Flexible Circuit Materials for High-Temperature Applications
June 9, 2015 | Sidney Cox, DuPont Circuit and Packaging MaterialsEstimated reading time: 1 minute
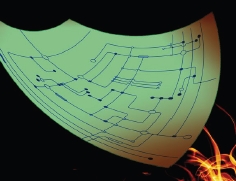
Abstract
Many opportunities exist for flexible circuits in high-temperature applications (automotive, military, aerospace, oil and gas). Flex circuits in these applications have been hindered by a lack of materials that can survive higher temperatures. Some materials, especially some thermoset adhesives, break down over time at higher temperature, becoming brittle or losing adhesion to copper. Polyimides tend to perform much better under high temperature.
The other issue is the lack of good test methods to verify that flex materials can survive higher temperatures. Several methods for testing copper clad laminates exist, but there are very few for coverlays and bondplies. We will discuss different test methods for measuring high-temperature capability including the new IPC service temperature test. We will also report on test results for various flexible materials and our recommendations for the best flexible materials for high temperature applications. This will include development work on new flex materials for high-temperature applications.
Introduction
More applications require flexible circuits that must survive high-temperature environments. These include automotive applications near the engine, oil and gas down-hole pumps, and aerospace applications near jet engines. There have been limited test methods to determine what temperatures flexible materials can survive.
The damage caused by high-temperature environments will mainly fall in three categories: loss of adhesion between copper and dielectric, loss of adhesion between dielectric layers, and embrittlement of the dielectric layers. At the highest temperatures the copper would also become brittle, but in most cases the flexible circuit dielectrics fail first. Thermoset adhesives seem to be most sensitive to embrittlement especially compared to polyimide films which are much more resistant to high temperatures.
Read the full article here.
Editor's Note: This article originally appeared in the June 2015 issue of The PCB Magazine.
Suggested Items
The Evolution of Picosecond Laser Drilling
06/19/2025 | Marcy LaRont, PCB007 MagazineIs it hard to imagine a single laser pulse reduced not only from nanoseconds to picoseconds in its pulse duration, but even to femtoseconds? Well, buckle up because it seems we are there. In this interview, Dr. Stefan Rung, technical director of laser machines at Schmoll Maschinen GmbH, traces the technology trajectory of the laser drill from the CO2 laser to cutting-edge picosecond and hybrid laser drilling systems, highlighting the benefits and limitations of each method, and demonstrating how laser innovations are shaping the future of PCB fabrication.
Day 2: More Cutting-edge Insights at the EIPC Summer Conference
06/18/2025 | Pete Starkey, I-Connect007The European Institute for the PCB Community (EIPC) summer conference took place this year in Edinburgh, Scotland, June 3-4. This is the third of three articles on the conference. The other two cover Day 1’s sessions and the opening keynote speech. Below is a recap of the second day’s sessions.
Day 1: Cutting Edge Insights at the EIPC Summer Conference
06/17/2025 | Pete Starkey, I-Connect007The European Institute for the PCB Community (EIPC) Summer Conference took place this year in Edinburgh, Scotland, June 3-4. This is the second of three articles on the conference. The other two cover the keynote speeches and Day 2 of the technical conference. Below is a recap of the first day’s sessions.
Preventing Surface Prep Defects and Ensuring Reliability
06/10/2025 | Marcy LaRont, PCB007 MagazineIn printed circuit board (PCB) fabrication, surface preparation is a critical process that ensures strong adhesion, reliable plating, and long-term product performance. Without proper surface treatment, manufacturers may encounter defects such as delamination, poor solder mask adhesion, and plating failures. This article examines key surface preparation techniques, common defects resulting from improper processes, and real-world case studies that illustrate best practices.
RF PCB Design Tips and Tricks
05/08/2025 | Cherie Litson, EPTAC MIT CID/CID+There are many great books, videos, and information online about designing PCBs for RF circuits. A few of my favorite RF sources are Hans Rosenberg, Stephen Chavez, and Rick Hartley, but there are many more. These PCB design engineers have a very good perspective on what it takes to take an RF design from schematic concept to PCB layout.