Challenges of DFM Analysis for Flex and Rigid-Flex Design, Part 3
June 14, 2023 | Mark Gallant, DownStream TechnologiesEstimated reading time: 2 minutes
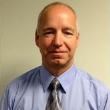
(Editor’s note: This is the final installment of a three-part series. To read Part 2, click here.)
What a True Rigid-flex DFM Analysis Solution Must Include
DFM analysis tools for the last several decades have focused on a typical rigid PCB or some variant. While many standard DFM constraints are applicable, flex has many unique requirements that cannot be addressed with typical DFM analysis. Flex and rigid-flex DFM must be targeted toward the unique materials and processes used to produce flex and rigid-flex designs.
One such example is board outline vs. layer profile. Some CAD systems do not support boundaries on a per layer basis. For most rigid-flex designs, all that is provided is a cumulative board outline that is the extent of all layer shapes. Without a defined boundary per layer, there may be no prevention of routing traces or placing components outside, or off of, a layer in the CAD system. The CAD DRC may also miss these items because they are within the boundary of the cumulative board outline. Having a DFM tool capable of analyzing each layer against its unique profile can detect when conductors are outside, or off of, their respective layers.
Here is a categorized list of the types of analyses and features a flex or rigid-flex DFM tool should have.
1. Trace fracture
Trace or copper fracture in bend areas. Some examples include presence of trace corners, width transitions, or traces non-perpendicular to the bend axis in a bend area. Also, I-beaming where traces are coincident on adjacent flexible layers.
2. Delamination
Pads or vias in bend areas with improper pad shapes or coverlay exposures. When it is required to have vias or other pads in bend areas, special care must be taken when designing the coverlay to reduce delamination potential. Often in these conditions, the coverlay overlaps the pad area to prevent delamination. In other designs, pads are adorned with tabs to extend under the coverlay.
3. Tearing
The absence of tear stops on slits or inside corners. Copper segments, arcs, circles, or other shapes are added to prevent tear around slits or inside corners.
4. Squeeze out
Epoxy leakage onto adjacent copper or other layer surfaces. In order to prevent epoxy squeeze out, a perimeter air gap or fence must be present around adjacent layer content. For example, a larger annular ring may be required on the epoxy layer than its corresponding coverlay annular ring. This prevents epoxy from squeezing out onto adjacent copper or traces.
5. Button plating
Absence of exposures in coverlay for vias. The most common method of plating vias in a bend area is button plating. This requires vias to be plated have an exposure on their adjacent coverlay. Absence of an exposure on the coverlay would prevent plating.
To read this entire article, which appeared in the June 2023 issue of Design007 Magazine, click here.
Suggested Items
The Evolution of Picosecond Laser Drilling
06/19/2025 | Marcy LaRont, PCB007 MagazineIs it hard to imagine a single laser pulse reduced not only from nanoseconds to picoseconds in its pulse duration, but even to femtoseconds? Well, buckle up because it seems we are there. In this interview, Dr. Stefan Rung, technical director of laser machines at Schmoll Maschinen GmbH, traces the technology trajectory of the laser drill from the CO2 laser to cutting-edge picosecond and hybrid laser drilling systems, highlighting the benefits and limitations of each method, and demonstrating how laser innovations are shaping the future of PCB fabrication.
Day 2: More Cutting-edge Insights at the EIPC Summer Conference
06/18/2025 | Pete Starkey, I-Connect007The European Institute for the PCB Community (EIPC) summer conference took place this year in Edinburgh, Scotland, June 3-4. This is the third of three articles on the conference. The other two cover Day 1’s sessions and the opening keynote speech. Below is a recap of the second day’s sessions.
Day 1: Cutting Edge Insights at the EIPC Summer Conference
06/17/2025 | Pete Starkey, I-Connect007The European Institute for the PCB Community (EIPC) Summer Conference took place this year in Edinburgh, Scotland, June 3-4. This is the second of three articles on the conference. The other two cover the keynote speeches and Day 2 of the technical conference. Below is a recap of the first day’s sessions.
Preventing Surface Prep Defects and Ensuring Reliability
06/10/2025 | Marcy LaRont, PCB007 MagazineIn printed circuit board (PCB) fabrication, surface preparation is a critical process that ensures strong adhesion, reliable plating, and long-term product performance. Without proper surface treatment, manufacturers may encounter defects such as delamination, poor solder mask adhesion, and plating failures. This article examines key surface preparation techniques, common defects resulting from improper processes, and real-world case studies that illustrate best practices.
RF PCB Design Tips and Tricks
05/08/2025 | Cherie Litson, EPTAC MIT CID/CID+There are many great books, videos, and information online about designing PCBs for RF circuits. A few of my favorite RF sources are Hans Rosenberg, Stephen Chavez, and Rick Hartley, but there are many more. These PCB design engineers have a very good perspective on what it takes to take an RF design from schematic concept to PCB layout.