-
- News
- Books
Featured Books
- smt007 Magazine
Latest Issues
Current IssueWhat's Your Sweet Spot?
Are you in a niche that’s growing or shrinking? Is it time to reassess and refocus? We spotlight companies thriving by redefining or reinforcing their niche. What are their insights?
Moving Forward With Confidence
In this issue, we focus on sales and quoting, workforce training, new IPC leadership in the U.S. and Canada, the effects of tariffs, CFX standards, and much more—all designed to provide perspective as you move through the cloud bank of today's shifting economic market.
Intelligent Test and Inspection
Are you ready to explore the cutting-edge advancements shaping the electronics manufacturing industry? The May 2025 issue of SMT007 Magazine is packed with insights, innovations, and expert perspectives that you won’t want to miss.
- Articles
- Columns
- Links
- Media kit
||| MENU - smt007 Magazine
Mining for Metals Requires a Long View
June 15, 2022 | Nolan Johnson, I-Connect007Estimated reading time: 3 minutes
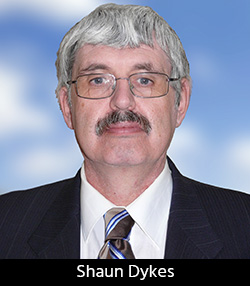
Nolan Johnson talks with Shaun Dykes, a 50-year expert in the mining industry. Dykes gives a concise primer on mining development, and the amount of time and effort required to develop and supply the mineral resources we depend upon for the manufacture of printed circuit boards. There are many factors that play into when and where a mine is developed—and what can prevent a mine from ever producing minerals.
Nolan Johnson: Shaun, what is your specific role and your background?
Shaun Dykes: I’m the president and CEO at American CuMO Mining Corp., and an engineer and geologist by background. I’ve been in the business for almost 50 years. I’ve been all over the world, looking at and worked on deposits in different regimes, governments, and bureaucracies from Canada, U.S., and Australia. I spent time in Russia and South America as well.
Johnson: Minerals and their role in the supply chain for finished metals has a great impact on my readers. They rely on the copper, tin, lead, and all the metals that go onto those fiberglass boards. In addition, there’s solder and the minerals involved in those formulations. Copper, of course, plays a central role; that seems to be a metal at the core of the dynamics going on.
What are some of the global supply and demand trends in your industry and how might that be affecting us in electronics manufacturing?
Dykes: Metals, especially now with all the new technologies, are appearing everywhere—your circuitry, desalination plants, batteries, even your drinking water. Every single metal is in strong demand. The supply is getting shorter and shorter, and as mines become older, the grades are dropping and that reduces the amount of metal available. It now takes about five times longer to permit a mine than it used to because of the new regulations and rules you must go through.
Even then, some mines just can’t go into production because they’re either too costly or the opposition is too strong, and you can’t get the permits to proceed. Right now, the supply is far less than the demand. Of course, that demand is increasing on a steady basis, year in, year out. That’s why you’re seeing the increase in metal prices.
Johnson: It sounds to me like any sort of domestic mining is under even stricter regulation, even while the demand is going up.
Dykes: Definitely. What we go through in the mining industry—some of it’s good, while some is red tape and just absolute garbage. But other parts are good for the environment to make sure that the old days of mining, where you just rape and pillage with no care for what was going on, is long gone. Now, when we look at developing new mines, one of the first things we look at is the environment—rare and endangered species, trees, and more, before we even start spending the hundreds of millions of dollars it takes to develop a mine.
Johnson: Hundreds of millions of dollars to develop a mine? In our space, to build a computer chip factory, a semiconductor factory, is hundreds of millions of dollars and four or five years before it’s producing. Is it comparable with a mine? If you decide to go forward, how quickly can you get a mine up and running?
Dykes: Well, it depends. From first boots on the ground, you’ve got to drill it and explore; for the larger scale mines, like the ones that supply your metals, it’s averaging close to 20 years.
Johnson: Twenty years to get a mine started?
Dykes: From when you’ve discovered and outlined it, and let’s say you’ve got all your resources and a bankable feasibility study, it’s probably two to four years to construct it. Your construction costs can range from a couple hundred million dollars for the small mines up to several billion dollars for the large scale. A large-scale copper mine today will cost $2 billion to $3 billion, maybe even more. We’ve been working on a mine in Idaho since 2004. We still have about two years to go on the economic analysis part and then it will be three or four years to build it. The cost to build it is anywhere from $1 billion to $3 billion.
To read the rest of this article, which appeared in the June 2022 issue of SMT007 Magazine, click here.
Suggested Items
SHENMAO Strengthens Semiconductor Capabilities with Acquisition of PMTC
07/10/2025 | SHENMAOSHENMAO America, Inc. has announced the acquisition of Profound Material Technology Co., Ltd. (PMTC), a premier Taiwan-based manufacturer of high-performance solder balls for semiconductor packaging.
KYZEN to Highlight Understencil and PCB Cleaners at SMTA Querétaro Expo and Tech Forum
07/09/2025 | KYZEN'KYZEN, the global leader in innovative environmentally responsible cleaning chemistries, will exhibit at the SMTA Querétaro Expo & Tech Forum, scheduled to take place Thursday, July 24, at Centro de Congresos y Teatro Metropolitano de Querétaro.
Driving Innovation: Direct Imaging vs. Conventional Exposure
07/01/2025 | Simon Khesin -- Column: Driving InnovationMy first camera used Kodak film. I even experimented with developing photos in the bathroom, though I usually dropped the film off at a Kodak center and received the prints two weeks later, only to discover that some images were out of focus or poorly framed. Today, every smartphone contains a high-quality camera capable of producing stunning images instantly.
Hands-On Demos Now Available for Apollo Seiko’s EF and AF Selective Soldering Lines
06/30/2025 | Apollo SeikoApollo Seiko, a leading innovator in soldering technology, is excited to spotlight its expanded lineup of EF and AF Series Selective Soldering Systems, now available for live demonstrations in its newly dedicated demo room.
Indium Corporation Expert to Present on Automotive and Industrial Solder Bonding Solutions at Global Electronics Association Workshop
06/26/2025 | IndiumIndium Corporation Principal Engineer, Advanced Materials, Andy Mackie, Ph.D., MSc, will deliver a technical presentation on innovative solder bonding solutions for automotive and industrial applications at the Global Electronics A