Tools Recognizes Donna Orr’s Ongoing Leadership and Impact Across 27+ Years
06/26/2025 | Count On ToolsCount On Tools, Inc. (COT), a leading provider of precision components and SMT spare parts, is proud to recognize Donna Orr, Executive Manager, for her continued dedication and leadership as she marks more than 27 years with the company.
A Record Year for the 75th Annual IEEE Electronic Components and Technology Conference (ECTC)
06/26/2025 | ECTCThe 75th annual 2025 IEEE Electronic Components and Technology Conference (ECTC), held at the Gaylord Texan Resort & Convention Center here May 27-30, had record attendance, a record number of paper submissions/presentations, record international and student participation, and a record number of exhibitors in a sold-out exhibition hall:
The Death of the Microsection
06/26/2025 | Bob Neves, Reliability Assessment Solutions, Inc.I got my start out of college grinding and polishing PCB microsections. My thumbs are a bit arthritic today because of the experience (microsection grinders know what I mean). Back then, via structures were rather large, and getting to the center in six steps of grinding and polishing was easy compared to what my team has been doing recently at the lab.
Specially Developed for Laser Plastic Welding from LPKF
06/25/2025 | LPKFLPKF introduces TherMoPro, a thermographic analysis system specifically developed for laser plastic welding that transforms thermal data into concrete actionable insights. Through automated capture, evaluation, and interpretation of surface temperature patterns immediately after welding, the system provides unprecedented process transparency that correlates with product joining quality and long-term product stability.
Fresh PCB Concepts: Assembly Challenges with Micro Components and Standard Solder Mask Practices
06/26/2025 | Team NCAB -- Column: Fresh PCB ConceptsMicro components have redefined what is possible in PCB design. With package sizes like 01005 and 0201 becoming more common in high-density layouts, designers are now expected to pack more performance into smaller spaces than ever before. While these advancements support miniaturization and functionality, they introduce new assembly challenges, particularly with traditional solder mask and legend application processes.