-
- News
- Books
Featured Books
- pcb007 Magazine
Latest Issues
Current IssueThe Hole Truth: Via Integrity in an HDI World
From the drilled hole to registration across multiple sequential lamination cycles, to the quality of your copper plating, via reliability in an HDI world is becoming an ever-greater challenge. This month we look at “The Hole Truth,” from creating the “perfect” via to how you can assure via quality and reliability, the first time, every time.
In Pursuit of Perfection: Defect Reduction
For bare PCB board fabrication, defect reduction is a critical aspect of a company's bottom line profitability. In this issue, we examine how imaging, etching, and plating processes can provide information and insight into reducing defects and increasing yields.
Voices of the Industry
We take the pulse of the PCB industry by sharing insights from leading fabricators and suppliers in this month's issue. We've gathered their thoughts on the new U.S. administration, spending, the war in Ukraine, and their most pressing needs. It’s an eye-opening and enlightening look behind the curtain.
- Articles
- Columns
- Links
- Media kit
||| MENU - pcb007 Magazine
All About Flex: Flexible PCB: What’s in a Name?
November 25, 2015 | Dave Becker, All FlexEstimated reading time: 3 minutes
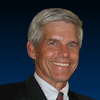
Flexible PCB is a common term that is synonymous with flexible circuits. While the term “PCB” is generally used to describe rigid printed circuitry, “flexible PCB” is a little contradictory because “boards” aren’t really flexible. Some companies, like All Flex, design and manufactures flexible PCBs, but not rigid PCBs.
There are many similarities between the two, but also significant differences.
Design
The shortest distance between two points is a straight line, so a circuit trace on a flex circuit should look like a circuit trace on a rigid circuit board, right? Actually there can be considerable differences between designing a rigid PCB and a flexible PCB. Because of the flexibility feature, there are unique issues affecting robustness. For example, since flex can bend, one needs to be sure that bending does not crack or break solders joints near a bend location. For this reason, design features like radiused corners and filleted pads are common on flexible circuits. Another issue is that the substrate used for flex is not as dimensionally stable vs. its rigid cousin. Allowances for dimensional changes may be required for flexible PCB design. Most PCB design software is tailored to rigid printed circuit materials and features. Tradeoffs occur when this same software is used to design flexible PCBs[1].
Fabrication
Rigid PCBs and flexible PCBs have very similar fabrication steps and often use the same equipment and equipment manufacturers. For example, photo imaging the base circuitry layer can use virtually identical technology. The differences arise because of the difference between handling a rigid board versus a flexible substrate. Some ultra-thin circuits are extremely flimsy and need special material handling systems. While a PCB is relatively easy to handle, a thin flexible circuit may need special clamping, fixturing or vacuum systems to hold it in place while processing. Some very high-volume flexible PCB manufactures process circuits in a continuous reel (reel-to-reel). Reel to reel processing uses significantly different material handling mechanisms vs. systems processing discrete panel sizes.
Tooling
Both PCBs and flexible PCBs use similar tooling such as CAD files, photo tools and electrical test fixtures. Perhaps the biggest difference is around the cutline definition. Flexible circuits provide unlimited configuration opportunities that often results in very odd shapes and sizes. Circuit boards often are rectangular or may have some notches or curved outlines routered. Because of this nuance, steel rule dies and hard tool dies are probably used more often for flexible PCBs than for boards, at least for ultra-high-volume applications. Laser definition of the circuit outline is also a common flex circuit process. Other differences in tooling involve fixturing that may be required to handle flexible substrates.
Coverlay/Covercoat
Flexible PCBs require different dielectric materials such as flexible photoimagable soldermask or laminated coverlay (also called coverfilm) vs. the non-flexible PCBs. This creates materials with unique properties and challenges. Materials need to bend and flex, with some applications requiring millions of cycles, without cracking or delaminating. Several design features need to be considered with dynamic flex applications, including: copper grain direction, circuit pattern layout, coverfilm thickness, and trace geometries. The most common flexible dielectric is laminated film dielectric bonded to the substrate with high temperature and pressure, a solution rarely used for rigid PCBs.
Applications
Flexible PCBs constitute about 10–15% of all PCBs produce globally, so there are far more applications that use hardboards than flex. The biggest advantage for flex is that it can reduce the size, weight and amount of hardware used for many electronic packages. It is best described as an “electronic interconnect packaging solution.” The concept of an “origami flex circuit” also comes to mind. If you have an application that requires multiple planes of interconnections, or there are active bending or flexing requirements for parts of the package, then a flexible PCB may be your best choice.
References
Dave Becker is vice president of sales and marketing at All Flex Flexible Circuits LLC.
Suggested Items
I-Connect007 Editor’s Choice: Five Must-Reads for the Week
07/11/2025 | Andy Shaughnessy, Design007 MagazineThis week, we have quite a variety of news items and articles for you. News continues to stream out of Washington, D.C., with tariffs rearing their controversial head again. Because these tariffs are targeted at overseas copper manufacturers, this news has a direct effect on our industry.I-Connect007 Editor’s Choice: Five Must-Reads for the Week
Digital Twin Concept in Copper Electroplating Process Performance
07/11/2025 | Aga Franczak, Robrecht Belis, Elsyca N.V.PCB manufacturing involves transforming a design into a physical board while meeting specific requirements. Understanding these design specifications is crucial, as they directly impact the PCB's fabrication process, performance, and yield rate. One key design specification is copper thieving—the addition of “dummy” pads across the surface that are plated along with the features designed on the outer layers. The purpose of the process is to provide a uniform distribution of copper across the outer layers to make the plating current density and plating in the holes more uniform.
Trump Copper Tariffs Spark Concern
07/10/2025 | I-Connect007 Editorial TeamPresident Donald Trump stated on July 8 that he plans to impose a 50% tariff on copper imports, sparking concern in a global industry whose output is critical to electric vehicles, military hardware, semiconductors, and a wide range of consumer goods. According to Yahoo Finance, copper futures climbed over 2% following tariff confirmation.
Happy’s Tech Talk #40: Factors in PTH Reliability—Hole Voids
07/09/2025 | Happy Holden -- Column: Happy’s Tech TalkWhen we consider via reliability, the major contributing factors are typically processing deviations. These can be subtle and not always visible. One particularly insightful column was by Mike Carano, “Causes of Plating Voids, Pre-electroless Copper,” where he outlined some of the possible causes of hole defects for both plated through-hole (PTH) and blind vias.
Trouble in Your Tank: Can You Drill the Perfect Hole?
07/07/2025 | Michael Carano -- Column: Trouble in Your TankIn the movie “Friday Night Lights,” the head football coach (played by Billy Bob Thornton) addresses his high school football team on a hot day in August in West Texas. He asks his players one question: “Can you be perfect?” That is an interesting question, in football and the printed circuit board fabrication world, where being perfect is somewhat elusive. When it comes to mechanical drilling and via formation, can you drill the perfect hole time after time?