-
- News
- Books
Featured Books
- smt007 Magazine
Latest Issues
Current IssueMoving Forward With Confidence
In this issue, we focus on sales and quoting, workforce training, new IPC leadership in the U.S. and Canada, the effects of tariffs, CFX standards, and much more—all designed to provide perspective as you move through the cloud bank of today's shifting economic market.
Intelligent Test and Inspection
Are you ready to explore the cutting-edge advancements shaping the electronics manufacturing industry? The May 2025 issue of SMT007 Magazine is packed with insights, innovations, and expert perspectives that you won’t want to miss.
Do You Have X-ray Vision?
Has X-ray’s time finally come in electronics manufacturing? Join us in this issue of SMT007 Magazine, where we answer this question and others to bring more efficiency to your bottom line.
- Articles
- Columns
- Links
- Media kit
||| MENU - smt007 Magazine
How to Streamline PCB Thermal Design
April 1, 2015 | John Parry, Mentor Graphics CorporationEstimated reading time: 2 minutes
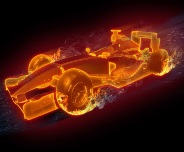
Thermal issues with a PCB design are mostly determined during the component selection and layout phases. After this point, only remedial actions are possible if components are found to run too hot. Addressing thermal issues early in PCB design, starting at the system or enclosure level to understand the flow environment critical for air-cooled electronics, can streamline the process. Assumptions about the airflow uniformity in early design that subsequently prove unachievable can have a disastrous effect on the commercial viability of the product and meeting the market window.
Begin Before Placement and Layout
Substantial work can be done well before layout is completed within the electrical design flow. A simple representation of the enclosure can provide information about the air flow profile over the board. Start by smearing the total board power over the total board surface, which will provide a temperature map that will show any hot regions that are caused by a badly distributed air flow. Treat the board as a block with an isotropic conductivity of between 5 W/mK and 10 W/mK to optimize enclosure-level air flow ahead of the PCB design.
Components inject heat locally into the board so the heat flux density into the board below a component will be higher than the average for the board. As a result, the local board temperature will be higher than that predicted in the simulation. Refine the model before using the board temperature to estimate component temperatures. If the board temperature at any point is close to the maximum component case temperature, this limit will be exceeded once the component heat sources are represented discretely.
Guesstimate Component Power
At this stage, make a best-guess estimate of the individual power budgets for the main heat dissipating components that will be used in the design and the approximate size of those packages. This will enable describing them as footprint heat sources in the simulation, smearing the remainder of heat uniformly over the board surface.
Before Selecting the Package, Use 3D Component Models
Include some form of 3D component model in the simulation before the component selection is finalized. By feeding the thermal results back before this milestone is reached, the thermal performance will more likely be considered in the package selection criteria. Some ICs are available in more than one package style, and not all package styles perform equally well from a thermal point of view. The need for a heatsink later may be eliminated by appropriate package selection.
Component temperature, either in the form of a case temperature or junction temperature depending on how the manufacturer has specified the component, is the key measure used to indicate whether the design is thermally acceptable.
Editor's Note: This article originally appeared in the March issue of SMT Magazine.
Suggested Items
DownStream Acquisition Fits Siemens’ ‘Left-Shift’ Model
06/26/2025 | Andy Shaughnessy, I-Connect007I recently spoke to DownStream Technologies founder Joe Clark about the company’s acquisition by Siemens. We were later joined by A.J. Incorvaia, Siemens’ senior VP of electronic board systems. Joe discussed how he, Rick Almeida, and Ken Tepper launched the company in the months after 9/11 and how the acquisition came about. A.J. provides some background on the acquisition and explains why the companies’ tools are complementary.
Elementary Mr. Watson: Retro Routers vs. Modern Boards—The Silent Struggle on Your Screen
06/26/2025 | John Watson -- Column: Elementary, Mr. WatsonThere's a story about a young woman preparing a holiday ham. Before putting it in the pan, she cuts off the ends. When asked why, she shrugs and says, "That's how my mom always did it." She asks her mother, who gives the same answer. Eventually, the question reaches Grandma, who laughs and says, "Oh, I only cut the ends off because my pan was too small." This story is a powerful analogy for how many PCB designers approach routing today.
Siemens Turbocharges Semiconductor and PCB Design Portfolio with Generative and Agentic AI
06/24/2025 | SiemensAt the 2025 Design Automation Conference, Siemens Digital Industries Software today unveiled its AI-enhanced toolset for the EDA design flow.
Cadence AI Autorouter May Transform the Landscape
06/19/2025 | Andy Shaughnessy, Design007 MagazinePatrick Davis, product management director with Cadence Design Systems, discusses advancements in autorouting technology, including AI. He emphasizes a holistic approach that enhances placement and power distribution before routing. He points out that younger engineers seem more likely to embrace autorouting, while the veteran designers are still wary of giving up too much control. Will AI help autorouters finally gain industry-wide acceptance?
Beyond Design: The Metamorphosis of the PCB Router
06/18/2025 | Barry Olney -- Column: Beyond DesignThe traditional PCB design process is often time-consuming and labor-intensive. Routing a complex PCB layout can consume up to 30% of a designer’s time, and addressing this issue is not straightforward. We have all encountered this scenario: You spend hours setting the constraints and finally hit the Go button, only to be surprised by the lack of visual appeal and the obvious flaws in the result.