-
- News
- Books
Featured Books
- pcb007 Magazine
Latest Issues
Current IssueSales: From Pitch to PO
From the first cold call to finally receiving that first purchase order, the July PCB007 Magazine breaks down some critical parts of the sales stack. To up your sales game, read on!
The Hole Truth: Via Integrity in an HDI World
From the drilled hole to registration across multiple sequential lamination cycles, to the quality of your copper plating, via reliability in an HDI world is becoming an ever-greater challenge. This month we look at “The Hole Truth,” from creating the “perfect” via to how you can assure via quality and reliability, the first time, every time.
In Pursuit of Perfection: Defect Reduction
For bare PCB board fabrication, defect reduction is a critical aspect of a company's bottom line profitability. In this issue, we examine how imaging, etching, and plating processes can provide information and insight into reducing defects and increasing yields.
- Articles
- Columns
- Links
- Media kit
||| MENU - pcb007 Magazine
The Future of Imaging and Inkjet Printing
January 27, 2021 | I-Connect007 Editorial TeamEstimated reading time: 2 minutes
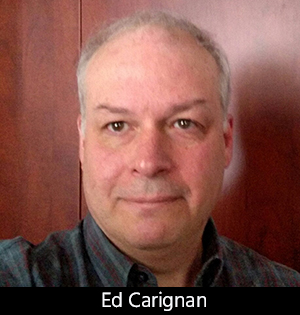
We recently spoke to Ed Carignan of Technica, who outlines the current landscape for both direct imaging and inkjet printing and describes how the technologies have evolved over the years. He also details what’s next on the horizon.
Nolan Johnson: A lot seems to be happening for imaging. I would even go so far as to say that it seems that what’s now being called imaging is changing. How would you describe the landscape for imaging currently? How is it changing, and what’s on the horizon?
Ed Carignan: The biggest change that happened over the last decade was a large-scale conversion from standard phototool-based imaging to direct digital imaging (DI). The technology instantly allowed fabricators to improve registration accuracy, improve productivity, and reduce their reliance on individual operator skill. The change also benefitted PCB designers who could begin to reduce tolerance budgets for higher component densities. A variety of equipment manufacturers now populate this market, driving competitive pricing downward and made the adoption rate very widespread by both large and small PCB fabricators. The two significant contributors to the current success of DI were the development of the equipment platforms (laser-based, UV LED/DMDbased, etc.) and formulation changes made in dry film resist and solder mask materials to reduce photo speeds, allowing for fast exposure times.
What is new are inkjet-based systems used for the direct and additive placement of solder mask on the PCB panel. Inkjet systems for direct digital printing of legend inks have been available and in use by fabricators for many years. However, further improvements in platforms and print head technologies have made the potential for solder mask printing a reality. Similar to the DI development, this technology requires a careful match between the solder mask ink and the equipment’s ink delivery components. A key quality issue for PCB fabricators, assemblers and the end customer is that droplet placement by the piezoelectric, drop-on-demand print head engines negate unintentional placement of solder mask ink on solderable pads. With the development of print heads capable of jetting sub-6 picoliter droplet sizes, it is becoming viable to print solder mask inks directly in place of what was previously done in direct imaging and in an additive process, while also reducing the number of process steps in the bargain.
What will be exciting to watch is how much of that market will be transitioned to inkjet systems over the next decade as more equipment suppliers and more early-adopters ramp-up. There will likely always be a place where both direct imaging and inkjet systems co-exist for various PCB designs and constraints. At Technica, we represent solid partners in both technology spaces: CBT (Taiwan) for DI solutions and SUSS MicroTec (Netherlands) for inkjet equipment.
To read this entire interview, which appeared in the January 2021 issue of PCB007 Magazine, click here.
Suggested Items
Silicon Mountain Contract Services Enhances SMT Capabilities with New HELLER Reflow Oven
07/17/2025 | Silicon Mountain Contract ServicesSilicon Mountain Contract Services, a leading provider of custom electronics manufacturing solutions, is proud to announce a significant upgrade to its SMT production capability with the addition of a HELLER 2043 MK5 10‑zone reflow oven to its Nampa facility.
Knocking Down the Bone Pile: Addressing End-of-life Component Solderability Issues, Part 4
07/16/2025 | Nash Bell -- Column: Knocking Down the Bone PileIn 1983, the Department of Defense identified that over 40% of military electronic system failures in the field were electrical, with approximately 50% attributed to poor solder connections. Investigations revealed that plated finishes, typically nickel or tin, were porous and non-intermetallic.
SHENMAO Strengthens Semiconductor Capabilities with Acquisition of PMTC
07/10/2025 | SHENMAOSHENMAO America, Inc. has announced the acquisition of Profound Material Technology Co., Ltd. (PMTC), a premier Taiwan-based manufacturer of high-performance solder balls for semiconductor packaging.
KYZEN to Highlight Understencil and PCB Cleaners at SMTA Querétaro Expo and Tech Forum
07/09/2025 | KYZEN'KYZEN, the global leader in innovative environmentally responsible cleaning chemistries, will exhibit at the SMTA Querétaro Expo & Tech Forum, scheduled to take place Thursday, July 24, at Centro de Congresos y Teatro Metropolitano de Querétaro.
Driving Innovation: Direct Imaging vs. Conventional Exposure
07/01/2025 | Simon Khesin -- Column: Driving InnovationMy first camera used Kodak film. I even experimented with developing photos in the bathroom, though I usually dropped the film off at a Kodak center and received the prints two weeks later, only to discover that some images were out of focus or poorly framed. Today, every smartphone contains a high-quality camera capable of producing stunning images instantly.