-
-
News
News Highlights
- Books
Featured Books
- smt007 Magazine
Latest Issues
Current IssueWhat's Your Sweet Spot?
Are you in a niche that’s growing or shrinking? Is it time to reassess and refocus? We spotlight companies thriving by redefining or reinforcing their niche. What are their insights?
Moving Forward With Confidence
In this issue, we focus on sales and quoting, workforce training, new IPC leadership in the U.S. and Canada, the effects of tariffs, CFX standards, and much more—all designed to provide perspective as you move through the cloud bank of today's shifting economic market.
Intelligent Test and Inspection
Are you ready to explore the cutting-edge advancements shaping the electronics manufacturing industry? The May 2025 issue of SMT007 Magazine is packed with insights, innovations, and expert perspectives that you won’t want to miss.
- Articles
- Columns
- Links
- Media kit
||| MENU - smt007 Magazine
State of the Coating Industry
June 30, 2021 | Phil Kinner, ElectrolubeEstimated reading time: 4 minutes
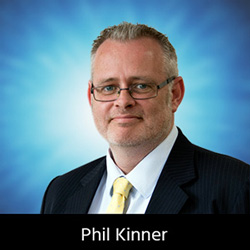
2020 was certainly an interesting year—one that most of us will choose to forget. The list of challenges was seemingly endless: plant shutdowns, project cancellations, component shortages, furloughs, working from home, Microsoft Teams, Brexit, and so forth. Fortunately, life continued largely unchanged for those of us on the R&D team at Electrolube and we were able to complete many of our longer-term projects without the usual day-to-day interruptions. I would say, a win is a win!
As a result of the tremendous progress heralded by the vaccination programme, hope of a return to “normality” is high. However, what will normality look like as we look ahead?
Several trends have really stood out as the first half of 2021 comes to a close. First, 150°C appears to have become the “new normal” for the maximum required operating temperature of conformal coatings for automotive use. This is an increase from 85°C or 120°C on the last generation of products. This new high is really pushing the limits of availability from traditional coating chemistries, but happily for us, this is not a surprise as we have been preparing for this very moment over the last few years—applying ourselves to the generation of solutions and products that support the new requirements.
Condensation resistance continues to grow in importance, increasing in prominence within many new customer specifications. Historically, conformal coatings have been predominantly applied to provide a barrier against the effects of humidity on the underlying circuit. This is not nearly as challenging a scenario as a condensing environment, where the presence of liquid water provides new tests, both to the thickness and coverage achievable. Liquid water will seek out any weak spots in the protection afforded and corrosion takes place much more quickly if this is present. Liquid water can also change the electrical properties of many coatings, causing them to become less insulating than expected—leading to leakage currents and other unexpected electrical behaviours that result in faulty performance of the assembly. We have witnessed many cases of late whereupon companies are performing condensation testing of powered assemblies coated with historical materials and processes, which fail very rapidly, as predicted by the NPL’s recent industry project. Thankfully, there are materials and processes available that can maintain operation and prevent corrosion and failure events under condensing conditions.
Environmental issues have really been in the spotlight over the past 12 months as pollution levels have dropped in many areas due to various lockdowns—despite huge ice sheet breakages and raging wildfires. Throughout the world, governments have pledged commitments to a variety of agreements aiming to reduce greenhouse gases and minimize climate change. For example, this year China has effectively banned the use of certain solvents used in many legacy coating formulations, and heavily restricted the use of solvents in general coatings applications. Whilst conformal coatings are currently exempt from this legislation, it is not hard to imagine that they will be targeted in further legislation or perhaps even the next revision. This has had a knock-on effect with the environmental aspect of corporate social responsibility (CSR) starting to become more apparent at the material specification level. For the first time in my 22 years in the conformal coating industry, I have seen several specifications that specifically preclude the use of solvent-containing or solvent-emitting conformal coating materials. This is not only a great step forward for the environment, but a great step forward for the material users as well. Solvent-free alternative materials are generally higher performing in condensing environments and can have the ability to meet the requirements of the increased maximum thermal operating temperatures.
The IPC-CC-830 Conformal Coating Standard Committee is currently looking to introduce several new classes of coating materials. This reflects the newer types of products that have been introduced to help meet some of these new industry requirements. However, since the pass/fail criteria remains the same for materials from different classes, users will still be required to ensure that the materials are fit for purpose and meet their requirements.
Electrolube remain committed to providing conformal coating solutions to meet current challenges but also pay attention to future requirements. The novel, high-performance, solvent-free 2K range of conformal coatings, initially introduced some five years ago, is finding commercial success in many applications. Improved environmental credentials, as a result of the solvent-free nature and lack of by-products from curing, sit happily alongside improved condensation resistance and are the hallmarks of the 2K range.
As for me, I am really looking forward to resuming live and in-person events where I can talk about conformal coating solutions and solve customer’s challenges and issues with them. I’m also really excited about the product launches we will be making later in the year, as well as unleashing future innovations from our R&D pipeline. Finally, I am really looking forward to our integration journey into MacDermid Alpha Electronics Solutions and the benefits that will see continued investment and the opportunity to work with a much larger global team. 2021 is shaping up to be a very exciting year personally, professionally, and for the industry in general.
Phil Kinner is the global business and technical director of conformal coatings at Electrolube. To read past columns or contact Kinner,?click here. Download your free copy of Electrolube's book, The Printed Circuit Assembler's Guide to… Conformal Coatings for Harsh Environments, and watch the micro webinar series “Coatings Uncoated!”