-
- News
- Books
Featured Books
- pcb007 Magazine
Latest Issues
Current IssueThe Hole Truth: Via Integrity in an HDI World
From the drilled hole to registration across multiple sequential lamination cycles, to the quality of your copper plating, via reliability in an HDI world is becoming an ever-greater challenge. This month we look at “The Hole Truth,” from creating the “perfect” via to how you can assure via quality and reliability, the first time, every time.
In Pursuit of Perfection: Defect Reduction
For bare PCB board fabrication, defect reduction is a critical aspect of a company's bottom line profitability. In this issue, we examine how imaging, etching, and plating processes can provide information and insight into reducing defects and increasing yields.
Voices of the Industry
We take the pulse of the PCB industry by sharing insights from leading fabricators and suppliers in this month's issue. We've gathered their thoughts on the new U.S. administration, spending, the war in Ukraine, and their most pressing needs. It’s an eye-opening and enlightening look behind the curtain.
- Articles
- Columns
- Links
- Media kit
||| MENU - pcb007 Magazine
PCB Plating Still Comes Down to Physics
June 21, 2022 | I-Connect007 Editorial TeamEstimated reading time: 3 minutes
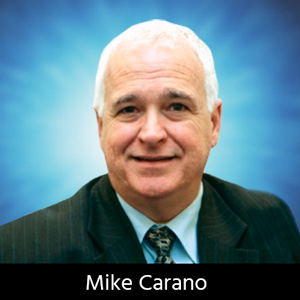
For this month’s plating issue, we spoke with I-Connect007 columnist Michael Carano, a longtime surface finish expert with years of experience at RBP Chemical and OM Group. We asked Michael to discuss the latest innovations in plating equipment and chemicals, as well as some of the drivers in this segment, and the biggest challenges and opportunities he sees in plating today.
As Michael points out, despite all of the technological advances in this industry, process engineers still need a solid understanding of Faraday’s Law and Ohm’s Law to successfully plate PCBs.
Andy Shaughnessy: This is our electroplating issue, and I’ve heard you say that you know how to plate anything. What's the latest in electroplating? What sort of innovations and challenges are you seeing in processes, equipment, etc.?
Michael Carano: If you go back 30 years, what's different in electroplating technology? Forget about electrodes for now. What's different about electroplating technology? I like to call it electrodeposition because we are attaching electrodes and we're running current through a tank. In the last 10–15 years, it hasn't changed much. But what has changed is the technology of the circuit board—smaller vias and thicker boards. Whenever you make a via smaller and you add more layers, what you do is you increase what they call the ohmic resistance through the via.
With Ohm's Law, V = IR; you apply a voltage to a plating tank. If you have a 10:1 aspect ratio board and a 20:1 aspect ratio board, which one is going to be more difficult to plate? Very simple: the 20:1, because the resistance increases significantly down through the hole. From a technology standpoint, you've got to make several adjustments, which the industry has. We’ve seen adjustments in tank design, plating rack design, process control, and the formulation of new additives that enhances throwing power and overall plating distribution.
It's always funny when someone says, "Why can't we just do this?" Well, you're violating Faraday's Law. There are only so many things you can do and you can't violate certain laws of the universe. Faraday's Law is one that you don't mess with. So you've got to manipulate the amperage, the voltage, and all the things that make a difference in getting chemistry into the hole.
That's significant. Then we went to periodic reverse pulse plating, which is basically electroplating except it uses a reverse current as well as a forward current. It makes adjustments in the wave shape using square wave vs. more turbulent type waves. That has helped tremendously to plate and improve the reliability of the thicker through-hole printed circuit boards.
Finally, one of the things that was borrowed from the semiconductor industry—we've all talked about what's new because sometimes it's not new, it's just re-cloaked in a new technology—is they learned to plate copper in narrow trenches. They call it damascene plating; they actually fill a trench with electroplated copper. Of course, the trenches are very minute compared to a blind via of a circuit board, but the circuit board industry and the suppliers, in my experiences, have been able to adapt to chemistry and, again, the agitation and other adjustments, to fill blind vias by electroplating copper in a via from what's called bottom-up filling, super fill, without necessarily overplating on the top. That has helped create HDI and ultra-HDI and allowed that technology to really blossom.
How do you fill blind vias when you're not going to put a component in them? You need to fill them with something. It's like the saying: A man digs a hole, and then he wants to fill it. Well, you must fill the hole in a blind via because you can't have air in a blind via if you're not going to put components in it.
To read this entire conversation, which appeared in the June 2022 issue of PCB007 Magazine, click here.
Suggested Items
Trump Copper Tariffs Spark Concern
07/10/2025 | I-Connect007 Editorial TeamPresident Donald Trump stated on July 8 that he plans to impose a 50% tariff on copper imports, sparking concern in a global industry whose output is critical to electric vehicles, military hardware, semiconductors, and a wide range of consumer goods. According to Yahoo Finance, copper futures climbed over 2% following tariff confirmation.
Happy’s Tech Talk #40: Factors in PTH Reliability—Hole Voids
07/09/2025 | Happy Holden -- Column: Happy’s Tech TalkWhen we consider via reliability, the major contributing factors are typically processing deviations. These can be subtle and not always visible. One particularly insightful column was by Mike Carano, “Causes of Plating Voids, Pre-electroless Copper,” where he outlined some of the possible causes of hole defects for both plated through-hole (PTH) and blind vias.
Trouble in Your Tank: Can You Drill the Perfect Hole?
07/07/2025 | Michael Carano -- Column: Trouble in Your TankIn the movie “Friday Night Lights,” the head football coach (played by Billy Bob Thornton) addresses his high school football team on a hot day in August in West Texas. He asks his players one question: “Can you be perfect?” That is an interesting question, in football and the printed circuit board fabrication world, where being perfect is somewhat elusive. When it comes to mechanical drilling and via formation, can you drill the perfect hole time after time?
The Evolution of Picosecond Laser Drilling
06/19/2025 | Marcy LaRont, PCB007 MagazineIs it hard to imagine a single laser pulse reduced not only from nanoseconds to picoseconds in its pulse duration, but even to femtoseconds? Well, buckle up because it seems we are there. In this interview, Dr. Stefan Rung, technical director of laser machines at Schmoll Maschinen GmbH, traces the technology trajectory of the laser drill from the CO2 laser to cutting-edge picosecond and hybrid laser drilling systems, highlighting the benefits and limitations of each method, and demonstrating how laser innovations are shaping the future of PCB fabrication.
Day 2: More Cutting-edge Insights at the EIPC Summer Conference
06/18/2025 | Pete Starkey, I-Connect007The European Institute for the PCB Community (EIPC) summer conference took place this year in Edinburgh, Scotland, June 3-4. This is the third of three articles on the conference. The other two cover Day 1’s sessions and the opening keynote speech. Below is a recap of the second day’s sessions.