The Importance of Rigid-Flex PCB Design Guidelines
July 21, 2022 | Cody Stetzel, Cadence Design SystemsEstimated reading time: 2 minutes
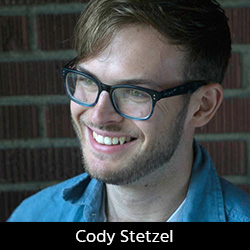
I have the tendency to try to replicate the delicacies I’ve ordered at restaurants in my own kitchen. One of my latest attempts at creating restaurant-worthy dishes was a Korean pancake that’s crispy on the outside but soft on the inside. With my amateur cooking skills, it proved to be an impossible task—I could either make only a hard pancake or one that was total fluff.
While I’m still struggling to figure out the trick to bringing together the different textures of a Korean pancake, I’ve had more success in bringing together the hardboard elements and flexible PCB elements of a rigid-flex PCB. Compared to making Korean pancakes, striking the right balance of flexibility and rigidity on a rigid-flex PCB is easy if you abide by rigid-flex PCB design guidelines.
What Is a Rigid-Flex PCB?
For those who have spent their careers designing conventional PCBs on the FR-4 substrate, a rigid-flex PCB may be unfamiliar territory. As the name implies, a rigid-flex PCB is a PCB that combines both elements of a hardboard and a flexible PCB in a single piece.
A rigid-flex design is typically made up of two or more rigid areas that are interconnected by a flexible strip. The synergistic property of the rigid and flex elements allow the PCB to be bent or folded in applications.
Rigid-flex PCBs are getting more attention in recent years, due to the demand for more compact, shock-resistant, and robust electronics. A rigid-flex design eliminates the need for connectors and interconnecting cables. Rigid-flex PCBS are also easier to install, as the entire design is manufactured on a single PCB.
Material Considerations for Rigid-Flex PCB Design
You’ll want to consult your PCB manufacturer before starting a design. Depending on whether the PCB is meant for dynamic bend or stable bend, the choice of copper type, the number of layers, bend radius, and coverlays may differ.
A dynamic bend rigid-flex PCB is installed in an environment where it will constantly be subjected to bending. Therefore, it is recommended to use no more than two layers and ensure that the bending radius is at least 100 times the material thickness.
Meanwhile, it’s possible to have up to 10 to 20 layers for a rigid-flex PCB that’s meant for stable-bend installations. It is not subjected to repeated bending force and that means a smaller bending radius of about 10 times its material thickness is also possible.
To read this article, which appeared in the July 2022 issue of Design007 Magazine, click here.
Suggested Items
I-Connect007 Editor’s Choice: Five Must-Reads for the Week
07/18/2025 | Nolan Johnson, I-Connect007It may be the middle of the summer, but the news doesn’t quit, and there’s plenty to talk about this week, whether you’re talking technical or on a global scale. When I have to choose six items instead of my regular five, you know it’s good. I start by highlighting my interview with Martyn Gaudion on his latest book, share some concerning tariff news, follow that up with some promising (and not-so-promising) investments, and feature a paper from last January’s inaugural Pan-European Design Conference.
Elephantech Launches World’s Smallest-Class Copper Nanofiller
07/17/2025 | ElephantechJapanese deep-tech startup Elephantech has launched its cutting-edge 15 nm class copper nanofiller – the smallest class available globally. This breakthrough makes Elephantech one of the first companies in the world to provide such advanced material for commercial use.
Copper Price Surge Raises Alarms for Electronics
07/15/2025 | Global Electronics Association Advocacy and Government Relations TeamThe copper market is experiencing major turbulence in the wake of U.S. President Donald Trump’s announcement of a 50% tariff on imported copper effective Aug. 1. Recent news reports, including from the New York Times, sent U.S. copper futures soaring to record highs, climbing nearly 13% in a single day as manufacturers braced for supply shocks and surging costs.
I-Connect007 Editor’s Choice: Five Must-Reads for the Week
07/11/2025 | Andy Shaughnessy, Design007 MagazineThis week, we have quite a variety of news items and articles for you. News continues to stream out of Washington, D.C., with tariffs rearing their controversial head again. Because these tariffs are targeted at overseas copper manufacturers, this news has a direct effect on our industry.I-Connect007 Editor’s Choice: Five Must-Reads for the Week
Digital Twin Concept in Copper Electroplating Process Performance
07/11/2025 | Aga Franczak, Robrecht Belis, Elsyca N.V.PCB manufacturing involves transforming a design into a physical board while meeting specific requirements. Understanding these design specifications is crucial, as they directly impact the PCB's fabrication process, performance, and yield rate. One key design specification is copper thieving—the addition of “dummy” pads across the surface that are plated along with the features designed on the outer layers. The purpose of the process is to provide a uniform distribution of copper across the outer layers to make the plating current density and plating in the holes more uniform.