-
-
News
News Highlights
- Books
Featured Books
- smt007 Magazine
Latest Issues
Current IssueWhat's Your Sweet Spot?
Are you in a niche that’s growing or shrinking? Is it time to reassess and refocus? We spotlight companies thriving by redefining or reinforcing their niche. What are their insights?
Moving Forward With Confidence
In this issue, we focus on sales and quoting, workforce training, new IPC leadership in the U.S. and Canada, the effects of tariffs, CFX standards, and much more—all designed to provide perspective as you move through the cloud bank of today's shifting economic market.
Intelligent Test and Inspection
Are you ready to explore the cutting-edge advancements shaping the electronics manufacturing industry? The May 2025 issue of SMT007 Magazine is packed with insights, innovations, and expert perspectives that you won’t want to miss.
- Articles
- Columns
- Links
- Media kit
||| MENU - smt007 Magazine
Solder Paste Printing and Optimizations for Interconnecting Back Contact Cells
July 26, 2022 | Narahari S Pujari and Krithika PM, MacDermid Alpha Electronics SolutionsEstimated reading time: 2 minutes
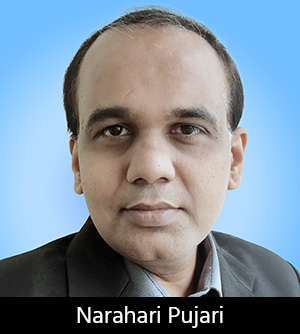
Introduction
The interdigitated back contact (IBC) is one of the methods to achieve rear contact solar cell interconnection. The contact and interconnection via rear side theoretically achieve higher efficiency by moving all the front contact grids to the rear side of the device. This results in all interconnection structures being located behind the cells, which brings two main advantages. First, there is no frontside shading of the cell by the interconnection ribbons, thus eliminating the need for trading off series resistance, losses for shading losses when using larger interconnection ribbons. Second, a more homogeneous looking frontside of the solar module enhances the aesthetics. This combined increased power yield and improved aesthetics make back-contact modules particularly suited for special applications such as vehicle and building integration.
Out of many ways of interconnecting the IBC cells, busbar stringing, which is similar to conventional tabbing and stringing of two-side contacted cells, is the most common method2. In this technique, the metallization design of the cell contains multiple parallel-printed busbars distributed over the cell, allowing shorter finger length, and ribbon on busbar soldering. This reduces the resistance losses in the metallization compared to the edge stringing. With the advent in multibar bar (MBB) technology, the width of these busbars is also reducing and is down to around 300 to 500 microns. The interconnection can be carried out by either ECA (electrically conductive adhesives) or by using direct ribbon/wire. Both materials have created some challenges. The poor peel strength is often the major issue. The uniform IMC (intermetallic layer), which is characteristic of reliable bond strength, is absent with ECA. The metallization paste used in IBC is low-temperature-curing silver paste. The paste is fired at lower temperature around 500°C or less and deposited on silicon cell. In addition to that, the height of the paste is only about 8-12 micron. Because of this, silver leaching during interconnection is commonly observed. The metallization just comes off during interconnection at high temperature. If used, solder wire, cold solder joints, and solder diffusion through the cell are the major issues. Poor adhesion between cell and ECA, and interconnecting wire, high contact resistance are other common problems. Accordingly, when a circuit or conductive layer or interconnection is formed on a substrate using such conventional pastes, damage to the substrate or failure in reliability of the device may occur. Further, when ECA is used, silver in the ECA is expensive and appears on various restricted chemicals lists due its short supply.
To read this entire paper, which appeared in the July 2022 issue of SMT007 Magazine, click here.
Suggested Items
Knocking Down the Bone Pile: Addressing End-of-life Component Solderability Issues, Part 4
07/15/2025 | Nash Bell -- Column: Knocking Down the Bone PileIn 1983, the Department of Defense identified that over 40% of military electronic system failures in the field were electrical, with approximately 50% attributed to poor solder connections. Investigations revealed that plated finishes, typically nickel or tin, were porous and non-intermetallic.
SHENMAO Strengthens Semiconductor Capabilities with Acquisition of PMTC
07/10/2025 | SHENMAOSHENMAO America, Inc. has announced the acquisition of Profound Material Technology Co., Ltd. (PMTC), a premier Taiwan-based manufacturer of high-performance solder balls for semiconductor packaging.
KYZEN to Highlight Understencil and PCB Cleaners at SMTA Querétaro Expo and Tech Forum
07/09/2025 | KYZEN'KYZEN, the global leader in innovative environmentally responsible cleaning chemistries, will exhibit at the SMTA Querétaro Expo & Tech Forum, scheduled to take place Thursday, July 24, at Centro de Congresos y Teatro Metropolitano de Querétaro.
Driving Innovation: Direct Imaging vs. Conventional Exposure
07/01/2025 | Simon Khesin -- Column: Driving InnovationMy first camera used Kodak film. I even experimented with developing photos in the bathroom, though I usually dropped the film off at a Kodak center and received the prints two weeks later, only to discover that some images were out of focus or poorly framed. Today, every smartphone contains a high-quality camera capable of producing stunning images instantly.
Hands-On Demos Now Available for Apollo Seiko’s EF and AF Selective Soldering Lines
06/30/2025 | Apollo SeikoApollo Seiko, a leading innovator in soldering technology, is excited to spotlight its expanded lineup of EF and AF Series Selective Soldering Systems, now available for live demonstrations in its newly dedicated demo room.