-
- News
- Books
Featured Books
- smt007 Magazine
Latest Issues
Current IssueWhat's Your Sweet Spot?
Are you in a niche that’s growing or shrinking? Is it time to reassess and refocus? We spotlight companies thriving by redefining or reinforcing their niche. What are their insights?
Moving Forward With Confidence
In this issue, we focus on sales and quoting, workforce training, new IPC leadership in the U.S. and Canada, the effects of tariffs, CFX standards, and much more—all designed to provide perspective as you move through the cloud bank of today's shifting economic market.
Intelligent Test and Inspection
Are you ready to explore the cutting-edge advancements shaping the electronics manufacturing industry? The May 2025 issue of SMT007 Magazine is packed with insights, innovations, and expert perspectives that you won’t want to miss.
- Articles
- Columns
- Links
- Media kit
||| MENU - smt007 Magazine
Review: Emerging Opportunities for Additive Electronics
September 15, 2021 | Pete Starkey, I-Connect007Estimated reading time: 4 minutes
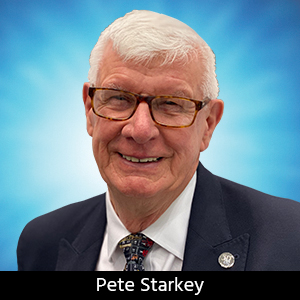
The special feature at SMTA’s virtual Additive Electronics TechXchange 2021 was a presentation by Dr. Matthew Dyson, senior technology analyst at IDTechEx, entitled "Emerging Opportunities for Additive Electronics.”
Introduced by SMTA meetings and events manager Karlie Severinson; moderators were Lenora Clark, director of autonomous driving and safety technology at ESI Automotive, and Tara Dunn, vice president of marketing and business development at Averatek. Dyson’s presentation set a baseline for SMTA’s planned 2022 TechXchange conference which would continue to review industry challenges and opportunities in additive manufacturing.
He began his overview by defining 3D additive electronics as “adding electronic functionality via the sequential deposition of material rather than subtractive techniques such as etching,” and drew a distinction between partially and fully additive processes, with examples of each.Why bother? His response to that rhetorical question was a catalogue of motives and incentives, classified under headings of design flexibility, economics, and environmental. Top of his “design flexibility” list was the integration of mechanics, electronics, and optics, followed by flexibility of shape, miniaturisation, new functionality, increased robustness, mass customisation, and seamless surfaces. His “economics” list included reduced part count, shorter process chains, reduced materials use, increased reliability and rapid design iterations. Environmental motives included reduced materials mix, simplified recycling and disposal, reduced material quantity and reduced parts tourism. Plenty of justification to explore opportunities in advanced electronics packaging as well as in circuit prototyping and manufacturing.
Looking first at advanced electronics packaging, Dyson commented that ICs were reaching the limit of miniaturisation and that emerging packaging methods would lead to improvements in function density. Embedding multiple bare dies in the same package would facilitate further miniaturisation and additive manufacturing methods would enable the economic production of smaller volumes.
Laser direct structuring was a technique for rapid selective patterning of moulded polymers containing a catalyst precursor that could be activated by a laser for subsequent electroless plating. Dyson classified this procedure as only partially-additive because of the initial moulding operation. Aerosol deposition of conductive inks was another partially-additive process option for use in advanced semiconductor packaging. Aerosol jets as small as 20 microns were available, which could print on 3D surfaces. Stereolithography, a form of photochemical 3D printing using a laser to selectively polymerise chemical monomers, could be used to form entire IC packages, incorporating channels and 3D vias into which conductive ink could be printed to form traces and via connections.
3D heterogeneous integration was the long-term aim, incorporating interconnecting substrates, multiple silicon dies, compound active components, mechanical active and passive components, to produce complete system-in-package modules.
Dyson turned his attention to PCB fabrication, particularly rapid in-house prototyping without the IP security risk of outsourcing, and the potential to incorporate novel functionality such as planar capacitors. Multilayers could be additively manufactured without etching or laminating operations, electroplating would be optional and surface-mount components could be assembled on both sides. He showed a series of examples of real-world functional circuits and assemblies, including an RF circuit for satellite communications, recently launched onto the International Space Station.
An example of partially-additive manufacturing was a print-then-plate process that enabled PCBs to be produced without etching. The pattern was produced by inkjet printing a conductive nano-ink, which was subsequently fully-metallised by electroless plating. The process sequence was shorter than standard, consumed less copper and was suitable for high-mix low-volume production.
A process in development used the principles of stereolithography and laser direct structuring, already discussed in connection with IC packaging, but with a newly formulated resin compatible with both technologies, to produce custom-made sensor housings for industrial IoT on older-but-still-functioning machinery.
Dyson showed examples of integrated devices that had been fully 3D printed, including a hermetically sealed automotive accelerometer and a magnetic flux sensor.
So what were the challenges for widespread adoption? Throughput was an obvious limiting factor; in general the higher the resolution, the slower the production rate and the higher the cost. Scaling the operation by increasing the number of nozzles was an obvious approach. Techniques like laser-induced forward transfer, which combined optical patterning with additive deposition, and print-then-ablate, which was effectively a part-additive part-subtractive procedure, could offer speed increases. For ultra-fine-line patterning, a development of inkjet known as electrohydrodynamic printing was capable of one-micron resolution. Inevitably, this was a slow process.
Another issue was sustainability; if wiring and components were integrated within the structural dielectric, recycling was difficult although some depolymerisation technologies were being evaluated and the use of copper inks instead of silver might improve biodegradability.
Durability was a further consideration, particularly with respect to expansion mismatch causing failures during thermal cycling. Using fillers in dielectric resins could reduce the problem, but might compromise other physical or electrical properties.
Dyson used a roadmap produced by Holst Centre, the Dutch research and innovation organisation, to summarise the technology trend and readiness level of additive manufacturing in IC packaging and PCB prototyping and production, from concept to commercialisation. The trend was illustrated by a graph of increasing capability vs. time, with a second curve indicating decreasing unit cost. The crossover point coincided with a reference line representing traditional production at some time in the near future, nominally at the “scaling-up” stage where resolution had reached 20-micron line and space, throughput more than 1,000 units of 1 cubic centimetre per hour, performance equivalent to 30% that of bulk copper, and a high level of reliability. He concluded with an adoption roadmap for the next decade, with forecasts for circuit prototyping, custom sensor housing, advanced electronics packaging, optical sensor packaging, microfuidics and MEMS, and integrated devices.
His presentation initiated a lively session of interactive discussion and successfully established a baseline for the 2022 TechXchange conference, which is scheduled for February 17 in San Jose.