Rice Flashes New Life Into Lithium-ion Anodes
December 30, 2022 | Rice UniversityEstimated reading time: 2 minutes
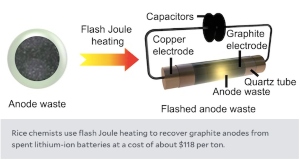
How many rechargeable lithium-ion batteries are you wearing? How many are in your general vicinity?
Probably more than a few, and they’re great for powering all the things important to modern lives: cellphones, watches, computers, cars and so much more.
But where they go when they fail is a growing problem. Rice University scientists believe they have a partial solution that relies on the unique “flash” Joule heating process they developed to produce graphene from waste.
The Rice lab of chemist James Tour has reconfigured the process to quickly regenerate graphite anode materials found in lithium-ion batteries, removing impurities so they can be used again and again.
The lab’s work appears in Advanced Materials.
Flashing powdered anodes from commercial batteries recycles some of what the researchers called the “staggering” accumulation of waste they currently leave behind. In just a few seconds, a jolt of high energy decomposes inorganic salts including lithium, cobalt, nickel and manganese from an anode. These can be recovered by processing them with dilute hydrochloric acid.
“The production of lithium-ion batteries in 2026 is expected to be five times what it was in 2017, and right now, less than 5% of them are recycled,” said Tour, who introduced the flash process for graphene in 2020. “That puts a heavy load on the environment, as these spent batteries are processed and the anodes burned for energy or sent for landfills.
“We’re claiming our process can recover critical metals and recondition anodes in a far more environmentally and economically friendly manner,” he continued.
The lab reported that flashing anodes degrades the solid-electrolyte interphase (SEI), which conducts lithium ions but also insulates the anode from detrimental reactions.
Flashing then coats the remaining graphite particles with an ion-permeable carbon shell that contributes to their future capacity, rate performance and cycling stability compared to materials conventionally recycled in a time-consuming and energy-intensive process known as high-temperature calcination.
The lab estimated it would cost about $118 to recycle one ton of untreated anode waste. They demonstrated that flash-recycled anodes have a recovered specific capacity of 351 milliAmp hours per gram at 32 degrees Fahrenheit, superior to the rate performance and electrochemical stability of untreated or calcinated recycled anodes.
The recycled, flashed anodes the researchers tested retained more than 77% of their capacity after 400 recharge cycles.
“Beyond the spent graphite anodes, we are confident that the cathodes, the electrolytes and their mixtures can be effectively recycled or reconditioned by our method,” said Rice graduate student Weiyin Chen, lead author of the study.
Co-authors are Rice academic visitor Rodrigo Salvatierra; alumnus John Tianci Li; research scientist Carter Kittrell; graduate students Jacob Beckham, Kevin Wyss, Nghi La, Paul Savas, Chang Ge, Paul Advincula, Phelecia Scotland and Lucas Eddy; and postdoctoral researchers Bing Deng and Zhe Yuan.
Suggested Items
Digital Twin Concept in Copper Electroplating Process Performance
07/11/2025 | Aga Franczak, Robrecht Belis, Elsyca N.V.PCB manufacturing involves transforming a design into a physical board while meeting specific requirements. Understanding these design specifications is crucial, as they directly impact the PCB's fabrication process, performance, and yield rate. One key design specification is copper thieving—the addition of “dummy” pads across the surface that are plated along with the features designed on the outer layers. The purpose of the process is to provide a uniform distribution of copper across the outer layers to make the plating current density and plating in the holes more uniform.
The Knowledge Base: A Conference for Cleaning and Coating of Mission-critical Electronics
07/08/2025 | Mike Konrad -- Column: The Knowledge BaseIn electronics manufacturing, there’s a dangerous misconception that cleaning and coating are standalone options, that they operate in different lanes, and that one can compensate for the other. Let’s clear that up now. Cleaning and conformal coating are not separate decisions. They are two chapters in the same story—the story of reliability.
SMT007 Magazine July—What’s Your Competitive Sweet Spot?
07/01/2025 | I-Connect007 Editorial TeamAre you in a niche that’s growing or shrinking? Is it time to reassess and refocus? We spotlight companies thriving by redefining or reinforcing their niche—what are their insights? In the July 2025 issue of SMT007 Magazine, we spotlight companies thriving by redefining or reinforcing their niche and offer insights to help you evaluate your own.
Smarter Machines Use AOI to Transform PCB Inspections
06/30/2025 | Marcy LaRont, PCB007 MagazineAs automated optical inspection (AOI) evolves from traditional end-of-process inspections to proactive, in-line solutions, the integration of AI and machine learning is revolutionizing defect reduction and enhancing yields, marking a pivotal shift in how quality is managed in manufacturing.
Magnalytix and Foresite to Host Technical Webinar on SIR Testing and Functional Reliability
06/26/2025 | MAGNALYTIXMagnalytix, in collaboration with Foresite Inc., is pleased to announce an upcoming one-hour Webinar Workshop titled “Comparing SIR IPC B-52 to Umpire 41 Functional & SIR Test Method.” This session will be held on July 24, 2025, and is open to professionals in electronics manufacturing, reliability engineering, and process development seeking insights into new testing standards for climatic reliability.