-
- News
- Books
Featured Books
- smt007 Magazine
Latest Issues
Current IssueMoving Forward With Confidence
In this issue, we focus on sales and quoting, workforce training, new IPC leadership in the U.S. and Canada, the effects of tariffs, CFX standards, and much more—all designed to provide perspective as you move through the cloud bank of today's shifting economic market.
Intelligent Test and Inspection
Are you ready to explore the cutting-edge advancements shaping the electronics manufacturing industry? The May 2025 issue of SMT007 Magazine is packed with insights, innovations, and expert perspectives that you won’t want to miss.
Do You Have X-ray Vision?
Has X-ray’s time finally come in electronics manufacturing? Join us in this issue of SMT007 Magazine, where we answer this question and others to bring more efficiency to your bottom line.
- Articles
- Columns
- Links
- Media kit
||| MENU - smt007 Magazine
How to Select an Automatic Pick-and-Place Machine
April 15, 2015 | Robert Voigt, DDM NovastarEstimated reading time: 2 minutes
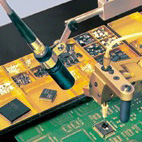
This is the third in a series of articles designed to help buyers analyze and select SMT equipment for PCB assembly, and examines automatic pick-and-place machines, the most complex component in a circuit assembly operation. Because of this complexity, the next few columns will address different functions in this process.
Automatic pick-and-place machines are much more common than manual or semiautomatic machines, but they also have the greatest range of capabilities and cost. This column will focus on features and capabilities and include some cautions regarding reliability of low-cost machines, including:
• Production volume ranges (CPH)
• Accuracy and repeatability specs
• Pick-up and centering methods
In future columns, I will address size, machine accuracy, encoders, feeders and mechanical positioning methods.
When starting your evaluation process, there are two defining factors to keep in mind, which determine what category fits your machine needs. The No. 1 principal factor is components per hour (CPH), and the secondary factor is machine capability.
Production Volume
As in the previous column, it’s constructive to start by addressing production ranges for various types of machines, since this is the No. 1 factor in your evaluation process. For purposes of comparison, since all circuit boards vary in size and complexity, we talk about volumes in terms of components per hour, or CPH. The following table offers a general guideline of machine categories defined by their CPH.
Machine Capabilities
This is the second defining factor in helping choose the correct auto pick-and-place machine for your needs. Here, we will only be talking about two aspects of machine capability: accuracy and repeatability, and pick-and-place centering methods.
Accuracy and Repeatability
For production machines, we typically recommend looking for a machine with accuracy of +/- .0001” and down to fine pitch capability of 12 mil on a repeated basis. Less expensive machines often don’t meet this spec. Most low-cost machines will also not come standard with a computer or software which could help with the repeatability aspects if not the accuracy. While some may offer enhanced technology, most do not.
Pick-and-place Centering Methods
There are four methods for pick-up and placement:
1. No centering mechanism
2. Mechanical (jaws)
3. Laser centering
4. Vision centering
Method 1: No centering mechanism other than relying on the component’s pick-up point for placement. In other words, the part is not physically centered after being picked up by the tool head, and if it’s picked off-center on the tool, it will be off-center when placed on the board. Obviously, this is not a very accurate placement method because there is no definable tolerance. You can expect to find this method used by hobbyists or instructors, but certainly not in any type of precision production environment. There are not many options available either, and long-term reliability is questionable.
• Pros: Low cost
• Cons: Low accuracy, repeatability and long-term reliability, no options, or spare parts
• Size range: No definable tolerances
Editor's Note: This article originally appeared in the March issue of SMT Magazine.
Suggested Items
WellPCB, OurPCB Launch Low-Cost PCB Assembly and Custom Cable Assembly Solutions
05/29/2025 | ACCESSWIREWellPCB and OurPCB, world leading PCB manufacturing service providers, announced today that they have officially launched new Low-Cost PCB Assembly Solutions and Custom Cable Assembly services to meet the needs of the electronics manufacturing industry for high cost performance and flexible customization.
Electronics Industry Demand Holds Steady Amid Tariff Turbulence
05/22/2025 | IPCElectronics manufacturers are bracing for higher costs as profit pressures deepen according to IPC’s May Sentiment of the Global Electronics Manufacturing Supply Chain Report.
LitePoint, Pegatron 5G Successfully Launch Volume Manufacturing of 5G O-RAN Radio Units to Power Private 5G Networks
05/21/2025 | BUSINESS WIRELitePoint, a leading provider of wireless test solutions, and Pegatron 5G, a leading provider of end-to-end 5G product solutions, have jointly announced a milestone in their collaboration; the start of high-volume manufacturing for 5G O-RAN radio units.
Fresh PCB Concepts: The Power of a Lunch & Learn for PCB Professionals
05/15/2025 | Team NCAB -- Column: Fresh PCB ConceptsIn the electronics industry, innovation isn’t simply a competitive edge, it’s a survival strategy. For those working in printed circuit board (PCB) design, engineering, procurement, and quality control, staying informed and connected is key to creating high-performance, cost-effective, and manufacturable products. Enter the Lunch & Learn—a simple yet highly effective format for professional development offering technical insights in short, informal sessions (served with lunch).
Localized Automation Becomes a Tariff Storm Safe Haven, but U.S. Smart Factory Build-Out Costs Far Exceed China’s
05/09/2025 | TrendForceTrendForce’s latest “Human-Machine Technology Report” points out that although the 90-day delay on the U.S. reciprocal tariffs announced by the Trump administration in early April 2025 offers temporary relief, it has already triggered lasting shifts in global manufacturing and supply chain strategies.