-
- News
- Books
Featured Books
- smt007 Magazine
Latest Issues
Current IssueMoving Forward With Confidence
In this issue, we focus on sales and quoting, workforce training, new IPC leadership in the U.S. and Canada, the effects of tariffs, CFX standards, and much more—all designed to provide perspective as you move through the cloud bank of today's shifting economic market.
Intelligent Test and Inspection
Are you ready to explore the cutting-edge advancements shaping the electronics manufacturing industry? The May 2025 issue of SMT007 Magazine is packed with insights, innovations, and expert perspectives that you won’t want to miss.
Do You Have X-ray Vision?
Has X-ray’s time finally come in electronics manufacturing? Join us in this issue of SMT007 Magazine, where we answer this question and others to bring more efficiency to your bottom line.
- Articles
- Columns
- Links
- Media kit
||| MENU - smt007 Magazine
Time to Ditch Heavy Metal for Soft Rock?
April 8, 2015 | Yash Sutariya and Thomas TarterEstimated reading time: 3 minutes
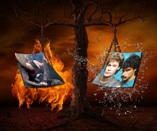
I've been writing on thermal management for LED applications for a few years now, seemingly on an endless quest to find the next best thing for LED PCBs. It's been kind of like Indiana Jones and his search for the Holy Grail, except I don't have cool bullwhip skills. To date, we've focused on calculating thermal management needs as well as explore other alternatives to MCPCBs to achieve thermal management, such as standard plated through holes in FR4 material. I'd say at this point the industry has reached a saturation point when it comes to knowledge on how to dissipate heat (of course you never know what’s around the corner).
I think now it's time to move on to a topic that we've overlooked when it comes to PCBs for LEDs: reliability! I think the reason we've overlooked reliability is because it is traditionally associated with via life under thermal cycling conditions. Since most LED PCBs are single sided, this really hasn't been an issue. However, if you look above the waterline, there is another weak link—the solder joint. Some OEMs in the industry have been performing studies on the life of their LED products. While the bulbs themselves are said to have useful lives in excess of 30+ years, they are finding out that the actual LED assemblies can fail in as little as 5–6 years. Initial analysis is pointing to the significant X and Y axes CTE differences between the solder joint, copper circuitry layer, thermally conductive dielectric, and the aluminum. The net result of the CTE differences is a shear effect being created that can eventually disrupt the solder joint, which results in operational failure.
Depending upon how accurate this information is, it could mean the start of a whole new approach to PCBs for LED applications. Below is an abstract of a white paper written by Thomas Tarter from Package Science Services, which performed initial testing on carbon fiber and graphite based materials provided by Stablcor Technology Inc. The carbon fiber constraining cores (CFCC) materials evaluated are carbon-fiber and/or graphite reinforced epoxy cores to aid in heat dissipation, rigidity, weight reduction, and CTE control. These cores can be used independently or in conjunction with current MCPCBs to produce functionally improved heat dissipation while reducing the CTE mismatch currently present on LED assemblies.
Abstract: Introduction and Model Parameters (by Thomas Tarter)
Thermal performance for PCB structures are investigated in the form of steady-state finite element models of various stack-ups of commonly used materials for LED applications. The models show the effect of materials used in the stack up including FR-4, aluminum, copper, graphite and CFCC. The goal of the study is to compare relative thermal behavior of typical boards modified with the enhanced core materials.
The materials are inserted into standard PCB stack-up configurations as an added or replaced layer. Models are solved for maximum temperature on a 25 mm x 25 mm coupon with a 2 mm x 2 mm-square heat source. The stack up resembles substrates known as "metal-clad" where the dielectric and topside copper are laminated directly onto a metal substrate. In addition, FR4 boards are used as a worst-case comparison.
Variables used in the study include material properties and layer thickness. The primary variables are top side copper thickness/weight, dielectric thickness and base material thickness. Table 1 lists the ranges for geometry and material properties. The heat source is simulated as a planar load, directly on the surface of the top-layer copper. One watt is applied over a 2mm x 2 mm square area in the center of the coupon. The models are solved in natural convection with an ambient temperature of 30°C.
Editor's Note: This article originally appeared in the March issue of SMT Magazine.
Suggested Items
Hands-On Demos Now Available for Apollo Seiko’s EF and AF Selective Soldering Lines
06/30/2025 | Apollo SeikoApollo Seiko, a leading innovator in soldering technology, is excited to spotlight its expanded lineup of EF and AF Series Selective Soldering Systems, now available for live demonstrations in its newly dedicated demo room.
Indium Corporation Expert to Present on Automotive and Industrial Solder Bonding Solutions at Global Electronics Association Workshop
06/26/2025 | IndiumIndium Corporation Principal Engineer, Advanced Materials, Andy Mackie, Ph.D., MSc, will deliver a technical presentation on innovative solder bonding solutions for automotive and industrial applications at the Global Electronics A
Fresh PCB Concepts: Assembly Challenges with Micro Components and Standard Solder Mask Practices
06/26/2025 | Team NCAB -- Column: Fresh PCB ConceptsMicro components have redefined what is possible in PCB design. With package sizes like 01005 and 0201 becoming more common in high-density layouts, designers are now expected to pack more performance into smaller spaces than ever before. While these advancements support miniaturization and functionality, they introduce new assembly challenges, particularly with traditional solder mask and legend application processes.
Knocking Down the Bone Pile: Tin Whisker Mitigation in Aerospace Applications, Part 3
06/25/2025 | Nash Bell -- Column: Knocking Down the Bone PileTin whiskers are slender, hair-like metallic growths that can develop on the surface of tin-plated electronic components. Typically measuring a few micrometers in diameter and growing several millimeters in length, they form through an electrochemical process influenced by environmental factors such as temperature variations, mechanical or compressive stress, and the aging of solder alloys.
SolderKing’s Successful Approach to Modern Soldering Needs
06/18/2025 | Nolan Johnson, I-Connect007Chris Ward, co-founder of the family-owned SolderKing, discusses his company's rapid growth and recent recognition with the King’s Award for Enterprise. Chris shares how SolderKing has achieved these award-winning levels of service in such a short timeframe. Their secret? Being flexible in a changing market, technical prowess, and strong customer support.