-
- News
- Books
Featured Books
- smt007 Magazine
Latest Issues
Current IssueWhat's Your Sweet Spot?
Are you in a niche that’s growing or shrinking? Is it time to reassess and refocus? We spotlight companies thriving by redefining or reinforcing their niche. What are their insights?
Moving Forward With Confidence
In this issue, we focus on sales and quoting, workforce training, new IPC leadership in the U.S. and Canada, the effects of tariffs, CFX standards, and much more—all designed to provide perspective as you move through the cloud bank of today's shifting economic market.
Intelligent Test and Inspection
Are you ready to explore the cutting-edge advancements shaping the electronics manufacturing industry? The May 2025 issue of SMT007 Magazine is packed with insights, innovations, and expert perspectives that you won’t want to miss.
- Articles
- Columns
- Links
- Media kit
||| MENU - smt007 Magazine
The EMS ‘State of the Union'
March 15, 2023 | Mark Laing, Siemens Digital Industries SoftwareEstimated reading time: 4 minutes
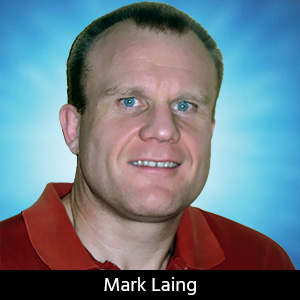
We recently heard President Biden’s State of the Union address, and it got me thinking that perhaps now is a good time to look at our own post-pandemic “state of the union” in the electronics manufacturing services industry. I will describe several key issues that our customers around the world are facing as we move forward into a new normal.
Accelerated High-mix Trend and Part Availability Constraints
One trend that appeared prior to COVID (but has accelerated since) is the increase in the number of unique products being built—the move to higher product mix and variety. Instead of a single product being built in a day, higher mix facilities are building several unique products with smaller production volumes. The line beat rate (Tact time of the line) becomes less important as the number of batches increases, and the changeover time becomes more significant.
The high-mix trend, together with supply chain issues, is driving a need for more agility in production schedules based on part availability. As product mix increases, part availability becomes a constraint to having unlimited agility to move from product to product.
Since companies are no longer able to acquire parts on demand as they did before the pandemic, they are forced to increase inventories and store components for future use. In addition, they are often driven to find alternative component sources, making the approved vendor lists (AVLs) more critical than ever. AVL management will also put additional pressure on communication channels between OEMs and EMS suppliers, as the initial AVL created by the OEM will need to be adjusted in real time based on actual component availability.
I also see further automation around component availability and purchasing as key to overcoming this challenge. There will be a movement toward component portals that deliver real-time data on stock levels and lead times for components rather than relying on manual methods that rely on human intervention. However, this is particularly challenging when it comes to semiconductors where AVLs focus mostly on passive and discrete components. Although simple logic devices can also form part of an AVL, it is the more complex components that are more specific, so less likely to have functional and fit replacements. Even if it is physically the same package, with the same number of pins, different pin outs can be common. It only takes one part to be unavailable to create the situation where the build can't be completed. This has led some OEMs to redesign products to remove dependencies on parts that are proving to be much harder to source. We have talked about design for manufacturing (DFM) for many years, but we may soon see specific designs being constantly adjusted for part availability. This will also contribute to the increase in higher-mix manufacturing.
Reshoring to the U.S.
Another trend is the reshoring of electronics manufacturing to the United States or Mexico and away from China and the Asia Pacific region. Obviously, the labor costs are higher in the U.S. compared to Asia-Pacific, so being able to build products efficiently in the U.S. requires more digitalization and automation. Being able to efficiently create a digital twin of the product once and then using that twin to create the requirements for each machine in the line to reduce duplicate effort will be key to increasing U.S.-based production. With the increases in product mix, being able to efficiently manage the changeovers will also be another critical element of U.S. manufacturing. Deeper partnerships between companies will be necessary to further integrate the different solutions needed to effectively manage higher mixes and their impact on changeovers. In practice this will mean earlier involvement for the EMS company with the OEM and getting more advanced notice of what will be needed. Maybe a footprint has been designed to only accept a single part but adjusting that a little allows another part to be substituted in its place. Now the EMS has a choice of two parts and either one will fit the board.
Further consequences of this reshoring will be the human resource requirements. Finding sufficient people to run a successful electronics assembly business, or any business for that matter, in the current economic climate is highly challenging. However, there are many incentives for companies to consider these paths. The recent U.S. Inflation Reduction Act affected how rebates for electric cars were calculated based on the amount of U.S.-sourced content. Although details are still being defined, expect to see other federal rebates being applied in similar ways to help drive more U.S. manufacturing.
Conclusion
Next year, IPC APEX EXPO moves back to Anaheim after several years in San Diego. My first one of these trade shows was in the mid-90s in Anaheim, so I see it as coming full circle after over 25 years attending the event (missing only that one COVID year). We still have many challenges ahead as we navigate the “new normal” but given our collective capability, I’m sure we will overcome them together.
Mark Laing is a business development manager for Siemens Digital Industries Software.
This article orginally appears in the March 2023 issue of SMT007 Magazine.
Suggested Items
Meet the Author Podcast: Martyn Gaudion Unpacks the Secrets of High-Speed PCB Design
07/10/2025 | I-Connect007In this special Meet the Author episode of the On the Line with… podcast, Nolan Johnson sits down with Martyn Gaudion, signal integrity expert, managing director of Polar Instruments, and three-time author in I-Connect007’s popular The Printed Circuit Designer’s Guide to... series.
Intervala Hosts Employee Car and Motorcycle Show, Benefit Nonprofits
08/27/2024 | IntervalaIntervala hosted an employee car and motorcycle show, aptly named the Vala-Cruise and it was a roaring success! Employees had the chance to show off their prized wheels, and it was incredible to see the variety and passion on display.
KIC Honored with IPC Recognition for 25 Years of Membership and Contributions to Electronics Manufacturing Industry
06/24/2024 | KICKIC, a renowned pioneer in thermal process and temperature measurement solutions for electronics manufacturing, is proud to announce that it has been recognized by IPC for 25 years of membership and significant contributions to electronics manufacturing.
Boeing Starliner Spacecraft Completes Successful Crewed Docking with International Space Station
06/07/2024 | BoeingNASA astronauts Barry "Butch" Wilmore and Sunita "Suni" Williams successfully docked Boeing's Starliner spacecraft to the International Space Station (ISS), about 26 hours after launching from Cape Canaveral Space Force Station.
KIC’s Miles Moreau to Present Profiling Basics and Best Practices at SMTA Wisconsin Chapter PCBA Profile Workshop
01/25/2024 | KICKIC, a renowned pioneer in thermal process and temperature measurement solutions for electronics manufacturing, announces that Miles Moreau, General Manager, will be a featured speaker at the SMTA Wisconsin Chapter In-Person PCBA Profile Workshop.