-
- News
- Books
Featured Books
- pcb007 Magazine
Latest Issues
Current IssueSales: From Pitch to PO
From the first cold call to finally receiving that first purchase order, the July PCB007 Magazine breaks down some critical parts of the sales stack. To up your sales game, read on!
The Hole Truth: Via Integrity in an HDI World
From the drilled hole to registration across multiple sequential lamination cycles, to the quality of your copper plating, via reliability in an HDI world is becoming an ever-greater challenge. This month we look at “The Hole Truth,” from creating the “perfect” via to how you can assure via quality and reliability, the first time, every time.
In Pursuit of Perfection: Defect Reduction
For bare PCB board fabrication, defect reduction is a critical aspect of a company's bottom line profitability. In this issue, we examine how imaging, etching, and plating processes can provide information and insight into reducing defects and increasing yields.
- Articles
- Columns
- Links
- Media kit
||| MENU - pcb007 Magazine
Estimated reading time: 1 minute
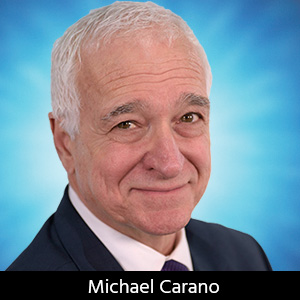
Contact Columnist Form
Achieving Fine Lines and Spaces, Part 2
Achieving high yields with fine lines and spaces requires a good understanding of surface preparation methods. These include pumice and chemical cleaning. In essence, the surface profile of roughness plays a role in resist adhesion.
Pumice vs. Chemical Cleaning
As someone who has frequently worked with PCB fabricators on a global basis, I must confess that surface preparation and imaging issues rank quite high on the list of yield loss. In previous columns, I have stressed the basic fundamentals. That is, understand what you are up against (which soils are on the surface, what are the interactions of the process parameters, etc.) in order to optimize yields. As stated previously, in order to minimize distortion and material stretching, mechanical methods of surface preparation are giving way to chemical cleaning. Copper foils and are also trending toward lower thicknesses in order to improve fine-line etching. Secondly, the need to improve impedance control with today’s high-speed electrical requirements is driving the implementation of low profile copper foil. These lower-profile foils are generally of a finer grain size, further impacting the ability to affect a surface topography sufficient to enhance photoresist adhesion. So let’s first review the importance of surface topography and photoresist adhesion.
Critical Surface Profile Parameters
I stated earlier that poor resist adhesion leading to defects such as opens or shorts, peeling and interfacial voids, are related to numerous issues including, surface preparation, characteristics of the copper foil, lamination parameters, and the formulation of the photoresist itself. There are other causes of poor adhesion that are directly attributable to other factors such as developing and exposure. These causes will be explored in a future column. With respect to surface topography, I already stated that the randomness of the copper topography after surface prep is more beneficial than a unidirectional one seen with mechanical scrubbing. Pumice, aluminum oxide, and chemical clean impart the random or multidirectional topography that we are concerned with. While that is a good thing, let’s take a close look at critical profile or topographical parameters.
Read the full column here.
Editor's Note: This column originally appeared in the December 2013 issue of The PCB Magazine.
More Columns from Trouble in Your Tank
Trouble in Your Tank: Can You Drill the Perfect Hole?Trouble in Your Tank: Yield Improvement and Reliability
Trouble in Your Tank: Causes of Plating Voids, Pre-electroless Copper
Trouble in Your Tank: Organic Addition Agents in Electrolytic Copper Plating
Trouble in Your Tank: Interconnect Defect—The Three Degrees of Separation
Trouble in Your Tank: Things You Can Do for Better Wet Process Control
Trouble in Your Tank: Processes to Support IC Substrates and Advanced Packaging, Part 5
Trouble in Your Tank: Materials for PWB Fabrication—Drillability and Metallization