-
- News
- Books
Featured Books
- pcb007 Magazine
Latest Issues
Current IssueThe Hole Truth: Via Integrity in an HDI World
From the drilled hole to registration across multiple sequential lamination cycles, to the quality of your copper plating, via reliability in an HDI world is becoming an ever-greater challenge. This month we look at “The Hole Truth,” from creating the “perfect” via to how you can assure via quality and reliability, the first time, every time.
In Pursuit of Perfection: Defect Reduction
For bare PCB board fabrication, defect reduction is a critical aspect of a company's bottom line profitability. In this issue, we examine how imaging, etching, and plating processes can provide information and insight into reducing defects and increasing yields.
Voices of the Industry
We take the pulse of the PCB industry by sharing insights from leading fabricators and suppliers in this month's issue. We've gathered their thoughts on the new U.S. administration, spending, the war in Ukraine, and their most pressing needs. It’s an eye-opening and enlightening look behind the curtain.
- Articles
- Columns
- Links
- Media kit
||| MENU - pcb007 Magazine
MKS Discusses the Cutting Edge of Technology
December 20, 2022 | Nolan Johnson, I-Connect007Estimated reading time: 3 minutes
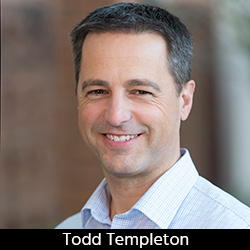
During a recent tour of the MKS facility in Beaverton, Oregon, I met with Todd Templeton, Chris Ryder, Kyle Baker, and Martin Orrick. As a reminder, MKS acquired ESI in 2019 and has retained the ESI brand. In this interview, they explain their approach to HDI and ultra HDI, the current state of base materials, and what the future looks like on the cutting edge of technology.
Nolan Johnson: Todd, what are you seeing in the market and what’s happening with your customers? What are the dynamics and what are their pain points?
Todd Templeton: When it comes to HDI, we have seen a big shift in historical spending recently, with a lot more investment into the IC substrate space. In 2019, we introduced the Geode™ drilling system, primarily targeted at the HDI market. Since then, we’ve heard customers say, “That’s great, but what can you do for me over here in IC substrate?” Therefore, we’re looking at ABF (Ajinomoto Build-up Film) substrates and investing more heavily to meet customer demand.
Chris Ryder: We’re expanding the Geode CO2 via drilling system into that IC substrate space, and it has turned out to be an excellent modular platform for a broad range of applications. It has worked well in adopting and adapting into various rigid panel products. The Geode via drilling system already has quite a breadth of range from standard commodity HDI products to mSAP and SLP substrates, but these are all copper-clad materials. Hence, we’ve been evolving and adapting the platform toward an additional ABF-specific configuration for the FCBGA market with a future plan to expand in that market.
To be clear, we already serve some portion of the ABF-based market with the higher end of the Geode via drilling system configurations, but there’s effort to focus more specifically on that product range and market segment. As we move forward, we’ll certainly be sharing more details.
Johnson: Are you finding more willingness to invest uniformly across the globe?
Templeton: Yes, we’re seeing it all over. It’s not regionally dependent. As Chris was saying, we have a solid platform with our products to address the HDI and mSAP markets, but our customers are saying, “Our investment has increasingly shifted to IC substrate; do you have a solution for me there?” With some minor adjustments to our system architecture, we can have a compelling product in that space. It has been driving some of our development and focus in the rigid panel space. When it comes to flex, we have multiple legs of the stool that support demand for our products.
Johnson: When the pandemic started, you had a good idea that those applications would lead the way. Has that shifted and changed?
Templeton: Has it changed? Primarily, that time was driven by 5G. We were looking to make sure everything had the right components, such as antennas, the bay stations, etc. I don’t think that it’s shifted much since then.
Ryder: The pandemic created more demand for high-power, high-performance computing, or “HPC.” That’s certainly been a driver behind the FCBGA and ABF upward trend. Development in this market was there before the pandemic, but the focus has grown and accelerated demand since.
Johnson: As well as the cloud-based data centers, and core streaming content?
Ryder: Yes. Servers, HPC, and data centers have definitely seen growth. There has been an uptick in demand over the last couple of years. On the other hand, our customers have become more thoughtful about which technologies to invest in, as well as the timing of these investments. This has somewhat changed the technology adoption pace of the past decade or so.
Johnson: It would seem to imply it’s slowing down and getting conservative.
Ryder: Not necessarily. Manufacturers are looking to react more swiftly to present trends vs. second guessing long-term trends. Our customers, for example, are looking for shorter lead times on our equipment to facilitate more timely decisions on when to execute for product integration, product implementation, and time to market. There have been some areas in the industry where we’ve succeeded by having a quicker response to those demands. When customers decide to pull the trigger on a project, they can’t deal with a one-year lead time for a manufacturing tool. Our agility has been beneficial for us.
To read this entire conversation, which appeared in the November 2022 issue of PCB007 Magazine, click here.
Suggested Items
I-Connect007 Editor’s Choice: Five Must-Reads for the Week
07/11/2025 | Andy Shaughnessy, Design007 MagazineThis week, we have quite a variety of news items and articles for you. News continues to stream out of Washington, D.C., with tariffs rearing their controversial head again. Because these tariffs are targeted at overseas copper manufacturers, this news has a direct effect on our industry.I-Connect007 Editor’s Choice: Five Must-Reads for the Week
Digital Twin Concept in Copper Electroplating Process Performance
07/11/2025 | Aga Franczak, Robrecht Belis, Elsyca N.V.PCB manufacturing involves transforming a design into a physical board while meeting specific requirements. Understanding these design specifications is crucial, as they directly impact the PCB's fabrication process, performance, and yield rate. One key design specification is copper thieving—the addition of “dummy” pads across the surface that are plated along with the features designed on the outer layers. The purpose of the process is to provide a uniform distribution of copper across the outer layers to make the plating current density and plating in the holes more uniform.
Trump Copper Tariffs Spark Concern
07/10/2025 | I-Connect007 Editorial TeamPresident Donald Trump stated on July 8 that he plans to impose a 50% tariff on copper imports, sparking concern in a global industry whose output is critical to electric vehicles, military hardware, semiconductors, and a wide range of consumer goods. According to Yahoo Finance, copper futures climbed over 2% following tariff confirmation.
Happy’s Tech Talk #40: Factors in PTH Reliability—Hole Voids
07/09/2025 | Happy Holden -- Column: Happy’s Tech TalkWhen we consider via reliability, the major contributing factors are typically processing deviations. These can be subtle and not always visible. One particularly insightful column was by Mike Carano, “Causes of Plating Voids, Pre-electroless Copper,” where he outlined some of the possible causes of hole defects for both plated through-hole (PTH) and blind vias.
Trouble in Your Tank: Can You Drill the Perfect Hole?
07/07/2025 | Michael Carano -- Column: Trouble in Your TankIn the movie “Friday Night Lights,” the head football coach (played by Billy Bob Thornton) addresses his high school football team on a hot day in August in West Texas. He asks his players one question: “Can you be perfect?” That is an interesting question, in football and the printed circuit board fabrication world, where being perfect is somewhat elusive. When it comes to mechanical drilling and via formation, can you drill the perfect hole time after time?