-
- News
- Books
Featured Books
- pcb007 Magazine
Latest Issues
Current IssueThe Hole Truth: Via Integrity in an HDI World
From the drilled hole to registration across multiple sequential lamination cycles, to the quality of your copper plating, via reliability in an HDI world is becoming an ever-greater challenge. This month we look at “The Hole Truth,” from creating the “perfect” via to how you can assure via quality and reliability, the first time, every time.
In Pursuit of Perfection: Defect Reduction
For bare PCB board fabrication, defect reduction is a critical aspect of a company's bottom line profitability. In this issue, we examine how imaging, etching, and plating processes can provide information and insight into reducing defects and increasing yields.
Voices of the Industry
We take the pulse of the PCB industry by sharing insights from leading fabricators and suppliers in this month's issue. We've gathered their thoughts on the new U.S. administration, spending, the war in Ukraine, and their most pressing needs. It’s an eye-opening and enlightening look behind the curtain.
- Articles
- Columns
- Links
- Media kit
||| MENU - pcb007 Magazine
Characterization of PCB Material & Manufacturing Technology for High-Frequency
September 2, 2015 | E. Schlaffer, AT&S; and O. Huber, T. Faseth, and H. Arthaber, University of Technology, ViennaEstimated reading time: 15 minutes
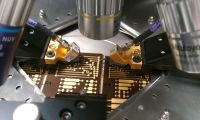
Abstract
Today's electronics industry is changing at a rapid pace. The root causes are manifold. The world population is growing toward eight billion, which gives rise to new challenges in terms of urbanization, mobility and connectivity. Consequently, numerous new business models for the electronic industry will develop. Connectivity will influence our lives more than ever. Concepts like Industry 4.0, Internet of Things, M2M communication, smart homes and communication in, or to cars are maturing. All these applications are based on the same demanding requirement—a considerable amount of data and increased data transfer rate. These arguments present major challenges to PCB design and manufacturing.
This paper investigates the impact of different PCB manufacturing technologies and their relation to high-frequency behavior. In the course of the paper a brief overview of PCB manufacturing capabilities will be presented. Moreover, signal losses in terms of frequency, design, manufacturing processes, and substrate materials are investigated. The aim of this paper is to develop a concept to use materials in combination with optimized PCB manufacturing processes, which allows a significant reduction of losses and increased signal quality.
First analysis demonstrates that for increased signal frequency, demanded by growing data transfer rate, the capabilities to manufacture high-frequency PCBs become a key factor in terms of losses. Base materials with particularly high-speed properties like very low dielectric constants are used for efficient design of high-speed data link lines. Furthermore, copper foils with very low treatment are to be used to minimize loss caused by the skin effect. In addition to the materials composition, the design of high-speed circuits is optimized with the help of comprehensive simulation studies.
The work on this paper focuses on requirements and main questions arising during the PCB manufacturing process in order to improve the system in terms of losses. For that matter, there are several approaches that can be used. For example, the optimization of the structuring process, the use of efficient interconnection capabilities, and dedicated surface finishing can be used to reduce losses and preserve signal integrity.
In this study, a comparison of different PCB manufacturing processes by using measurement results of demonstrators that imitate real PCB applications will be discussed. Special attention will be drawn to the manufacturing capabilities that are optimized for high-frequency requirements and focused to avoid signal loss. Different line structures like microstrip lines, coplanar waveguides, and surface integrated waveguides are used for this assessment.
This research was carried out by Austria Technologie & Systemtechnik AG (AT&S AG), in cooperation with Vienna University of Technology, Institute of Electrodynamics, Microwave and Circuit Engineering.
Introduction
Several commercially available PCB fabrication processes exist for manufacturing PCBs. In this paper two methods, pattern plating and panel plating, were utilized for manufacturing the test samples.
The first step in both described manufacturing processes is drilling, which allows connections between different copper layers. The second step for pattern plating (see figure 1) is the flash copper plating process, wherein only a thin copper skin (flash copper) is plated into the drilled holes and over the entire surface. On top of the plated copper a layer of photosensitive etch resist is laminated which is subsequently imaged by ultraviolet (UV) light using a negative film. Negative film imaging is exposing the gaps in between the traces to the UV light. In developing process the non-exposed dry film is removed with a sodium solution. After that, the whole surrounding space is plated with copper and eventually covered by tin. The tin layer protects the actual circuit pattern during etching. The pattern plating process shows typically a smaller line-width tolerance, compared to panel plating, because of a lower copper thickness before etching. The overall process tolerance for narrow dimensions in the order of several tenths of µm is approximately ± 10%.
Figure 1 (left) - Pattern plating; Figure 2 (right) - panel plating.
The second typical PCB manufacturing process is panel plating (see Figure 2). In this process, after drilling, the entire panel is plated with copper. On top of the plated copper a layer of photosensitive etch resist is laminated. After that, there is positive film imaging, whereby the actual circuit pattern is exposed to UV light. After developing, the copper is etched with a chemical wet process and in the last step the etch resist is removed and the copper structure is finished. It should be noted that in panel plating the etching is applied on the whole thickness of plated copper and copper foil. During panel plating the copper thickness varies up to ± 3% only, because of the uniform plating method. However, the distribution of the etching solution on the surface is unequal; a lower exchange of etching solution and copper occurs in the center and somewhat more on the edges of a production panel. This is called “puddling effect.” The consequences are wider lines in the center and narrower lines at the edges of each panel. The overall process tolerance for narrow dimensions in the order of several tenths of µm is approximately ± 20%.
Page 1 of 5
Suggested Items
Copper Price Surge Raises Alarms for Electronics
07/15/2025 | Global Electronics Association Advocacy and Government Relations TeamThe copper market is experiencing major turbulence in the wake of U.S. President Donald Trump’s announcement of a 50% tariff on imported copper effective Aug. 1. Recent news reports, including from the New York Times, sent U.S. copper futures soaring to record highs, climbing nearly 13% in a single day as manufacturers braced for supply shocks and surging costs.
I-Connect007 Editor’s Choice: Five Must-Reads for the Week
07/11/2025 | Andy Shaughnessy, Design007 MagazineThis week, we have quite a variety of news items and articles for you. News continues to stream out of Washington, D.C., with tariffs rearing their controversial head again. Because these tariffs are targeted at overseas copper manufacturers, this news has a direct effect on our industry.I-Connect007 Editor’s Choice: Five Must-Reads for the Week
Digital Twin Concept in Copper Electroplating Process Performance
07/11/2025 | Aga Franczak, Robrecht Belis, Elsyca N.V.PCB manufacturing involves transforming a design into a physical board while meeting specific requirements. Understanding these design specifications is crucial, as they directly impact the PCB's fabrication process, performance, and yield rate. One key design specification is copper thieving—the addition of “dummy” pads across the surface that are plated along with the features designed on the outer layers. The purpose of the process is to provide a uniform distribution of copper across the outer layers to make the plating current density and plating in the holes more uniform.
Trump Copper Tariffs Spark Concern
07/10/2025 | I-Connect007 Editorial TeamPresident Donald Trump stated on July 8 that he plans to impose a 50% tariff on copper imports, sparking concern in a global industry whose output is critical to electric vehicles, military hardware, semiconductors, and a wide range of consumer goods. According to Yahoo Finance, copper futures climbed over 2% following tariff confirmation.
Happy’s Tech Talk #40: Factors in PTH Reliability—Hole Voids
07/09/2025 | Happy Holden -- Column: Happy’s Tech TalkWhen we consider via reliability, the major contributing factors are typically processing deviations. These can be subtle and not always visible. One particularly insightful column was by Mike Carano, “Causes of Plating Voids, Pre-electroless Copper,” where he outlined some of the possible causes of hole defects for both plated through-hole (PTH) and blind vias.