-
- News
- Books
Featured Books
- pcb007 Magazine
Latest Issues
Current IssueThe Hole Truth: Via Integrity in an HDI World
From the drilled hole to registration across multiple sequential lamination cycles, to the quality of your copper plating, via reliability in an HDI world is becoming an ever-greater challenge. This month we look at “The Hole Truth,” from creating the “perfect” via to how you can assure via quality and reliability, the first time, every time.
In Pursuit of Perfection: Defect Reduction
For bare PCB board fabrication, defect reduction is a critical aspect of a company's bottom line profitability. In this issue, we examine how imaging, etching, and plating processes can provide information and insight into reducing defects and increasing yields.
Voices of the Industry
We take the pulse of the PCB industry by sharing insights from leading fabricators and suppliers in this month's issue. We've gathered their thoughts on the new U.S. administration, spending, the war in Ukraine, and their most pressing needs. It’s an eye-opening and enlightening look behind the curtain.
- Articles
- Columns
- Links
- Media kit
||| MENU - pcb007 Magazine
Catching up with PNC
November 11, 2015 | Dan Beaulieu, D.B. Management GroupEstimated reading time: 13 minutes
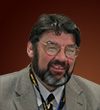
PNC, headquartered in Nutley, New Jersey, is a unique company. Started in 1968, and then taken over by Sam Sangani in 1996, it has evolved into one of the premier PCB companies on the East Coast, if not the country. Over the years, the company has grown to the point where it now offers circuit design, layout, fabrication and assembly to its customers, making it one of the few total concept under one roof companies in North America.
If there is one word that sums up the company’s philosophy, that word would be convenience. They strive to be as convenient as possible to their customers, always making sure that they are providing their customers with everything they need to succeed. Recently, I had the opportunity to talk to Calvin Switzer, VP of PNC.
Dan Beaulieu: Calvin, tell me a little bit about the company.
Calvin Switzer: The company was actually started in 1968 by a gentleman named Rene Gabbai, and then in 1996 we bought the company. We saw an opportunity with the current business of original ownership and felt we could increase business by studying each process and upgrading them systematically to increase our technology with new equipment.
Our vision was to become one of, if not the best printed circuit board shops in the Northeast, which we feel we have achieved. Since then, our vision has changed slightly by integrating a circuit design, started in 2004, and assembly division, begun in 2010. These changes were driven by our customer base, especially our assembly division. Over time, when POs were being placed, we were always asked, can we have the PCBs assembled and delivered as a final product? With such a high level of interest, we decided collectively to go in that direction.
Beaulieu: So you provide what I like to call total concept: circuit design, layout, fabrication and assembly?
Switzer: Yes absolutely. So many of our customers were asking us to provide the complete service package that it was an obvious decision to start doing just that. Our President, Sam Sangani, likes to say that we sell convenience, and I think he is correct.
Beaulieu: I agree with Sam. I think today our customers are looking for a more convenient way of doing business and certainly offering total concept under one roof provides convenience, to say the least.
Switzer: PNC’s total concept company makes us very unique in the industry. For those customers looking for efficient and expedited turn times, it’s become a big advantage over our competitors. I’d say most competitors who advertise the same practices actually have to subcontract portions of that work out, which makes turn time efficiency and quality control more difficult to control.
Beaulieu: I consider it a true service for the future, and you have it here today. I am quite sure that in a few years many others are going to follow your lead. Let’s talk some more about your technology. What capabilities do you have at PNC?
Switzer: Our PCB manufacturing capabilities increase with technology demands yearly, including 3/3 trace space; .250 thickness panels; blind and buried vias; controlled depth routing and drilling; controlled impedance; filled vias both conductive and non-conductive; PTH down to .006, using an array of materials from FR-4 to polyimide to Rogers ceramic and PTFF, aluminum clad and a number of hybrids. With regard to controlled impedance, we are seeing the demand for that increasing all the time.
Page 1 of 5
Suggested Items
Meet the Author Podcast: Martyn Gaudion Unpacks the Secrets of High-Speed PCB Design
07/10/2025 | I-Connect007In this special Meet the Author episode of the On the Line with… podcast, Nolan Johnson sits down with Martyn Gaudion, signal integrity expert, managing director of Polar Instruments, and three-time author in I-Connect007’s popular The Printed Circuit Designer’s Guide to... series.
Intervala Hosts Employee Car and Motorcycle Show, Benefit Nonprofits
08/27/2024 | IntervalaIntervala hosted an employee car and motorcycle show, aptly named the Vala-Cruise and it was a roaring success! Employees had the chance to show off their prized wheels, and it was incredible to see the variety and passion on display.
KIC Honored with IPC Recognition for 25 Years of Membership and Contributions to Electronics Manufacturing Industry
06/24/2024 | KICKIC, a renowned pioneer in thermal process and temperature measurement solutions for electronics manufacturing, is proud to announce that it has been recognized by IPC for 25 years of membership and significant contributions to electronics manufacturing.
Boeing Starliner Spacecraft Completes Successful Crewed Docking with International Space Station
06/07/2024 | BoeingNASA astronauts Barry "Butch" Wilmore and Sunita "Suni" Williams successfully docked Boeing's Starliner spacecraft to the International Space Station (ISS), about 26 hours after launching from Cape Canaveral Space Force Station.
KIC’s Miles Moreau to Present Profiling Basics and Best Practices at SMTA Wisconsin Chapter PCBA Profile Workshop
01/25/2024 | KICKIC, a renowned pioneer in thermal process and temperature measurement solutions for electronics manufacturing, announces that Miles Moreau, General Manager, will be a featured speaker at the SMTA Wisconsin Chapter In-Person PCBA Profile Workshop.